By Larry Trojak
Florida, for all its natural beauty, robust economy, and enticing climate—key components in the state drawing more than 300,00 transplants per year—is not without its shortcomings. The development needed to sustain that massive influx frequently meets a challenge in the area’s high water table. Projects which would be fairly straightforward in another location are often forced to bring in or move tremendous volumes of fill onsite. In order to avoid the cost and headache of importing possibly a million or more cubic yards of soil, companies tackling larger Florida projects often create new lakes, using that material elsewhere onsite to raise site elevations and alleviate the high water table issue. To make that happen in the most efficient manner possible at “Wild Blue,” a huge residential development project in the Ft. Myers area, Mitchell & Stark Construction (MSC) is drawing upon the strengths of GNSS technology for both the dredging/shore sloping and earthmoving facets of the operation. The end result has been nothing short of impressive in terms of time and effort saved. Company officials say their success can be linked to one key principle which also happens to be a hallmark in the construction-related GNSS realm: handle the material as little as possible. With that at the forefront … off they went.
MSC GOES ALL IN
Despite the proliferation and broad acceptance of GNSS solutions across the construction spectrum, it is still impressive to learn when an organization with no GPS experience embraces the technology in a big way. MSC is one of those companies—and “in a big way” is a huge understatement. In a mere two and half years, the company has transformed itself from one that was content with the status quo, to a virtual poster child for forward thinking through technology.
According to Chris Anderson, MSC’s project manager, in 2016, after lengthy consideration, the company recognized the benefits that could be gained through embracing GNSS systems and, more importantly, saw the different areas in which those benefits could be realized.
“We literally had nothing GPS-related at that time and jumped in with both feet,” he says. “That year, working with Lengemann, the Florida Topcon dealer, we purchased eight excavator systems and six dozer systems. In spring/summer of 2018 we added another four systems: two dozers and two excavators. And, in addition to all that, we have two excavators and two dozers that are fully wired and ready for serialized components. So, if a machine is headed to the shop for any reason, we can simply use that machine’s system on one of the wired replacement machines. It’s a way for us to ensure we have 100 percent utilization of our capital investment.”
THE LAKES OF WHICH …
A good portion of MSC’s work involves development of large-scale planned communities throughout southwest Florida. In addition to the 3,000-acre Wild Blue, the company is actively involved in work at Collier Preserve, Sorrento Grove, Anguilla, La Mirada, and a massive 15,000-acre development called Babcock Ranch. Located between Naples and Ft. Myers, Wild Blue is being done in phases—the first one will have roughly 500 homesites while subsequent phases will be larger and denser. Using a range of GNSS solutions, says Anderson, has dramatically changed their approach to such projects, starting with creating the site’s lakes.
“In addition to their obvious aesthetic value, creating lakes provides direct, tangible benefits,” he says. “Controlling algae blooms caused by runoff, is one such example. To help ensure that, the South Florida Water Management District, the governing entity for all the waterways in the region, requires that there be a specific acreage of lakes for every acre of property being developed. From a company perspective, creating a lake can improve onsite efficiency. Material from just one lake excavation on this site—about a half million cubic yards of soil—will be used as a source for some of the 2 feet to 5 feet of fill needed to get everything above flood plain elevation.”
While they are free to dewater an existing lake in order to excavate in a fairly dry condition, such is not the case in some of MSC’s other projects. Anderson says that, at developments closer to the Gulf, SFWMD prohibits dewatering for fear of saltwater intrusion into the base aquifer.
“In those cases, where digging under water while maintaining the 4:1 or 6:1 slopes is necessary, the Topcon X53i system is invaluable for us,” he says. “The technology has made looking at marks on the stick of the machine—a slow and laborious task—a thing of the past. Now an operator is able to look at his screen and see the bucket under water, relative to where they need to be. His or her work becomes little more than a material handling operation—it’s been amazing for us.”
FEEL THE EARTH MOVE
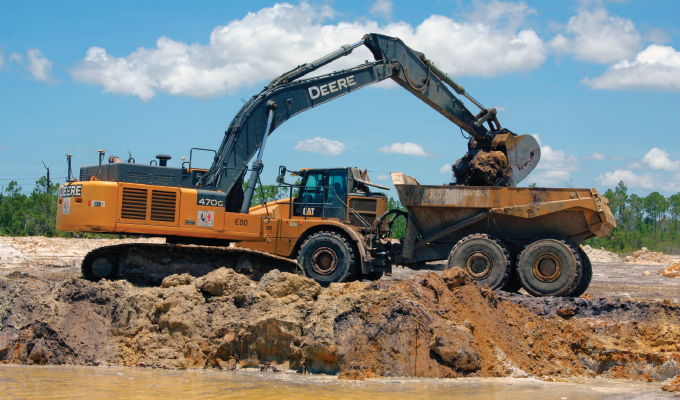
MSC is handling the earthmoving facet of the project with excavators, haul trucks and a fleet of dozers equipped with Topcon 3D-MCMAX machine control systems. While they have dramatically reduced the number of stakes on site—a byproduct of GNSS-based machine control—doing so was not their primary goal, according to Anderson.
