Does it seem to take you a while to find some things? Do you hear yourself muttering, “I know it’s here somewhere?” Do you find yourself burrowing through stacks of items to find one? Why do we repeat this?
The answer is simple—we have never realized the real value in “a designated place for every item.” In fact, we may actually find it humorous when we see a particularly organized person with a neat and pristine workplace or home and discount them as being anal retentive or obsessive compulsive. Perhaps we discount it with a statement like, “Well, someone has way too much time on their hands.” Actually, bringing order to a workplace or home has many benefits.
The 5Ss originate from a Japanese focus on organizing and bringing orderliness to the workplace. It represents the five pillars of the visual workplace (a way of bringing more orderliness and organization into the workplace through a structured approach). Each pillar’s name in the system originally was a Japanese word that started with “S.” We have converted it to begin with an English “S” word. Companies all over the world use the 5S system, because it aids in the creation and lifespan of a healthy, stable, efficient, and organized work environment. Without the 5S program in practice, or with only a few of the concepts in working order, an organization can become inefficient, chaotic, and extremely disorganized. In short, ALL of the elements of the 5S system need to be in effect for the process to work. The 5S system can be applied to your office, home, vehicle, or workplace environment … and work equally as well in each.
A HEALTHY WORK ENVIRONMENT
The 5Ss contribute to a safe and healthy work environment. They are the fundamentals which support standard operations, visual controls, workplace efficiencies, as well as other concepts. The 5Ss can also give an idea of the organization’s health.
Organizations that have difficulties implementing the system have chaotic, sometimes unsafe, and inefficient workplaces. Employees waste an inordinate amount of time searching and retrieving items.
LET’S EXAMINE EACH OF THE 5Ss:
Sort: Organize
This means removing items that are not needed in a particular work area, doing away with clutter, and keeping unnecessary items out of the work area to recover valuable space and provide improved safety.
Set in Order: Create Orderliness
This is organizing equipment, tools, documents, and materials by designing the most efficient space that is supportive of work flow. It also means creating structure that supports organization and neatness, making operations more efficient. We need a “home-site” for every item. The old adage “a place for everything and everything in its place” is the driver.
Shine: Executing Cleanliness
This means eliminating all dirt, dust, and grime; establishing ways of keeping dirt, dust, and grime from reappearing; inspecting to identify problems and beginning the correction process. This will create a more positive work environment. Cleanliness is a mindset we need to build. In addition, cleaning is inspection which allows us to find abnormalities and issues.
Standardize: Making Neatness a Standard
This approach is having standard ways of doing and sorting things so everyone can locate anything: creating checklists, standards, posters, and banners for communicating to everyone how things work, where things are supposed to be, and how to maintain the orderliness and organization standard.
Sustain: Turning 5S Principles into Habits
Making 5S principles a part of an organization’s culture and maintaining these principles will develop and maintain a clean, organized, and efficient work space. This is the toughest of the pillars to do as it involves sustaining the gains.
There are many reasons all organizations should implement the 5S system. It is an excellent beginning point for all improvement programs like Lean, Si Sigma, TPM, or TPR. It helps to create a stable environment that shows visible change occurring. We see a major metamorphosis with the visible changes.
There must be a stable environment present for any improvement process like Lean or Six Sigma to be successful. People who work in dirty or cluttered environments usually don’t notice the filth and disorganization because they are so used to it. So, if you don’t notice it, how can you fix it? We have to change this complacency.
In order for the 5S process to be effective, everyone in the organization has to be informed of the process, provide support for it, and be committed to sticking with it. Therefore, the 5Ss need to be made a part of an organization’s culture. If only a few people do 5Ss, then it will not work. On the same hand, if everyone does only two or three, even four of the 5Ss, the process will fail. Everyone has to be committed to all aspects of the 5S process from the first to the last pillar. ■
About The Author: Preston Ingalls is president and CEO of TBR Strategies, LLC, a Raleigh, North Carolina-based maintenance and reliability firm specializing in the construction and oil and gas industries. Preston can be reached at pingalls@tbr-strategies.com, or visit www.tbr-strategies.com.
_________________________________________________________________________
Modern Contractor Solutions, May 2015
Did you enjoy this article?
Subscribe to the FREE Digital Edition of Modern Contractor Solutions magazine.
Utilizing the 5Ss: Part 1
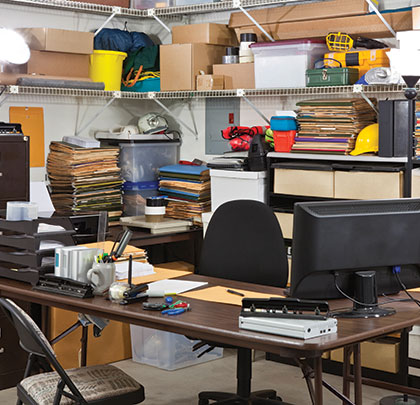