It’s hard to find an industry running without the use of lubricating greases. As per one estimate, more than 90 percent of roller bearings are grease lubricated. Historically, the use of grease to lubricate wheels and axles were known to mankind to date back to 1600 B.C. or even beyond. Until recently, there has been phenomenal progress in terms of machine design, operating parameters, and in the advancement of lubricating greases. Lubricating greases primarily consist of a thickener (10-15 percent) which acts like a sponge, base oil (80-90 percent) as dispersion, and lubrication media and performance additives (5-10 percent) for boosting grease performance. The total worldwide lubricating greases market size is about 2.48 billion pounds consisting of lithium/lithium complex, calcium, aluminum/aluminum complex, calcium sulfonate, clay base, polyurea, etc. By far the most popular greases worldwide are lithium base greases with a market share of more than 75 percent. In countries like China, its market share is more than 85 percent, and in India it’s even more than 90 percent.
The main raw material for making these lithium base greases is lithium hydroxide and the availability is getting scarcer day by day. This is because the resources for lithium mining are limited and lithium is being increasingly used in making lithium batteries for electric vehicles and mobile phones. The cost of lithium hydroxide is sky rocketing, and in India its cost within one year has increased 5 to 6 times, making this class of greases economically unviable. It’s becoming increasingly important to look for alternative sources. Out of many conventionally available types of grease in the market, the best suitable candidate appears to be calcium sulfonate grease. Most greases are incompatible with lithium greases, except for calcium sulfonate grease.
THE BEST IN THE BUSINESS
A careful comparison between better lithium and calcium sulfonate grease delineates that calcium sulfonate greases holds better ground over lithium greases. Calcium sulfonate grease outperforms lithium and lithium complex greases in tests and field applications. The unique feature of calcium sulfonate greases is that they do not necessarily require performance additives to meet the certain performance levels, whereas lithium and lithium complex greases need substantial amount of additives to level calcium sulfonate performance level. Calcium sulfonate greases exhibit superior mechanical and shear stability compared to lithium complex greases, thus indicating less leakage and runout during operations. The dropping point and high temperature life of calcium sulfonate greases is much better than lithium greases enabling them to operate at higher temperatures. Calcium sulfonate greases possess inherent extreme pressure and anti-wear properties over lithium complex greases.
Sulfonates are known be natural rust inhibitors, and therefore, calcium sulfonate greases, by virtue of its thickener property, possesses excellent water resistance properties and doesn’t break down in the presence of water. Additionally, calcium sulfonate greases are more compatible with lithium/lithium complex greases than other greases. The only limiting factor with calcium sulfonates greases is their inferior pump ability and cost; however, recent advancement in the calcium sulfonate thickener chemistry enabled them to be similar to lithium greases. The increasing cost of lithium hydroxide has brought price parity close to each other, therefore making calcium sulfonate greases more commercially viable.
Calcium sulfonate greases have outstandingly been used in mining and construction industry since this class of greases has a high tolerance to dirt, dust, and a humid environment.
LITHIUM GREASES
Multi-purpose grease in simple terms can be defined as the grease that combines the properties of two or more specialized greases which can be applied in more than one application. For example, lithium grease can be applied both in chassis and wheel bearing applications of transport vehicles. Historically, calcium greases were used as chassis and soda (sodium) base greases used as wheel bearing greases. Calcium base greases were rated as excellent greases for water resistance, but poor for high temperatures. Soda base greases, on the other hand, could cover high temperatures, but were poor on water resistance. Lately, lithium greases have made an appearance in the market and have been found to be superior to calcium and soda base greases. The lithium greases have become the most popular multi-purpose greases in the industry. The bearing temperature under normal conditions in a multi-utility vehicle does not exceed beyond 250 degrees F, therefore lithium greases meticulously became the universal choice in the transport sector as a multi-purpose grease. ■
About The Author: Dr. Anoop Kumar has a Ph.D. in chemistry from Indian Institute of Technology (Roorkee) India. With nearly 25 years’ experience in the field of lubricants and greases, Dr Anoop is the director of R&D and business development with Royal Mfg Co LP.
_________________________________________________________________________
Modern Contractor Solutions – March 2016
Did you enjoy this article?
Subscribe to the FREE Digital Edition of Modern Contractor Solutions magazine.
What’s Next After Lithium Greases: Calcium Sulfonate Complex Greases
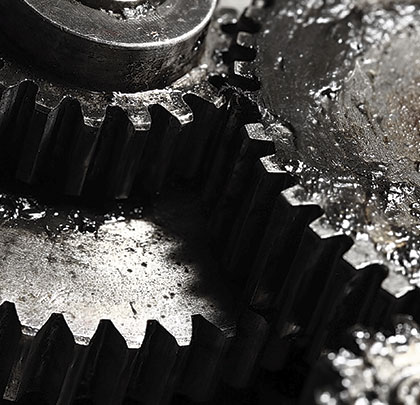