Colorbiotics has successfully completed the first 3-year test cycle of their soybean-derived polymer at the National Center for Asphalt Technology’s (NCAT) Test Track at Auburn University.
Biomag™ Hot Mix is a new generation of polymer asphalt additive, designed for high-traffic and heavy-load applications such as interstates and highways. “It consists of one part of our soybean rejuvenator (Invigorate) and one part soybean-derived polymer,” explains Austin Hohmann, product manager for Colorbiotics, Ames, Iowa. “It is a hyperbranched polymer that helps to interconnect and extend the styrene butadiene styrene domains within asphalt.”
According to Nam Tran, associate director at NCAT, this is the first biobased polymer of its kind undergoing lab and track testing at NCAT. “We have tested some rubber-based polymers, but polymers are typically derived from petroleum. The purpose of the polymer is to improve the rutting and cracking resistance of the binder.”
Soybean plants help to reduce CO2 levels in the atmosphere. Plants absorb CO2, a benefit for the environment and sustainability efforts. “Polymers made from plants and trees can be considered carbon negative, possibly offering carbon credits,” adds Tran.
Further environmental benefits are reaped along the production chain of bio-based polymers. “On average, it takes two pounds of oil to make one pound of polymer,” offers Hohmann. “By contrast, it takes just under one pound of soybean oil to make one pound of polymer.” Test results so far also indicate that the mix design may be optimized to increase the amount of RAP used to make the asphalt mix.
PASSING GRADE
Biomag includes soybean oil to improve the resistance of asphalt binders to oxidative aging. It was blended at an asphalt terminal and delivered to East Alabama Paving, who produced the mix paved at the test track.
The difference between the two new surface mixes tested by NCAT showed only in the type of virgin asphalt binders. Test Track Section W10 was paved with mix using the asphalt binder modified with the Biomag biopolymer, while the control section E5A included the binder modified with the traditional petroleum based SBS polymer. “We produced a mix with the biopolymer that matched the SBS polymer control mix to get an apples-to-apples comparison,” offers Buzz Powell, associate director at NCAT and research professor at Auburn University.
Aggregate gradation for the surface mix included a 12.5-millimeter (0.50 inch) nominal aggregate size, and 20% RAP was introduced at a 12.5-millimeter (0.50 inch) size with 5.5% binder and granite aggregate plus a local sand. Volumetric design parameters for both included 4% air voids, 5.3% total combined binder content with a 4.9% effective binder, and a 2.5% maximum specific gravity.
Binder analysis was based on test results of both the virgin binders and the extracted plant-produced asphalt mixtures that included RAP. A PG 76-22 SBS modified binder was used for the control for E5A, while the supplied W10 experimental binder mixed at the terminal offered a performance grade of PG 70-16. Reviewing the binder test results, researchers noticed differences in the biopolymer when comparing the test results of the virgin and extracted binders.
The asphalt samples at the plant were mixed at a higher temperature than in the lab, and as a result, the extracted W10 biopolymer binder offered a high-temperature performance grade of 88˚C, like the E5A control mix. Additionally, the low-temperature performance of the extracted E5A binder increased from -22˚C to -16˚C, whereas the extracted W10 binder maintained its low-temperature performance of -16˚C. Both extracted mixes showed the same performance grading.
Hohmann explains the W10 performance improvement of the extracted binder. “There is a reaction that occurs when mixing plant temperatures that we didn’t anticipate happening. Between tank to pavement, the increase in heat catalyzed a reaction not seen in the lab. We thought the increased heat would extend the Biopolymer but didn’t realize it would help to mature it. Therefore, we can add RAP to the mix and increase the performance grade of the biopolymer binder.”
He also noted the Multiple-Stress Creep-Recovery test improvements from the virgin binder to the extracted binder. “With RAP introduced to the mix, the control sample’s performance lowered, while the Biomag Section W10 sample showed improvement to better than that of the control, which could indicate a better resistance to rutting,” Hohmann adds.
A series of standard mixture performance tests were also performed on the samples: Dynamic Modulus, Hamburg Wheel Tracking, Illinois Flexibility Test (I-FIT), Energy Ratio, Indirect Tensile Asphalt Cracking, High Temperature Indirect Tensile, Cantabro Percentage Loss, and Disc Shaped Compaction Tension tests. All results showed similar or minor performance differences between the control and experimental mixtures.
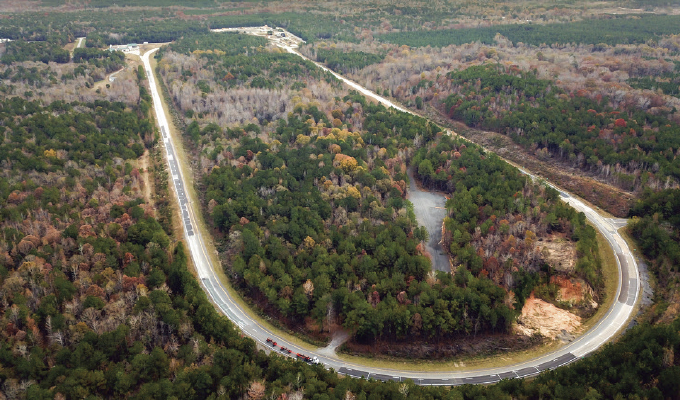
EXCELLING IN THE FIELD
Passing the test with minimal rutting, E5A showed only 2.4-millimeters (0.094 inch) of rutting and W10 had 4.7-millimeters (0.185 inch), well below the threshold commonly considered failing of 12.5-millimeters (0.5 inch). “These results are impressive, as you want some level of rutting of the mix. Otherwise, it will be too stiff, which can result in cracking. The experimental biopolymer binder asphalt is a healthy mix,” comments Powell.
The second 10 million EASLs cycle is scheduled for completion in 2024. Both Powell and Hohmann offer some thoughts about the Biomag W10 test results and the potential for optimizing the design. “As mentioned, the original goal of W10 design was to match the control mix with 20% RAP added. These test results indicate that the biopolymer produces a healthy mix that could be optimized for RAP content,” says Powell.
CLOSING THOUGHT
Hohmann agrees and adds, “A producer reaps significant ROI benefits at RAP content of more than 25%, as this saves on virgin binder and aggregate. We can achieve this with Biomag Hot Mix while offering cost, performance, and sustainability advantages for the producer.”
For More Information:
Colorbiotics, headquartered in Ames, Iowa, has been innovating products that enhance the beauty of homes, businesses, parks and athletic facilities for more than 30 years. Colorbiotics is the industry leader in the science behind landscape colorant, recreation surfaces and the equipment that makes them better. Colorbiotics is also transforming asphalt production and construction with environmentally friendly additives and topicals that restore flexibility of RAP and extend service life. For more information on markets and applications, visit www.colorbiotics.com.
Modern Contractor Solutions, May 2023
Did you enjoy this article?
Subscribe to the FREE Digital Edition of Modern Contractor Solutions magazine.
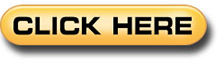