Self-shielded flux-cored welding is frequently used for structural construction and other jobsite welding since it offers a significant productivity advantage compared to stick welding.
Welders using this process are likely holding their welding guns for much of the day, and they may be standing on elevated girders or lifts trying to get into tight places to complete a weld. Because of this, it’s important to choose a self-shielded flux-cored gun that is comfortable, lightweight and maneuverable to help get work done efficiently.
Here are several key factors to consider when selecting a self-shielded flux-cored welding gun and tips for properly maintaining it to optimize performance.
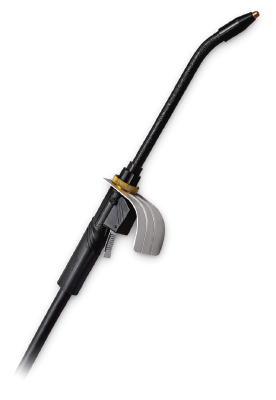
1. FLUX-CORED GUN OPTIONS
Not every welding gun fits every application. They come in various amperages and configurations, with features that include heat shields, configurable necks and adjustable cable lengths. The key is finding a flux-cored gun that works for each welder, since many options come down to operator preference.
2. AMPERAGE
Guns rated at 350 or 450 amps are common in structural field welding applications. Guns rated at 600 amps are also available but used less often due to being heavier. It’s important to avoid undersizing the welding gun since it can lead to overheating and other problems.
When selecting the gun amperage, consider the wire sizes that will be used most often. Typical wire sizes for a 350-amp gun are 1/16 inch and smaller. Wire sizes for 450-amp guns are 0.72 inch and larger, including 5/64 and 3/32 inch.
3. REPLACEABLE OR FIXED CABLE LINER
Some self-shielded flux-cored guns are available with either a replaceable cable liner or a fixed cable liner. The demanding environments where self-shielded flux-cored welding takes place can be hard on the gun and consumables, so replaceable liners provide benefits. They offer quick and easy cable maintenance and can extend product life, since welders can change out components that have high levels of wear. Guns with replaceable liners also tend to have a lighter weight cable and provide more flexibility to weld around edges or corners.
Guns with fixed cable liners are often larger, which can be an issue when welding in tight spaces. The cables are also typically stiffer and more rigid, so they can take more abuse. Once a fixed cable liner has reached the end of its useful life, the entire gun must be replaced.
4. NECK
Gun necks are available in varying lengths and bend angles. The choice for the application often comes down to operator preference or weld joint access and configuration.
A slimmer neck provides a better view of the weld pool and improved access to tight areas. A shorter neck typically provides more control compared to a longer neck. Still, operators may prefer a longer neck to increase the distance between themselves and the heat of the weld puddle — especially in higher amperage applications.
Keep in mind that lightweight, rotatable necks help reduce operator fatigue by aiding with posture and positioning, and they improve weld visibility.
5. TRIGGER
In the field, triggers that get wet or covered in dirt still need to work, so it’s important to purchase a quality gun that includes a durable trigger. Look for a gun with an enclosed trigger. This protects the contacts inside a housing, so the trigger is less prone to wear and breakage.
If you’re using a replaceable cable liner, it may have an internal or external trigger lead. Be aware that external trigger leads may require more maintenance because they can easily get snagged or catch on things like bolt heads. However, they are typically quick and easy to replace.
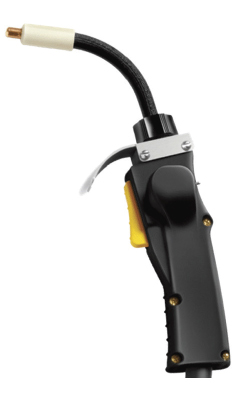
6. HANDLE
A handle needs to be rugged and durable for the jobsite, but it should also feel comfortable in the operator’s hand.
A self-shielded flux-cored gun with an optional dual schedule switch allows for wire speed adjustment while welding. In some guns, this switch is integrated into the handle to keep it protected from spatter. The ability to toggle between weld parameters easily—without having to stop welding and change settings—saves time and improves productivity.
THE BEST RESULTS
Beyond choosing the right gun for the job, it’s also important to use and maintain it properly. Consider these tips for optimizing gun performance.
Store and handle it properly: Jobsites can be dusty, dirty places. Be sure to store guns and cables properly when not in use. Roll the cables up and put the gun away in a clean, dry place so there’s less risk it will be damaged.
Maintain it as needed: Keep the gun and all components clean and check all connections periodically. Loose connections can cause electrical resistance and heat buildup, which can result in premature wear. Take the time to regularly blow out the liner with clean, compressed air to remove dirt and debris. Immediately address any damage to the gun components with maintenance or replacement.
Invest in quality consumables: Consumable choice often comes down to cost or operator preference. However, investing in high-quality consumables can help extend the life of the gun, provide better performance and reduce downtime for changeover.
CLOSING THOUGHT
The self-shielded flux-cored process can deliver significant benefits for productivity and efficiency. Choosing the right gun and components—and maintaining them properly—plays a key role in optimizing your results.
About the Author:
Stephen Bennett is a mechanical engineer with Bernard. For more, visit www.tregaskiss.com.
Modern Contractor Solutions, June 2023
Did you enjoy this article?
Subscribe to the FREE Digital Edition of Modern Contractor Solutions magazine.
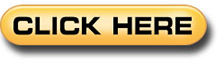