Contractor hand-digs “excavations” in crawl space under building
By James McRay
When your state’s Capitol Building is almost 150 years old, it’s going to require constant renovation and modern upgrades. This is true for Michigan’s Capitol in Lansing, which has been renovated many times since its original construction in 1872. That includes, of course, the renovation of the beautiful architecture in the building, which the public can see and enjoy. But it also requires the modernization and upkeep of the building’s almost-150-year-old plumbing.
It is the out-of-the-way, behind-the-walls, and under-the-building renovation that can be most challenging for renovation contractors. For example, Hoffman Bros. Inc.—headquartered in Battle Creek, Michigan—was recently tasked with preparing a section of the Capitol’s sanitation system for slip lining, including sections of pipe installed in the original 1872 construction of the building.
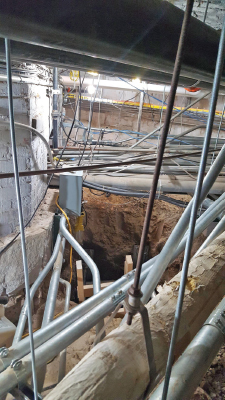
The installation of the new cured-in-place resin pipe lining required three excavations: a feeder hole, an alignment hole, and a draw hole for the winch to pull the lining through the pipe. Hoffman started the excavation project by digging an easy 2-foot-deep feeder hole on the north end of the Capitol grounds outside the building. However, it was the second and third excavations under the Capitol building that was anything but easy.
“Both the alignment and draw holes needed to be dug in a 5-foot crawl space with pipes and conduits running everywhere,” explains Aaron Mast, Hoffman’s superintendent. “Once we were in the correct spot in the crawl space for the alignment hole, we then had to dig an 8-foot-deep hole, which was partly under a conduit 2 feet off the floor.”
TRENCH PROTECTION SYSTEM
Making matters even more challenging was that the hand-dug “excavations” were deeper than 5 feet, which MIOSHA stipulates must employ one of the three approved trench protection systems: sloping, shielding, or shoring. Mast needed help finding a workable shoring solution, so he turned to the specialists at Efficiency Production, one of the nation’s leading trench shielding and shoring manufacturers, conveniently headquartered 20 miles south of the Capital in Mason, Michigan.
“We’ve dealt with Efficiency on a lot of different excavation projects in the past, some using trench shields, some with Slide Rail Systems,” says Mast. “So, I called (Efficiency’s Michigan sales and rental manager) Jim Hamilton, because I knew neither trench boxes nor Slide Rail was going to work for this project.”
“When I came out to the Capitol and saw where the Hoffman guys were digging—under the building in a crawl space where you couldn’t even stand up straight in most spots—I knew that the best thing—really the only thing—that would work for trench protection was hydraulic shores,” Hamilton says.
UNIQUE SHORING CHALLENGE
Hydraulic vertical shores consist of a pair of strong 8-inch aluminum rails that are connected by hydraulic cylinders. The hydraulic cylinders are pressurized outside of the excavation with a hand-pump. Where trench shields are used to protect workers against cave-ins, hydraulic shores are used to actually apply pressure to trench walls to prevent cave-ins—a critical consideration for shoring the 4×6 foot pits in the tight space directly below the Capitol’s famous Rotunda.
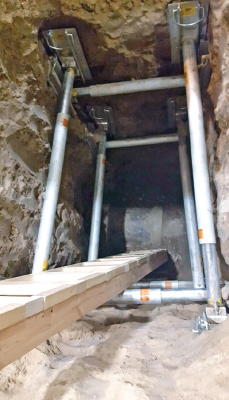
“Another thing that made hydraulic shores the only thing that would work was that all equipment needed to go down a 2-foot square access hatch to reach the utilities under the Capitol,” Hamilton continues. “The Shores, plus pump bucket and tools, needed to be carried down the access ladder by hand.”
EXCAVATIONS HAND-DUG
Of the two hand-dug excavations under the Capitol, the alignment hole was about 8-9 feet deep, but there was only 4-4.5 feet of overhead space. The second hole for the winch was 6 feet deep and dug with only 4-5 feet of overhead space. To shore the pits, Hoffman employed eight, single-cylinder hydraulic “spot-shores”—four running in each direction. When activated, the hydraulic pressure from the cylinders prevents the trench walls from collapsing.
CLOSING THOUGHT
“I hadn’t ever heard of hydraulic shores before Jim explained how they worked; and sure enough, they were slick and did the job,” Mast says. “We have a lot of traditional Efficiency trench safety equipment in our fleet, but I wouldn’t hesitate to use hydraulic shores again if we encounter a problem that can’t be addressed by something we already have in our toolbox.”
About the author:
James McRay is the director of marketing and media for Efficiency Production. He can be reached at 800.552.8800; james.mcray@arcosa.com. Efficiency Production, ™America’s Trench Box Builder™,∫ is an Arcosa Shoring Products company. Efficiency’s versatile trench shielding and shoring systems are designed specifically for safe and cost-effective installation of utility systems and infrastructure improvements. For more, visit www.efficiencyproduction.com.
Modern Contractor Solutions, February 2020
Did you enjoy this article?
Subscribe to the FREE Digital Edition of Modern Contractor Solutions magazine.
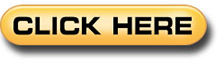