As a proud fourth-generation family company, C.D. Smith Construction Inc. is able to point to hundreds of hospitals, schools, factories, and churches in its home state of Wisconsin as examples of the quality start-to-finish building projects the general contractor takes on across the nation.
C.D. Smith also recently completed the process to become certified by the American Institute of Steel Construction (AISC), a mark that sets the quality standard for the structural steel industry and is the most recognized national quality certification program for the industry. Certified companies go through rigorous initial evaluation and are subject to annual audits. C.D. Smith trained about 60 workers to prepare for the process and completed a comprehensive administrative review, a documentation audit, and an on-site audit to receive the certification.
To keep its crews humming along on jobsites and providing welds worthy of the AISC certification, C.D. Smith turns to another company with deep Wisconsin roots, Miller Electric Mfg. Co. of nearby Appleton. Miller manufactures the engine-driven welder/generators used to power tools and equipment, often before permanent power is established.
ON THE JOB WITH MILLER EQUIPMENT
At the 250-foot-by-100-foot expansion of a Ryder frozen foods packaging and distribution center in Beaver Dam, Wisconsin, C.D. Smith Construction not only used its traditional Miller Bobcat™ 250 welder/generators, but also a new gas-powered Trailblazer® 325 during the structural steel construction.
“Welding on a job of this particular size is probably half of the job,” says Tom Pitzen, foreman, C.D. Smith Construction. “The welding requirements on this job are bar joists—3 inches of weld on each side of the bar joist. The trusses get bolted down and, after they’re bolted, the other requirement is a 3-inch weld to help hold them down.”
In addition, structural welding on the bar joists—or horizontal bridging—required a 11/2-inch weld on every support, top and bottom. The decking required 5/8-inch welds.
On this job, C.D. Smith crews completed the new building’s foundation work, structural steel, and concrete flooring, as well as outside roadways, sidewalks, and landscaping.
“When a job first starts, we’ll very seldom have power to that jobsite, so we always have to use some sort of a generator to get things going,” says Pitzen. “On this particular job, we have no outside power right here, so if we have to run a saw, a drill … everything will run off of the welder/generator. If we’re in a corner and we need lights, we’ll plug a cord in.”
The Ryder frozen foods facility expansion project provided Pitzen’s first opportunity to use the gas-powered Trailblazer 325, and he was impressed. Beyond the ability to power circular saws, hammer drills, and other tools where no permanent power source was available, the unit provides a high-quality weld.
PEACE AND QUIET
With the optional Excel™ power, the Trailblazer 325 provides 120 volts of pure sine wave generator power, enough to run most jobsite tools at idle speed, even when the welder is at work. Connecting to the Excel power receptacle provides up to 2,400 watts of generator power to run grinders, chop saws, drills, and lights with tangible results, says Pitzen, whose crews often work in noise-sensitive locations, such as hospitals under expansion.
“Noise on a jobsite is a big thing,” he says. “Without having that motor ‘kick up’ when striking an arc or powering a tool, the Trailblazer 325 will keep crews working at times they would otherwise have to tamp down or even shut down particular operations.”
Noise levels can be cut by more than 50 percent because the machine runs at the speeds it needs, not always automatically at high speed, explains John Van Meter, product manager for Miller.
“Most jobsite tools with Excel power run at idle speed. Most welding applications run at idle speed. The machine only goes to a higher speed when it needs to for heavier weld modes,” he says.
The new Bobcat welder/generators, designed with the engines relocated from the rear to the front, also are quieter than previous-generation models. The noise reduction benefits for the surrounding environment extend to the safety of the jobsite workers nearby.
“If you’ve got a lot of equipment running on your job, and if you’ve got welders nearby that are idling high and of course you have ear plugs in, it’s really easy to not hear a forklift or a skid steer backing up,” says Pitzen, who has nearly four decades in the construction industry under his belt. “The Trailblazer being such a quiet machine, you can hear a forklift coming around that welder.”
“At the end of the job, it comes down to cost: ‘Did you make money or did you lose money?’” Pitzen says.
With this machine, Pitzen can safely say the company made money. He estimates the Trailblazer 325 has saved the company 2 gallons of fuel per day on average over the older Bobcat 250
units. Pitzen estimates fuel savings alone from one welder/generator add up to about $1,500 a year; multiplying that by an entire fleet would mean thousands more in savings. C.D. Smith also sees savings from the employee hours gained by fewer trips to the gas station. The Trailblazer 325 is capable of run times up to 50 percent longer on a comparable tank of gas.
THE RIGHT COMBINATION
Having worked with C.D. Smith Construction for 35 years, Pitzen is a firm believer in the benefits of a combined, engine-driven welder/generator. The full, quiet output for both functions possible with today’s combined Miller models, he says, has the clear advantage over owning, hauling, and maintaining separate, dedicated units.
“By having everything in one unit, you’ve only got one motor running,” says Pitzen. “If you’ve got just a welder, and you need power and you have another generator alongside you running, you’re using twice the amount of fuel. With a welder/generator, it’s half the operating cost.”
And, as he says, “In construction today, it comes down to value and cost savings.”
■ ■ ■
[divider]
For More Information For more information on Miller equipment for your jobsite, call 920.734.9821, or visit www.millerwelds.com.
Modern Contractor Solutions, July 2014
Did you enjoy this article?
Subscribe to the FREE Digital Edition of Modern Contractor Solutions Magazine!
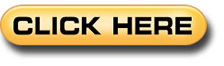