“I have a manufacturing background, so I know that double-handling material is a waste of time, effort and money,” he says. “We specifically use the Topcon-equipped dozers because we are trying to touch the ribbon fill once—any reduction in staking is just icing on the cake. Using the dozers, we are doing the bulk of the mass fill and getting it to within +/- .1 (feet) of where it needs to be for each home site. The accuracies are impressive.”
In addition to the accuracies the technology provides, Anderson says they gravitated towards the Topcon 3D-MCMAX system because the major components are not exposed to the elements like other blade-mounted systems.
“Because a South Florida jobsite can be a harsh environment, we want as much of our value protected as possible,” he says. So, removing one of the most field-critical components, the controller, from the mast and placed either in the cab or in a location where it will not be exposed to the sun, rain, and thieves, is huge for us.”
CONNECTING IT ALL
Dealing with multiple, large jobsites, in locations which can easily be more than an hour’s drive away from the office, is commonplace for MSC. Doing so has historically proven to be, at best, a challenge—at worst, a productivity-killer. However, when the company migrated to GNSS, they also opted to embrace Sitelink3D, a communication and management solution offered by Topcon. Designed as a means to provide office-to-machine, machine-to office, and machine-to-machine connectivity, Sitelink3D has proven invaluable to MSC as its jobsites—and client list—continue to grow.
“Sitelink3D is extremely helpful for us in so many areas, including quickly identifying and resolving discrepancies between what an operator is seeing on the screen and what the stake is showing,” says Anderson. “The same holds true for engineering changes. There have been a number of modifications on this project to where a lake bank has shifted, or they’ve had to extend a littoral shelf. That’s easily resolved now.”
He adds that, in the housing market, if one type of home isn’t selling, it is not uncommon for the developer to redo the lots and replat it with the new home selection. “That obviously changes the ribbon fill,” he says. “Using Sitelink3D, I can make all those changes from my desk and immediately get a new file out to the machines.”
CMS has also found the solution to have real value as a user training interface. He cited one project in which they were laying some very large pipe and the operator, while experienced, was used to dealing with machine control on dozers, but not excavators.
“On a dozer, you only need to load the surface on the model,” he says. “However, on this job, there were different trenches and, because I set them up as alignments, our operator was unsure how to jump back and forth between them. Being able to be on the phone with him and see what he was clicking on the screen—or being able to take control of the screen itself—saved me a huge amount of time in getting things resolved. Our projects are spread out all over this region, so you can see the tremendous savings just in trip time; reducing travel by 4 or 5 hours per week is not uncommon. We draw upon the benefits of Sitelink3D almost daily and always seem to be finding new ways to use it.”
MORE TO COME
The fact that lots at the developments at Wild Blue are selling out very quickly bodes well for additional company growth, both in terms of business and equipment purchases. While adding a GNSS control capability to motor graders is high on their to-do list, in order to augment some of the work currently done by dozers, they have already started making moves in other areas.
“Because of the degree to which we use GNSS systems, all our sites are localized, so a move into aerial topography using a drone made a lot of sense for us,” he says. “We tried to keep our capital investment down, so we purchased a mid-range priced UAV, but we still process our digital images through AgiSoft from Topcon to generate our 3D spatial data with the accuracies we need.”
He adds that they’ve found a good deal of success using the UAV to gather accurate data for verifying conditions on jobsites.
“Having to import fill is a huge line item that can easily surpass $1 million on a sizeable project,” he says. “This is a fast, efficient, cost-effective, and accurate way to determine what the existing conditions are. We always strive to give our clients the most accurate info possible so they’re budgeting correctly. That helps ensure their success and profitability and, by extension, ours as well.
CLOSING THOUGHT
To get up to speed during the period when MSC was transitioning into GNSS, Anderson attended “Point Man” training sessions at Topcon’s Livermore, California, training center. “Those sessions were very helpful, since I had no background in this technology,” he says. “I gained solid insight into both the hardware and the software, and turned what I called ‘unknown unknowns,’ into ‘known unknowns.’ Between that experience at Topcon and the help from Lengemann—first Tom Walrath, and later, Trey McKinney—MSC was in good shape.
“My old boss used to say: ‘variance is the enemy of efficiency,’ and I think that holds true in this industry as well,” he continues. “At MSC, we are trying to turn construction into more of a manufacturing environment model where we can control as many variables as possible. With the Topcon solutions and the ways in which we use them, I am able to push that scale of variables a little bit more towards the good side.”
about the author:
Larry Trojak is president of Trojak Communications, a Minnesota-based marketing communications firm. He has written for the construction, recycling, demolition, scrap, and aggregate processing industries.
Modern Contractor Solutions, July 2020
Did you enjoy this article?
Subscribe to the FREE Digital Edition of Modern Contractor Solutions magazine.
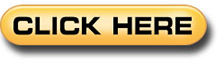