Experience can breed either innovation or stagnation. Recently, veteran contractor Kamminga & Roodvoets, Inc. (K&R), used their vast experience with Slide Rail Shoring Systems to successfully bid and perform two very challenging utility installation projects that required much innovation and ingenuity in how they implemented the popular excavation protection system.
“I’ve used Slide Rail Systems before, but not to this magnitude,” says Adam Khodl, project manager for K&R, describing the Efficiency Production manufactured Slide Rail System in a ClearSpan™ configuration. The trench protection system shored a 44 foot x 56 foot wide, and 32 feet deep excavation where K&R is installing a huge 40 foot x 50 foot cast-in-place lift station for the City of Muskegon, Michigan. “What I liked about (the Slide Rail System) is that even though it’s big, there are no cross-beams to get in the way of installing the lift station.”
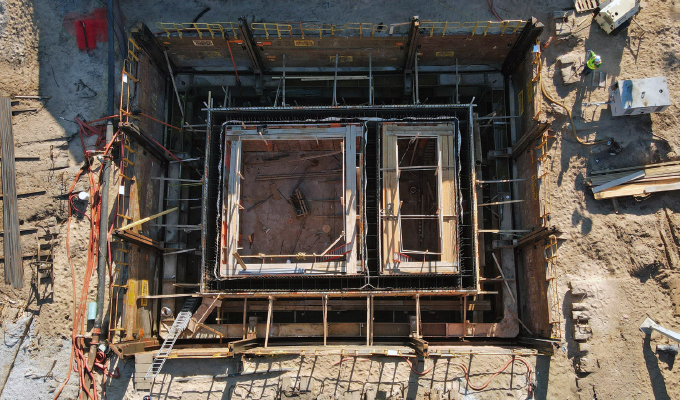
SHORING SYSTEM SOLUTION
Efficiency’s modular Slide Rail is a component shoring system comprised of specialized steel posts and panels. The versatile system can go 32 feet deep in a variety of configurations, such as small four-sided pits; large unobstructed excavations as big as 60 x 60 feet or more in a ClearSpan™ configuration; or in a Multi-Bay™ configuration to install tanks and other structures or lengths of pipe over 40 feet.
Slide Rail is installed simultaneously as the trench or pit is excavated by sliding the panels into integrated rails on the posts—an outside slotted rail first, then an open-face rail on the inside—then pushing the panels and posts incrementally down to grade as the pit is dug; a process commonly referred to as a “dig and push” system.
MUSKEGON PROJECT
“Muskegon is located just a few miles from Western Michigan’s beautiful Lake Michigan shoreline which means (K&R) were digging in the same sugar-sand that makes up those beautiful sand dunes on the beach,” explains Tim Hurst, director of Efficiency Production’s Special Operations Shoring Division. “It’s the dig and push installation process of the posts and panels—a little at a time—that allowed us to install the system down to grade in that soil,” Hurst says.
Efficiency’s ClearSpan™ configuration is unique to other manufacturer’s Slide Rail Systems in that it utilizes internal waler beams rather than cross-pit braces to support the system at deeper depths. “The walers on this system are different than on other Slide Rail that I have used in the past; they adjust with the system, so that was new to me,” says Steve Fox, K&R’s project foreman. “It’s a lot different but it’s clean. You don’t have to work around the walers and there are no crossbeams like other clear-span system. It’s a lot better system—a lot better.”
And that was just the first project.
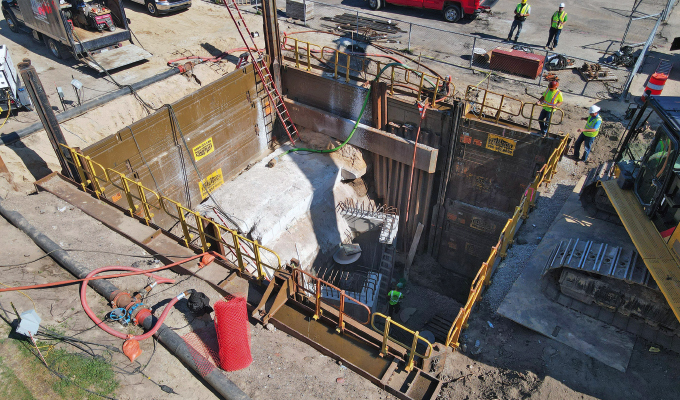
GRAND RAPIDS PROJECT
About 40 miles east of Muskegon, in downtown Grand Rapids, another crew from K&R utilized Efficiency’s Slide Rail System for a new sanitary sewer line. The contractor installed a 28 foot x 35 foot wide, and 24 feet deep Multi-Bay™ configuration with Shore-Trak™ Panel Sheeting Guides to shore tightly around an existing 11.5 foot x 14 foot sanitary sewer culvert. In the Slide Rail System, K&R caste-in-place a new 11 foot x 14 foot manhole structure up against the existing sewer line. The crew then sawed into the existing culvert and redirecting the line through the new manhole.
Once the manhole and diversion line were installed, the K&R crew backfilled the excavation and moved much of the same Slide Rail components to another spot right along Market Street and installed a 24 foot x 26 foot wide, and 28 foot deep 4-sided Slide Rail System to shore another section of the 96-inch diameter reinforced concrete pipe on the new half-mile long sewer pipeline.
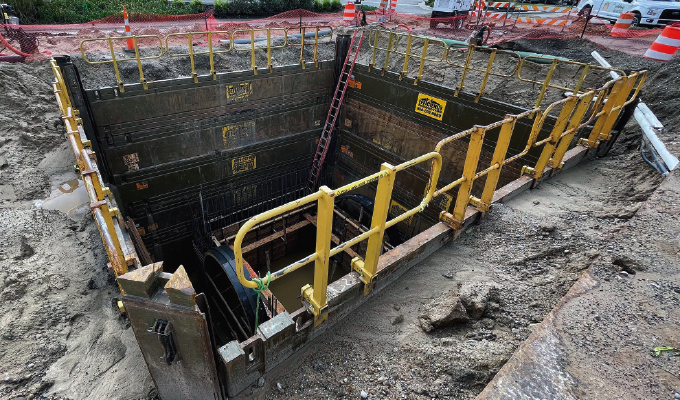
CLOSING THOUGHT
In 1951, Roger Roodvoets and Elwin Kamminga started a local bulldozing company, working out of Roger’s father’s garage. From that beginning, the two friends established the foundation for what has become an industry leader in roadbuilding and underground utility construction. With offices in Grand Rapids, Michigan, and Tampa, Florida, K&R has grown into a successful and highly regarded contractor with more than 200 employees, building projects ranging in size from city street intersections to highway interchanges.
About the Author:
James McRay is director of marketing & media with Efficiency Production, ™America’s Trench Box Builder™,∫ an Arcosa Shoring Products company. The company manufacturers and services the widest selection of standard and custom trench shielding and shoring systems. Efficiency’s versatile products are designed specifically for safe and cost-effective installation of utility systems and infrastructure improvements. All products are P.E. certified to meet OSHA standards. For more, call 800.552.8800 or visit www.efficiencyproduction.com.
Modern Contractor Solutions, February 2022
Did you enjoy this article?
Subscribe to the FREE Digital Edition of Modern Contractor Solutions magazine.
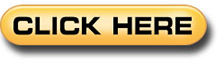