Recently, contractor RedStone Construction Group was low-bidder to install a sanitary sewer wet well for North Little Rock (Arkansas) Wastewater. The 25-foot-tall, 8-foot-diameter fiberglass wet well was installed along 10th Street in North Little Rock, Arkansas.
The installation of a pre-cast structure with sewer tie-in was really nothing new for RedStone. However, the depth of the excavation and its proximity to the Arkansas River presented a new wrinkle for the veteran underground utility crew. Plus, the excavation site was packed into a very small working area.
“We only had about a 25-foot radius of space around where the wet-well was going to go, so we didn’t have any room for sloping or benching,” says Kurt Cosse, RedStone’s project supervisor. “We knew we needed some type of non-traditional shoring system that would allow us to minimize the impact of the excavation area.”
UNIQUE SHORING CHALLENGE
RedStone turned to local heavy-equipment dealer Riggs Cat for possible solutions to their unique shoring challenge. “RedStone came to us and we looked at their project parameters and saw that they had a really tight confined area that they were going to put the lift station in,” says Riggs’ rental operations coordinator, Josh Clark. “So they asked us, what options do you have for shoring and we were able to show them an Efficiency Production Slide Rail System.”
“We’ve worked with Riggs pretty much since we’ve been in business, they’ve always been there for us,” says Cosse. “Just recently, Riggs has got into the trench safety rental business and they happened to have this shoring system that we needed and everything kind of fell into place from there—it’s just a good match.”
EFFICIENCY DEBUTS IN ARKANSAS
Efficiency Production’s Universal Slide Rail System is a component shoring system comprised of steel panels—similar to trench shield sidewalls—and vertical steel posts. When installed, the versatile system creates a safe, obstruction-free shored excavation.
“From the get-go, all the parts were right and what we needed,” Cosse says. “On previous jobs, we’ve had problems with shoring material not being the correct one, or not showing up at all. But from day one when we got the Slide Rail System, everything came that was required to install it.”
Featured Image: A 25-foot radius of space existed where the wet-well was going to go; there wasn’t room for sloping or benching.
Above: It took about a day to install the Slide Rail System, which was half the time RedStone Construction Group thought it would take.
INSTALLATION ASSISTANCE
Both Cosse and Clark were very impressed with Efficiency’s Shoring Specialist, Dan Meredith, who provided factory-direct installation assistance. “Dan was competent and knew exactly what he was doing,” insists Cosse. “He had very good patience and was a very good teacher. By the end of just one day, our crew could install the Slide Rail System by themselves.”
Meredith is part of Efficiency Production’s Special Operations Shoring Division. “It was great working with both Riggs Cat and RedStone, three different companies coming together for a common objective,” Meredith says.
Adds Clark, “I observed how Dan worked with and handled the crew and I was very impressed with him because he still interacted with RedStone’s crew on a level to where he could control what needed to be done and make the Slide Rail go into the ground effectively and efficiently, but he also showed that respect to those professionals that were there with Red Stone,” says Clark about Meredith. “It takes a special person to blend into a crew like that and Dan did that seamlessly.”
SMOOTH INSTALL SAVES TIME
Slide Rail is installed by sliding the steel panels into integrated rails on vertical posts, and then pushing the panels and posts incrementally down to grade as the pit is dug. “It took about a day to install the system which was half the time we thought it would take,” says Cosse. “I think that if we’d used another type of shoring or didn’t have Dan on site, it could have taken twice as long.”
RedStone rented from Riggs the Slide Rail equipment to shore a 14 x 14 foot excavation, 20 feet deep. They installed the system with a Cat 330F and Cat 323F excavators, plus a Cat frontloader.
RedStone Construction Group has been serving Arkansas for over 35 years, offering a wide range of services including excavation and earthwork, underground utilities, concrete, and asphalt paving and repairs. Visit www.redstone-cg.com for more information.
Headquartered in Little Rock, Arkansas, Riggs CAT is one of the oldest Caterpillar dealerships in the United States. Riggs CAT employs over 400 people statewide with personnel and facilities in El Dorado, Fort Smith, Jonesboro, Russellville, Springdale, and Texarkana, Arkansas. More information can be found at www.riggscat.com. ■
About the Author:
James McRay is the director of marketing and media for Efficiency Production, Inc. He can be reached at 800.552.8800; jmcray@efficiencyproduction.com. Efficiency Production provides the widest selection of standard and custom trench shielding and shoring systems. All products are P.E. certified to meet OSHA standards. For more information, visit www.efficiencyproduction.com.
_________________________________________________________________________
Modern Contractor Solutions, July 2017
Did you enjoy this article?
Subscribe to the FREE Digital Edition of Modern Contractor Solutions magazine.
Wet-Well Near the Arkansas River
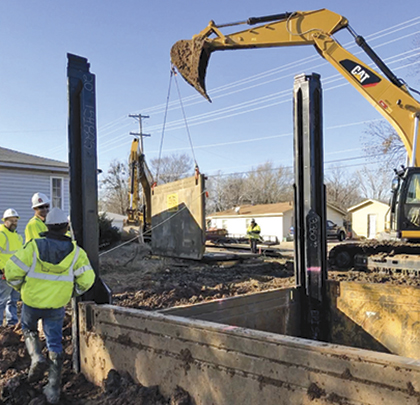