By Patrick Edwards
Imagine that you’re a fleet manager trying to meet aggressive goals tied to increasing profits and reducing costs, while also managing day-to-day operations. Responsibilities vary, but one thing is always top of mind: machine maintenance.
What if you could know that your dozer’s air filter is 80 percent full and has 58 working hours left? Or know the exact engine hours and location of your entire fleet, across every site?
With condition-based monitoring (CBM) tools, you can keep track of the health and location of every machine in your fleet and predict maintenance to keep your fleet running smoothly. CBM uses sensors to measure the status of an asset over time while it is in operation. The data collected can be used to establish trends, predict failure, and calculate the remaining life of an asset.
CHOOSE AN EFFECTIVE STRATEGY
From reactive to proactive approaches, there are many types of maintenance strategies utilized in the industry today. As the name suggests, reactive maintenance is simply responding to equipment emergencies as they come up. Reactive maintenance can be helpful for pieces of equipment that are not costly, failure-prone, or critical for operation. For instance, fleet managers might use reactive maintenance to fix a missing screw on the exterior of a dozer—a piece of hardware that isn’t likely to cause engine failure.
As the most widely used maintenance strategy in fleet management, preventive maintenance uses the philosophy, “If it ain’t broke, still fix it.” This is because fleet managers lack key data on the actual state of equipment. In turn, this forces organizations to service equipment to avoid potential failures, even if the equipment has a significant chunk of remaining life.
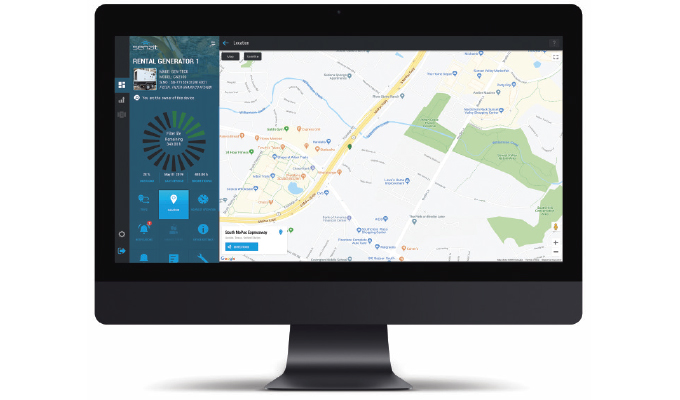
Taking it a step further, predictive maintenance strategies fill the information void left by preventive maintenance. Instead of relying on an outdated schedule to determine maintenance activities, predictive maintenance uses real-time equipment data and acts like an alert to notify you of potential problems.
That’s where CBM comes in, providing visibility into the actual state of your equipment. In turn, this data helps with predicting likely equipment failures and informs your maintenance schedule.
PREDICTIVE MAINTENANCE BENEFITS
While preventive maintenance can help avoid equipment failure, it also wastes resources. For example, it’s common to replace air filters simply because they look dirty. But this approach can lead to changing your filter before it actually needs to be replaced. Technician hours are wasted on unnecessary service tasks and downtime increases, which decreases your profitability.
In contrast, predictive maintenance helps avoid equipment failures while improving efficiency and maximizing your uptime. Utilizing CBM as a predictive tactic, you can take action based on air filter dust load—allowing you to get the most life out of the filter and replace it at the optimum time.
Fleet managers juggle a multitude of tasks, from managing people and delivering on time to ordering parts and reducing costs. Their time is valuable, and solutions that are easy to use are essential to helping them stay focused. Large or small, every fleet has a unique set of challenges. For fleets that rely on the fleet manager or operator to perform maintenance, transparency at all levels is imperative to maintain the highest level of efficiency and profitability. CBM empowers them with data to predict maintenance on all machines in the fleet, before a problem occurs.
SINGLE-SYSTEM APPROACH
Many predictive maintenance tools are installed at the OE level, and some may feel more comfortable with OE systems because of their integrated nature. But there are unique benefits to aftermarket CBM systems, especially for mixed fleets consisting of new and older pieces of equipment.
Top aftermarket CBM systems can be retrofitted to your entire fleet, so one dashboard provides a holistic view of the health and location of your entire fleet. This single-system approach allows you to sync maintenance based on the jobsite and machine conditions, share service records among multiple people on your team, and helps to prevent theft. Aftermarket CBM systems are also often priced at a fraction of the cost of OE systems.
PREDICTIVE AIR FILTER MAINTENANCE
As the industry’s first predictive maintenance platform to focus on increasing uptime for heavy-duty fleets, Senzit is an aftermarket tool designed to monitor air filters. Brand, equipment, and filter agnostic, Senzit can fit on any machine—from heavy construction equipment to generator sets.
Senzit is the only CBM software on the market that uses artificial intelligence (AI) and machine-learning algorithms to show an air filter’s dust load by percentage, and communicate remaining hours left on that filter.
Fleet and machine data is presented from a user-friendly web portal and mobile app. You can view the entire fleet, or look at specific aspects of a particular machine’s health to conveniently check on remaining air filter life, engine hours, real-time GPS, and equipment activity history. Mechanics can use the Senzit mobile app to remotely monitor equipment or locate equipment in the field and get driving directions to service it.
You can also use the Senzit reporting tool to improve maintenance cadence based on engine hours and dust load. This feature reports on which machines are used the most, and helps reduce overall downtime with optimized service intervals.
Custom alerts are another differentiating Senzit feature. Fleet managers can create custom alerts based on engine hours, dust load, and operating hours. Rental fleets can benefit from an alert to notify when the equipment is turned on outside of agreed-upon operating hours, allowing for breach of contract documentation and antitheft prevention.
CONDITION-BASED MONITORING
CBM is the future of maintenance, but this transition won’t be accomplished overnight. For your company, it can start with something as simple as predictive maintenance for air filters.
Preventive maintenance is nothing more than an educated guess based on your personal experience and manufacturer recommendations. CBM eliminates antiquated practices and relies on real-world conditions, delivering continuous monitoring along with accessible and easily digestible data. It is the gateway to syncing your service intervals based on the requirements of the job and your machine’s condition.
About the author
Patrick Edwards is a digital product owner at MANN+HUMMEL, currently leading the Senzit project, a predictive maintenance platform for heavy-duty fleets. MANN+HUMMEL is a leading global expert for filtration solutions, development partner and series supplier to the international automotive and mechanical engineering industry. MANN+HUMMEL launched Senzit in 2018 as its first digital product and the industry’s first digital air filter monitor. For more information, visit senzit.io.
Modern Contractor Solutions, July 2019
Did you enjoy this article?
Subscribe to the FREE Digital Edition of Modern Contractor Solutions magazine.
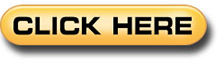