Water damage is an underrated threat on construction jobsites that can cause both acute and ongoing costs to contractors and project managers. With cold weather coming, there are also additional challenges faced protecting jobsites from the risk.
Meet Yaron Dycian, chief product and strategy officer at WINT-Water Intelligence, as he dives into the issues in the following Q&A.
MCS: What are the invisible costs related to water damage that construction companies don’t consider?
DYCIAN: Construction executives aren’t always afraid of water damage, and they should be. If they consider the prospect, most will think, “I’m insured, so I’m in good shape.” But the reality is they’re not.
Let’s start with deductibles. Contractors are paying out of pocket for any damage below the deductible. People usually don’t track those figures, so they add up. If your deductible is $25,000, and there are three water damage events on the project, that can ultimately cost $60-$70,000 out of your pocket.
Now, if you have a water damage event that you can submit to insurance, there is no guarantee you can recoup all the costs. Submitting the documentation is quite a complex process. It can take many months of work, and there are costs associated with that. Those invisible costs add up.
There are additional costs that become baked in over the long term. File big enough claims, and insurers will raise the deductible and next year’s premiums. Finally, there is the somewhat intangible but very real cost in reputational damage. If water damage incidents slow enough projects down, it will directly impact the contractor’s reputation. It might be hard to quantify, but reputational damage can cause real loss in future business.
MCS: What are the dangers facing the plumbing at construction sites during the winter?
DYCIAN: Obviously, the first is freezing. I’ve seen it multiple times on construction sites. There is water in the pipes, but the building is unoccupied and unheated. It’s not uncommon for someone to forget and leave a window open.
Now, during the weekend or during inclement weather, there is nobody there to see the window was left open, and the temperatures might already be in deep sub-freezing territory. And that cold temperature will hit an exposed pipe and cause it to burst. Indoor pipes are not protected against outside temperatures. It’s a very common situation.
Moreover, the plumbing in office building or typical large multi-tenant buildings will have tens of thousands of pipe fittings. All you need is one—just one out of those tens of thousands—to break. So, what are the odds that can happen? They’re pretty high.
In winter, jobsites can be unattended for stretches of time due to inclement weather or the holidays. And if these leaks are not discovered promptly, that one broken fitting in one of the upper stories of a building will result in massive damage. This can cost from hundreds of thousands to many millions of dollars based on the scale of the damage and the size of the project.
MCS: What technological solutions do construction companies turn to in order to prevent/mitigate water damage on jobsites?
DYCIAN: The first category to discuss is floor-based touch sensors. They’re old-fashioned technology that has been in use for decades. These sensors are, basically, just two wires in a container there are placed on the floor somewhere. If they get covered with water, it causes a short that the system detects and sends an alert message.
The problem is these sensors are merely reactive. If they don’t activate until they get wet, water has already been spreading. By the time an alert comes, significant damage can already have occurred. And even if someone receives the alert, they need to physically travel to the jobsite to shut off the water, losing time, while the damage continues to mount.
But innovations in leak prevention technology are giving contractors and developers the power to proactively mitigate water damage remotely. Advances in artificial intelligence and machine learning are being applied to water monitoring systems. This gives the systems the ability to learn normal water usage patterns on a jobsite or in a building in progress, alerting contractors or project manager when an abnormality is detected. The systems can also automatically shut off the water supply to the jobsite or building to avoid or minimize damage.
MCS: Are there any other components of water damage risk management to consider?
DYCIAN: Technology is part of the solution, but contractors need to take water damage as seriously as any other risk. A plan to mitigate water damage or loss should be in place at the beginning of a project. Incorporating the new AI-based water monitoring technology should be part of a broader plan that involves field management personnel, project partners, and even the risk management staff of the project’s insurer.
CLOSING THOUGHT
Ensure that water damage mitigation procedures and policies are known and used by any subcontractors. Remember, recognizing the water risk and preparing for the potential fail will pay off in the end.
For more information:
WINT is passionate about helping the world conserve one of its most precious resources, and the company is dedicated to helping businesses prevent the hazards, costs and waste associated with water leaks. Utilizing the power of artificial intelligence, the convenience of high-speed cellular data connections, and smart shut-off valves, Water Intelligence units provide an all-in-one solution for commercial facilities management teams looking to eliminate the fear of water-leak disasters and ongoing water waste. For more, visit www.wint.ai.
Modern Contractor Solutions, December 2020
Did you enjoy this article?
Subscribe to the FREE Digital Edition of Modern Contractor Solutions magazine.
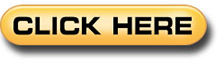