These days, contractors are looking for solutions to move quickly, reduce downtime, and increase productivity. One way this can be accomplished is through logistics/material handling.
Logistics helps companies complete jobs more efficiently in a shorter timeframe. While the construction industry has increased productivity by only three percent in the past 40 years, Faith Technologies, an energy expert and national leader in electrical planning, engineering, design and installation, is working to increase productivity by 20 percent in less time through the implementation of jobsite logistics.
WHAT IS LOGISTICS IN CONSTRUCTION?
Logistics is based on Lean/Six Sigma construction principles, and the concept of having materials, parts, equipment, and tools available at the point of use when they are needed, not too far before and not too late.
This philosophy is modeled after manufacturing operations and is similar to the Toyota Production System, also called the “Toyota Way.” One of the principles of the Toyota Way is “just in time,” which means that parts arrive at the time they are needed. This reduces workspace clutter and enables operations to run smoothly. It also means that Toyota only stocks the inventory that is needed at that time, which reduces their physical footprint.
The concept is the same for logistics. Implementing jobsite logistics personnel and systems enables Faith’s electricians to focus on their role, which is installing equipment, running wire, etc., and they have all the tools, parts, and equipment to do so, thanks to the logistics team. These two separate roles allow operations to run more efficiently and at a higher level of productivity.
Logistics helps skilled workers reduce secondary time, which is time spent setting up tools and equipment, deploying from place to place, operating equipment or anything else that is done on a jobsite beside the actual installation. The goal is to increase skilled workers’ primary time, which is time spent doing the job they are trained for. For instance, an electrician is trained to pull wire, do installs, hang fixtures, etc., and the amount of secondary time they spend on a project site decreases profitability and increases time spent on the project.
Deploying a jobsite logistics team helps eliminate busy work that can slow a contractor down. How do they do that? Logistics personnel will set up the job area ahead of the electrician with all of the tools and equipment needed so the electrician can focus on the installation. The logistics team will also procure any additional materials needed throughout the course of the job, work to fill equipment and tool orders, and anticipate jobsite needs. This could include moving lifts or ladders, setting up toolkits, or providing ice and water, ensuring that the skilled worker doesn’t have to stop what he or she is doing in the middle of a job to take care of these tasks. Additionally, the logistics team will clean up the area after the task is completed and have the next area set up for the electrician to begin working on.
WHY IMPLEMENT LOGISTICS?
Customers pay contractors for primary work. They are not paying a contractor to move materials, organize and find tools, clean up or redeploy to other parts of the project. Higher amounts of primary time accomplished by your craft professionals will drive business productivity and profitability and decrease secondary and waste time.
The goal is to have the logistics team take those tasks from the skilled workers, so they can focus on the tasks that the customer is paying them to complete.
In a recent study, Faith Technologies compared how much of an impact the logistics team added to the productivity of a jobsite. Without the logistics team, 60 percent of time was spent doing primary work. When logistics was integrated, primary time increased to 73 percent and waste time decreased by eight percent.
A recent evaluation by Faith’s Productivity Team during an electrical bracket installation showed that output levels doubled once logistics was deployed.
LOGISTICS SKILL SET
Those who thrive in a logistics role are people with backgrounds in warehousing, manufacturing, or storage operations. They should also have experience with and an understanding of technology, such as iPads or laptops to monitor and manage materials coming and leaving a jobsite, and to track upcoming project scheduling and needs. The role of technology on the jobsite will only continue to increase, and logistics personnel should work to stay ahead of trends in the industry.
Logistics professionals should also have strong leadership skills. They may be responsible for managing multiple people, from a team of five or six up to a team of 60 to 70 people in large organizations. Logistics is responsible for assigning people to set up certain worksites, cleaning others, and ordering or processing new materials coming on to the jobsite, based on the skills and abilities of their team members. They work hand in hand with superintendents and project managers to ensure tasks are being completed as efficiently as possible.
CONCLUSION
Today, logistics is a somewhat uncommon process within the construction industry. However, with the skilled labor shortage, we will likely see logistics implemented by construction companies focused on continuous improvement. As the construction industry becomes more productive, contractors will need to step up their productivity in order to remain competitive.
About the author:
Mike Machurick is the director of logistics at Faith Technologies. In this role, he manages the logistics team and ensures they have the proper training and materials needed to increase productivity on the construction site. To learn more about Faith Technologies or its logistics department, you can reach out to Mike at mike.machurick@faithtechnologies.com.
Modern Contractor Solutions, February 2019
Did you enjoy this article?
Subscribe to the FREE Digital Edition of Modern Contractor Solutions magazine.
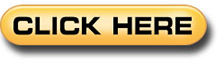