Unique project for world-renowned artist in Texas required extreme teamwork
Architects, engineers, and construction officials found a Texas project one of the most puzzling and challenging of their entire careers. That’s because the building was designed by a world-renowned artist. First and foremost, the structure had to meet the vision of the artist, Ellsworth Kelly. His requirements, artistically speaking, did not perfectly align with workers who were tasked with creating the structure.
The building, named Austin, stands on the grounds of the Blanton Museum of Art at the University of Texas. Overland Partners designed the 2,715-square-foot structure—which carried a price tag of $23 million—that some journalists have described as a “chapel.” Overland Project Manager James Lancaster says the building is a “temple for light,” which is how it was characterized in a story in The New York Times. “The most interesting thing in the building is the way the light moves across the space,’’ Lancaster says. “People watch the color of light dance around the room.”
Building Austin, however, required extensive collaboration from all of the parties in the design and building process. Ellsworth had a clear vision of what he wanted in the building. It was up to workers to execute it. “It starts with intimately understanding the artist,’’ Lancaster says. “We had to understand who he was and what his artwork was about. It was a process that began with listening. Before we put pencil to paper, we had to become attuned to Ellsworth and his vision for Austin.”
WORKING AS A TEAM
Besides meeting the artistic vision, design and construction teams also needed to incorporate the latest demands for mechanical systems, information technology, and security. Furthermore, the University of Texas has a laundry list of institutional standards that construction teams had to meet. In the construction of Austin, every cook in the kitchen had input.
“While every aesthetic decision was his, we did not simply abdicate to whatever Ellsworth asked for,’’ says Rick Archer, the principal in charge for Overland, and an alumnus of the University of Texas. “Codes, material selection, constructability, structure, and HVAC resulted in modifications to Ellsworth’s original design in terms of the scale and proportion.”
Perhaps no issue proved to be more vexing than installing and concealing large and cumbersome heating and air conditioning units. The teams designed a solution to place them in a 1,800-square-foot basement. In Austin, Kelly wanted visitors to see the light and art on the main floor. Rooftop mechanicals were unacceptable to the artist, as was installation on the main floor. Even the wiring had to be hidden or disguised. All of the mechanical and information technology equipment was placed in the basement, out of sight of visitors and maintaining the artistic integrity sought by Kelly.
ACCESSING THE UNDERGROUND
Overland achieved access to underground equipment by installing a double-leaf access door outside the structure. The door, manufactured by The BILCO Company of Connecticut, measures 5-feet by 10-feet, 11-inches, and features a keyed cylinder lock and a special slip resistant cover finish.
The door required 8 weeks to manufacture. T.H. Willis Company procured the door which was installed by Linbeck, the project’s general contractor. Steps and handrails were added to the door to access the basement and meet university standards.
“Many people don’t even know there is access to the basement,’’ Lancaster says. “We had to have access to the basement, but we also had to make the door, as much as we could, invisible. The solution was the BILCO floor access door. The anti-slip coating was critical because where it’s located is only one of two exits in case of emergency. We selected BILCO because of their willingness to work with us to get exactly what we needed. This is not a building; it’s a piece of art. The door, like a lot of other materials, is used in a way that it was probably never used before.”
ADDITIONAL CHALLENGES
The magnitude of the project and the artistic demands created a range of issues for design and construction teams. Even one of the most fundamental components to any building—the walls—required extensive research and creativity to meet the needs of the building.
Kelly envisioned 8-inch precast concrete walls, but architects quickly realized they were not adequate for the building. That material did not allow for mechanicals, wiring, and insulation. Overland decided to use steel walls instead.
“When we added in all these layers, the walls were more than 2 feet in thickness,’’ Lancaster says, which would have adversely impacted the amount of light that would have penetrated the stained glass windows. Architectural and engineering teams finally settled on 16-inch walls. “We determined that was the optimal thickness,’’ Lancaster says. “We were trying to shave off an eighth of an inch here and there. We found the optimal size for every piece in the assembly.”
One other considerable and unique challenge was Ellsworth’s faltering health. Kelly started designing the project in 1986, but could not find a location for the project, the right architectural team, and financial backers. When Overland began working with Kelly in 2012, he was 87 years old and soon after was diagnosed with cancer. “There was a lot of pressure on everybody to move quickly, but also to move carefully,’’ Archer says.
Construction teams spent 6 months documenting and obtaining approval on every aesthetic decision with Kelly. About one month after completing a binder that captured all of the aesthetic nuances desired by Kelly, the artist died at age 92. The building opened in February 2018, a little more than 2 years after his death. The artist did not see the completed project.
A JOYFUL SPACE
The building contains three facades of mouth-blown stained glass panels that tint light as it enters, 14 stations of Kelly’s black and white marble wall works, and an 18-foot tall redwood totem. The colorful glass by Bendheim, mouth-blown by skilled glass masters Glaschutte Lamberts of Germany and fabricated by Franz Mayer of Munich, adds a playful quality to the space.
Lancaster says visitors to Austin, quite simply, will feel joy. That is, after all, what Kelly and every other artist wants when people see their work.
About the author:
Thomas Renner writes frequently on building, construction, and manufacturing for U.S. trade publications. He can be reached at trenner@catalystmc.com.
Modern Contractor Solutions, February 2019
Did you enjoy this article?
Subscribe to the FREE Digital Edition of Modern Contractor Solutions magazine.
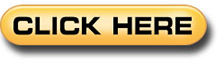