According to the Plastics Pipe Institute, Inc. (PPI), it is now possible for small towns such as Youngsville, Louisiana, with a population of 8,100, to afford a high-end sports complex using cost-effective drainage products such as corrugated high-density polyethylene (HDPE) pipe.
The Youngsville Sports Complex is a 70-acre complex that opened in May 2014. The complex has six soccer, four softball, and five baseball fields, ten tennis courts, a one-mile long walking path, fully stocked fishing pond, a playground, plus concession stands, shops, and facilities for festivals and corporate events.
The use of corrugated HDPE pipe on the site reduced the cost for the drainage system portion of this public-funded project. Large diameter corrugated HDPE pipe along with in excess of 500 catch basins were used to construct the drainage system for this community’s new multi-sport complex.
“We are certainly seeing expansion of the trend to provide underground drainage to community sports facilities,” states Tony Radoszewski, president of PPI. “Players, management, owners, and fans have always wanted a way to get water off the field quickly. In the old days, the only way to prevent rain from getting on the field was to roll out the tarp, but that would often kill the grass. Or for local fields, the games were just canceled, and many times the field was unplayable for several days. Underground drainage systems were developed that would collect and move the water.”
The pipe used at Youngsville also provided an environmental advantage. The MEGA GREEN® Series of Advanced Drainage Systems, Inc. (ADS) N-12® corrugated HDPE pipe is made with at least 40 percent recycled content. More than 23,800 linear feet of the pipe in diameters ranging from 10-48 inches was used on the project. MEGA GREEN pipe provides both strength and optimum hydraulic capacity with a Manning’s “n” rating of 0.012. It meets ASTM F2648 standard specifications and will support H-25 live loads.
The drainage basins were ADS Nyloplast® Water Control Structures. Other types of pipe considered for the project included PVC and concrete. Design engineering firm, C. H. Fenstermaker, selected HDPE pipe due to its favorable price, shallow burial depths, ease of installation, long life, and the recycled content of this particular product.
“Most times the fundamental concept for a sports complex facility is that drainage be handled in a conservative fashion,” explains Dax Douet, P.E., engineering director for Fenstermaker. “Too many times I have seen facilities that are at the minimum slope requirements or don’t provide enough drainage so both players and spectators walk through mushy ground and mud. I was determined not to have that happen. We have a lot of slope everywhere on our fields. We designed the Youngsville drainage system for a 10-year storm event.”
PLAYING CATCH WITH WATER
Basins were another key to the rapid water drainage. Douet elected to use Nyloplast structures which combine a ductile iron grate with a rugged, heavy–duty PVC structure.
“The Nyloplast catch basin has about a 6-inch sump underneath the pipe connection,” Douet explains. “I really liked that we used them. On a sports complex like this, they will apply a lot of fertilizer on these fields, and I thought it was a great idea that each of these catch basins had a sump, which basically allows sediment and runoff fertilizer to drop out the pipe, cross over the catch basin, and into the sump. The use of these drainage structures helped improve our water quality outflow into our drainage features.”
A+ GRADE
To get the grade and slopes as accurate as possible on all the playing fields, Douet had the construction crews use GPS equipment along with laser levels.
“To understand every nook and cranny of this park and how it drains, we actually created a 3D ground surface of this entire park to know exactly where we would need to catch the water and put the catch basins.”
“All the fields, common areas, and parking lots could be graded only with GPS equipment that had a vertical tolerance of 1/100th of a foot,” he continues. “The contractor used laser levels and GPS units following my 3D model. This way I would get exactly the drainage I wanted. That’s my biggest takeaway—if I was going to do a facility like this again, I would do it in the same way. The only way to do it right is to utilize the technology that the construction world has today and that’s with equipment that has a global positioning system.”
Douet made the call to put in native soil as backfill for all subsurface drainage not under the loading of vehicular traffic.
“As far as backfill, we originally bid the project using aggregate backfill, which is really what that pipe calls for, but when we bid the project, we were over budget, so I really needed to find areas where I could save money. One of the choices I made was to allow native soil to be put back in the trench, but only in areas that weren’t subject to traffic. Where the pipe is underneath parking lots, however, that was backfilled with aggregate. For most of the complex, there’s no weight on top of it, just people walking on it. I think we saved about $700,000 by allowing earthen backfill.”
RAINING ON THE PARADE
The storm water management system was put to the test just before the grand opening event, but Douet wasn’t worried.
“About 3 days before the grand opening, we had close to a 9-inch rain within 12 hours. That’s a major rain event,” he states. “And about 4 hours later, all the water was out and about. None of the fields had a drop of water on them.” ■
For More Information: The Plastics Pipe Institute Inc. (PPI) is the major trade association representing all segments of the plastic pipe industry and is dedicated to promoting plastics as the material of choice for pipe applications. For additional information about HDPE pipe and storm water drainage, visit www.plasticpipe.org.
_________________________________________________________________________
Modern Contractor Solutions – January 2016
Did you enjoy this article?
Subscribe to the FREE Digital Edition of Modern Contractor Solutions magazine.
Where the Water Runs
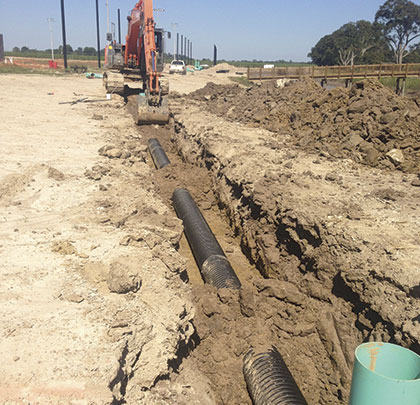