The key to maximum productivity is an efficient, well-maintained work truck. To keep your business running at peak potential for as long as possible, consider these four tips to optimize your fleet and get the most out of your work truck’s lifecycle.
1. SERVICE EQUIPMENT REGULARLY
Productivity is all about uptime. There is nothing worse than having a piece of equipment down when there is a job to be done. To maximize productivity, stick to the preventive maintenance and inspection schedules. Regular maintenance not only improves longevity, but it also ensures that your equipment is always running at peak performance.
2. SWITCH FROM A STEEL BODY TO AN ALUMINUM BODY
When choosing a body, consider the use of an aluminum body to reduce the weight of the truck. You can use the lower weight to reduce the wear and strain on a chassis. Alternatively, you can put those extra pounds to work for you by adding the tools and parts you need to get the job done. Along with careful payload management, a lighter body will limit the wear and strain on the truck. Aluminum is also a great option to reduce rust and corrosion. This will help your truck last longer whether you have harsh winter conditions, ocean-side climates, or work in a more corrosive environment.
In addition to aluminum bodies, consider equipping your fleet with aluminum work truck accessories like aluminum lube skids and aluminum storage systems. Additional aluminum accessories will also assist in reducing weight and increasing the longevity of the truck.
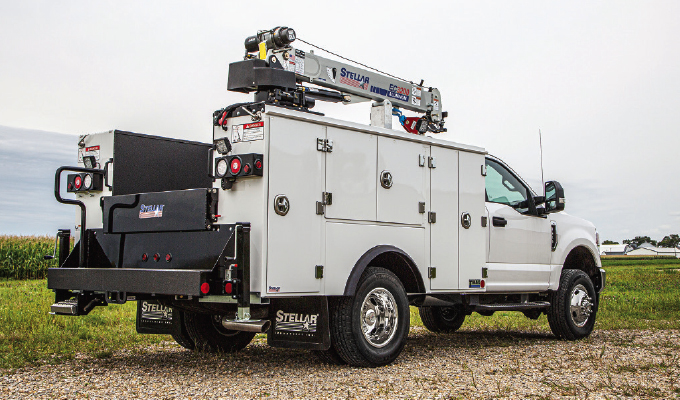
3. CONSIDER THE USE OF AN AUXILIARY POWER UNIT WITH INTEGRATED COMPRESSOR
Anything an operator can do to make their truck more efficient—and ultimately more productive—is a good thing. Converting to an auxiliary power unit (APU) with an integrated compressor is a great way to check both those boxes. In addition to an integrated compressor, these APUs often have a welder and generator.
Instead of running an individual air compressor, welder, and generator, consider upfitting your truck with an engine-driven, integrated solution. Not only are these systems more efficient than their modular counterparts, they can help on chassis maintenance and fuel savings as they don’t require the truck to run, utilizing their own engine in place of the standard PTO-driven air compressor configurations found on most work trucks. Some of these APUs can even be used to run the crane, eliminating the need for a PTO and idling in the chassis to run equipment.
4. ENHANCE EQUIPMENT WITH TECHNOLOGY
Chassis have included telematics systems for quite some time, with new enhancements each year. Telematics help fleet managers monitor maintenance needs, equipment usage, and truck lifecycles themselves, increasing the potential savings due to less downtime and fewer equipment replacements.
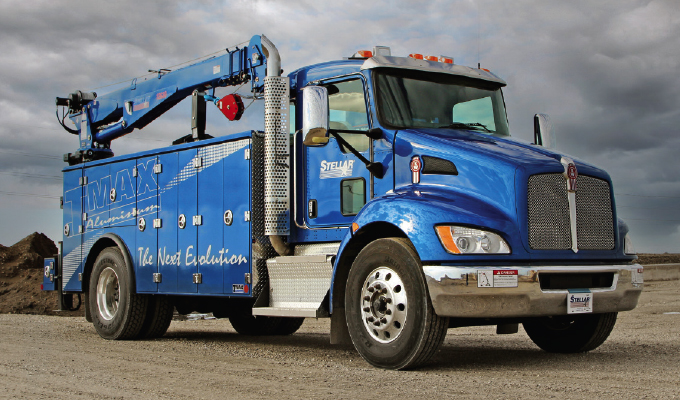
CLOSING THOUGHT
Whether you’re stepping up your maintenance game, switching to aluminum equipment for corrosion resistance, or just cutting weight to increase payload, always look to get the most out of your work truck. A well-maintained work truck means more uptime and more money in your pockets.
About the Author:
Adam Oppermann is a product manager with Stellar Industries. Stellar was founded in 1990 in Garner, Iowa, and has since expanded operations to four U.S. locations. Stellar is an employee-owned and operated manufacturer of high-quality work trucks and trailers, in addition to service truck and van accessories. Through the innovative, growing product line and an expanding distribution network, the company has gained an international presence and become the number one productivity choice in many markets. For more, visit www.stellarindustries.com.
Modern Contractor Solutions, March 2022
Did you enjoy this article?
Subscribe to the FREE Digital Edition of Modern Contractor Solutions magazine.
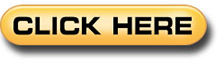