By Brent Trenga, LEED AP BD+C
Talk is cheap, but a future without action on climate change is detrimental to us all. We’ve seen recent news coverage of record-breaking brushfires in Australia, heatwaves in India, and even reports on threats to national security. Last year, NASA and NOAA found temperatures on Earth are the warmest since recordkeeping began. It’s clear the climate change crisis has reached an existential level. The lives of future generations depend on a unified, global effort to cut carbon emissions.
The building industry accounts for 39 percent of the country’s carbon dioxide emissions, according to the U.S. Green Building Council. Those manufacturing building materials, designing buildings, and constructing them have a responsibility to mitigate their impacts on the climate crisis for generations to come.
Some of the largest cities on each coast of the United States are taking action. Los Angeles will require all new buildings to be emissions-free by 2030 and all existing buildings will have to be retrofitted to meet the same goal by 2050. That same year, New York City will aim to achieve a net zero carbon economy.
One of the Big Apple’s newest neighborhoods is already working toward that goal. Hudson Yards bills itself as a “template for the future of cities,” featuring the instantly recognizable “Vessel” building, shops, restaurants, offices, and public spaces. As Manhattan’s first LEED Gold certified neighborhood, Hudson Yards features sophisticated energy and stormwater management solutions. For visitors, residents, and office workers, the neighborhood is filled with links to New York City’s public transport, helping to achieve a vision of fewer cars in Manhattan’s congested streets.
While Hudson Yards is a shiny new example for how major cities can work toward a sustainable future, the past remains a challenge, and it’s all around us. It’s time we turn our attention to the existing skyline. In order to truly make an impact, existing buildings must be retrofitted to reduce carbon emissions. The most recent U.S. Energy Information Administration survey found as many as 81 percent of commercial buildings were built before 2000.
Despite the environmental advantages and potential cost savings, The Brookings Institute estimates only one to two percent of existing building stock is renovated each year. We must start looking at the investment required from top to bottom to see how retrofits can be a game-changer for our planet.
GREEN FROM THE GROUND UP
The supply chain and the materials selected for any retrofit deserve careful consideration for their environmental impact. By carefully selecting the building materials, architects and specifiers can improve a building’s carbon footprint before the contractors break ground.
According to Architecture 2030, embodied carbon is responsible for 11 percent of overall global greenhouse gas emissions and 28 percent of global building sector emissions. When sourcing materials, architects and building owners should prioritize those with lower embodied carbon levels. This requires a critical look at the most prevalent material: concrete. A 2018 report found that cement, the primary ingredient in concrete, contributes to about 8 percent of global carbon emissions.
With more manufacturers making environmental product declarations available, building designers are able to see how the materials are not only created, but how they can be recycled or reused in the future. Steel produced in North America has been proven to have lower greenhouse gas emissions than Chinese steel. Its lifecycle continues with its recycling and reuse. Databases, like the Carbon Smart Materials Palette, can help guide decision making.
Whenever possible, locally-sourced materials are ideal to cut down on carbon emissions from transportation (Scope 3 emissions). The Brookings Institution found trucks to be responsible for 3 percent of greenhouse gas emissions and 1.6 percent of shipping.
HVAC AND INSULATION: THE HEAVY HITTERS
A retrofit is an opportunity to take advantage of better technology. Think back one decade ago. There were no apps allowing you to control the temperature of your home or smart thermostats, keeping track of your movements and habits. With 40 percent of total U.S. energy consumption attributed to buildings, an upgrade to HVAC systems can make a significant difference in both reducing the building’s carbon footprint and long-term energy costs.
Even skyscrapers can become energy efficient with a retrofit. Chicago’s iconic Willis Tower—once the tallest buildings in the world—has cut its electricity consumption by 34 percent in the last 20 years. The team upgraded the heating and cooling system with new gas boilers, which use fuel cell technologies to run at 90 percent efficiency.
Another giant, the Empire State Building, cut down on its energy consumption by 40 percent. The project cut the number of air handling units in half to two per floor and used variable air volume units instead of constant volume. Digital controls were upgraded throughout the HVAC systems, allowing for easier monitoring. In addition, more than 6,000 insulated reflective banners were installed behind radiator units around the building’s perimeter to conserve heat.
