Concrete bridges need to be durable, efficient, and strong—not only to ensure driver safety but also to provide departments of transportation a lower lifecycle cost. These qualities also contribute to a more sustainable design by mitigating emissions, embodied energy, and materials needed to build and maintain bridges.
Concrete made from lightweight aggregates, like expanded shale, clay or slate, can reduce the mass of a structure without compromising its strength, providing increased resistance to permeability and cracking and diminishing shipping requirements. Using lightweight concrete can help contractors streamline transportation and construction processes that result in more durable, resilient and, therefore, more sustainable bridges.
OPTIMIZING EFFICIENCY
In general, structural efficiency refers to the ratio of a structure’s mass with the load it can support. Projects with high structural efficiency indicate a strong yet relatively lightweight design. Whereas normalweight concrete has an average density of 145 pounds per cubic foot (pcf), structural lightweight concrete can have a density as low as 95 pcf. As a less dense material that offers comparable strength, structural lightweight concrete can contribute to higher structural efficiency, which allows engineers to design structures with an equivalent strength but with a reduced mass. This will reduce the loads placed on falsework and formwork and also the effort in handling the concrete.
Optimizing structural efficiency can contribute to bridges that are more resilient to seismic activity. Although lightweight concrete tends to be more brittle than normalweight concrete, its lower mass reduces seismic demands on foundations and substructures, making a lightweight concrete bridge able to withstand seismic events more readily than one built using conventional concrete. With the increased resilience, these structures can reduce the need to repair elements after natural disasters, which shrinks the embodied energy of a project and the materials it needs over its service life. The reduced structure weight also significantly reduces the size and cost of foundations, a major factor in seismic design.
Contractors who use structural lightweight concrete can create resilient bridges in a cost- and time-efficient way by reducing the need for complicated support structures. This can potentially increase their business while also contributing to more sustainable building practices.
REDUCING REQUIREMENTS
Because structural lightweight concrete is less dense, prestressed girders and other precast elements can be made larger while still fitting within truck load limits. This can help reduce the number of shipments required to complete a project, saving fuel and diminishing embodied emissions that would otherwise be necessary for transit.
In “A Holistic Approach to Sustainability for the Concrete Community,” the authors, Ries and Holm, cite two projects by Big River Industries to analyze the shipping costs of concrete products. In the first project, the number of truckloads of precast panel was reduced from 431 to 287 and from 87 to 66 in the second, as more panels could be loaded on each truck. Not only does this represent a sizeable reduction in transportation cost and roadway congestion but it also indicates fewer emissions generated via shipping.
IMPROVING DURABILITY
The durability of concrete depends on several factors, but permeability and cracking are arguably the primary causes of concern. Contractors who can reduce the degree to which their projects experience cracking and corrosion can both increase the sustainability of their projects over their service life and increase owner satisfaction with the quality of their work.
Permeability. Permeability is a measure of the ability for concrete to permit liquids or gases to pass through. Permeable concrete can lead to steel reinforcement corrosion, weakening the structural integrity of the concrete. This is especially a concern for bridges over salt water or where deicing chemicals are used, which can damage embedded metals faster due to chloride attack.
Because lightweight aggregate gradually releases water during drying, it cures the concrete internally. This increases the bond strength between the aggregate particles and the cement paste for reduced permeability. As reported in a 2008 paper presented at the Concrete Bridge Conference, the permeability of sand lightweight concrete was measured for 17 different batches for a long highway bridge deck. The average permeability for all batches of the lightweight concrete was 989 coulombs—well below the 2,500-coulomb limit in the specifications.
By being able to mitigate permeability, lightweight concrete reduces the need for repairs and replacement over a bridge’s service life. As such, these bridges can also reduce user delays and associated emissions when maintenance is required. This contributes to more sustainable construction in the long-term as well as an increase in owner satisfaction.
Cracking. Cracking can affect steel reinforcement as well as the concrete itself. Because lightweight concrete has a greater strength at the interface between aggregate particles and cement paste, a reduced modulus of elasticity and coefficient of thermal expansion, as well as lower shrinkage, it is less susceptible to cracking than conventional concrete. Likewise, because the pores in the aggregate are unconnected and do not allow deep penetration of water, lightweight concrete resists freeze-thaw damage when properly proportioned, batched and placed. This further increases its resistance to cracking and is vital for cold climate bridges, since deicers contribute to rapid freeze-thaw cycles and chloride attack.
CLOSING THOUGHT
When it comes to concrete bridges, it is crucial that efforts are made to be efficient with material use. Lightweight concrete can efficiently extend the service life of bridges and increase their resilience to contribute to lower lifecycle costs for bridge owners, reduced costs for contractors, and a decreased impact on the environment—a win-win situation for all.
About the Author:
Reid W. Castrodale, Ph.D., P.E., is the president of Castrodale Engineering Consultants, and serves as the director of engineering for the Expanded Shale, Clay and Slate Institute (ESCSI). In addition to his many years of industry experience (including serving as chair for the Bridge Committee at the Precast/Prestressed Concrete Institute), Castrodale has also taught numerous seminars and courses on reinforced and prestressed concrete bridge design.
Modern Contractor Solutions, November 2022
Did you enjoy this article?
Subscribe to the FREE Digital Edition of Modern Contractor Solutions magazine.
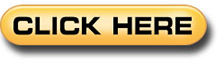