Even if the exterior walls remain the same, insulation with a high R-value can improve the energy efficiency of any old building, which in turn, reduces carbon emissions. In 2017, the International Energy Agency found that two-thirds of buildings need to be covered by mandatory building energy codes by 2025 in order to outpace carbon emissions from new builds.
Newer technologies incorporate greener manufacturing practices with better thermal performance—making insulation a critical measure for any retrofit. Upgrades in the building fabric are a one-time way to save energy for years to come. Newer materials prevent air and moisture from passing through the façade, allowing for better temperature control. They can preserve heat in cooler climates and protect from the sun’s powerful rays in warm, humid locations. A high-performance building envelope does not require extra energy to function, once installed, providing passive energy efficiency at no extra cost.
The 2010 deep energy retrofit of the Castle Square Apartments in Boston resulted in a dramatic energy reduction. The 1960s mixed-use building was constructed with porous, uninsulated concrete and brick infill walls with aluminum slider windows and through-wall air conditioning units. The building envelope played a major role in improving the energy efficiency of the affordable housing units.
Insulated metal panels were applied directly over the brick and concrete in order to create a high-performance shell with improved thermal resistance. An additional mineral fiber layer provided thermal continuity and a water resistive barrier. Combined with a new insulated roof, windows and energy-efficient appliances, within just 2 years, Castle Square’s savings on gas ranged between 48 and 64 percent. The project was LEED platinum certified and won the Vanguard Award from the National Affordable Housing Management Association.
A LIGHTER WAY TO CUT CARBON
Gutting a building is not an option for everyone. It can be a time-consuming and costly process. There are some small adjustments that can make a big difference. One of them is so simple, many people have already made the change at home.
While the United States reversed a law that would have banned energy-inefficient light bulbs this year, many other countries have phased out older bulbs. While typically more expensive, LED bulbs use 75 percent less energy and last 25 times longer than incandescent bulbs, according to the U.S. Department of Energy.
The Departments of Veterans Affairs and Navy in North Chicago, Ill. reduced energy consumption by 15 percent in just one year by replacing fluorescent bulbs with LEDs.
Along with new light bulbs, motion-activated light switches can also reduce energy usage by ensuring the lights are off when no one is around. Digital timer switches can now connect to a smart phone app, allowing for further control.
While reducing water use is a concept that has been around for decades, there is still work to be done. The Environmental Protection Agency estimates that 17 percent of the withdrawals from public water supplies are from the commercial and industrial sector. In order to reduce water use, office buildings, hotels, restaurants, and hospitals can update bathroom and kitchen fixtures to more efficient models.
One of the biggest benefits can be for the irrigation. By checking leaks and installing new technology, the grass can be greener, and with less water. The Granite Park complex in Plano, Texas, has reduced irrigation water use by 40 percent. Starting in 2008, a team upgraded traditional timer controllers to weather-based irrigation controllers, installed pressure regulating nozzles on the sprinkler heads and instituted a routine maintenance schedule. In 2009, the cost savings was $47,000.
CLOSING THOUGHT
New advances in technology and a better understanding of building materials give architects and project managers a way forward when dealing with buildings constructed decades in the past. As we look ahead to the future, building a more sustainable city does not require a wrecking ball, but a vision for how to weave green ideas into the fabric of what is already there.
about the author
Brent Trenga, LEED AP BD+C, WELL AP is building technology director for Kingspan Insulated Panels North America (www.kingspan.com). His background as an architect, construction manager, developer and project owner give him a unique perspective on all facets of the construction industry. Trenga leads Kingspan North America’s material health and transparency program and Kingspan’s North American NZE 2020 program, while collaborating with the company’s global healthy building team. Trenga can be reached at brent.trenga@kingspan.com.
Modern Contractor Solutions, May 2020
Did you enjoy this article?
Subscribe to the FREE Digital Edition of Modern Contractor Solutions magazine.
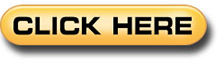