Welding fleet benefits from new technologies
Coastal Steel, Inc. specializes in commercial steel structures up to four stories, ranging from big box retailers to churches and municipal buildings. One recent project included a new addition to a Catholic school in a residential area in suburban Seattle. The two-story building featured approximately 25,000 square feet of floor space, 200,000 pounds of structural steel, and 30,000 pounds of decking.
Coastal Steel’s welding fleet includes the new Trailblazer 325 EFI with Excel™ Power, a machine that offers 325 amps of welding power at 100-percent duty cycle, 12,000 watts of generator power, and an additional 2,400 watts of optional Excel power. Welding requirements in this application vary based on the process and type of joint being welded. Welding with the Flux-Cored process typically requires between 225 and 280 amps when welding with a .072-inch-diameter flux-cored wire. For Stick welding, the machine typically resides between 135 and 170 amps for 5/32-inch electrodes and 110 to 130 amps if using a 1/8-inch electrode.
To apply the high-strength tension shear bolts, Coastal uses a “Lejuene Gun,” an electric shear wrench, off of the machine’s generator power. This tool requires 1,400 watts of power—easily handled by the primary generator power or the optional Excel power. Most other typical jobsite tools (lights, grinders, drills, screw guns, rotor hammers) require less power.
PROPER PERFORMANCE
As power tools are often run at the same time as the welding arc, it is important that there is no deterioration or interruption of the arc itself. Some traditional engine-driven welder/generators experience a fluctuation in the arc when a load is applied to the generator. This fluctuation can lead to defects in the weld.
“When you’re doing a full penetration weld, when your volts are high and your amperage is high, if you draw down a small bit, it can cause pinholes, it can cause cold roll,” says Hummel. “There’s only a fine line with Flux Cored when you’re running those full penetration welds. You’re as hot as you want to be and you don’t want it to change.”
The new machine features Smart-Cor™ technology that allows for the weld and generator power to remain entirely separate.
NEW LEVELS OF EFFICIENCY
Auto-Speed™ technology is a new feature for engine-driven welder generators that automatically adjusts the engine to run at lower speeds depending on the total power needed. Traditional engine-driven welder generators will run at a full 3,600 rpm for all applications. With this new technology, engine speed briefly jumps up to 3,600 rpm and then automatically lowers to match the task at hand. Certain loads, such as running 1/8-inch electrodes at relatively low amperage rates, allow for the machine to carry the function out at idle (2,400 rpm).
“If you’re running an 1/8-inch 7018 electrode, it will only idle up small amounts at a time,” says Hummel. “It’ll just give you enough rpm to run at 125 amps. If you’re running flux-cored wire, it will idle up more to run 20 volts. It will do what it has to do without doing too much.”
The second technology, Excel Power, is similar in that it allows jobsite tools to run at 2,400 rpm. In traditional welder/generators, the machine immediately ramps up to 3,600 rpm when a generator load is applied. With Excel Power, the machine runs most common worksite tools at idle speed.
Another key factor contributing to fuel savings is electronic fuel injection. Electronic fuel injection optimizes air/fuel ratios for all engine speeds and loads, ensuring operation at peak fuel efficiency. It also helps eliminate the starting problems encountered with carbureted models in colder and Northern climates. As fuel prices continue to rise, every bit of fuel savings helps. With this and the other technologies found in this machine, contractors will notice up to a 35-percent drop in actual fuel use, and runtimes on a standard 12-gallon tank extended by as much as 50 percent.
“I can run this machine about 20 hours on one tank of gas,” says Hummel. “I believe it’s about 30 to 40 percent better on gas than other machines. You might get 12 hours out of (other machines), but they either run on low idle or high idle—it’s all the way or nothing.”
IMPROVES WORK ENVIRONMENT
The ability to operate at lower sound levels is beneficial to both the neighbors and workers on the site. Steel work begins at 7 a.m., and school starts at 7:30 a.m. Due to the ability to run most processes at lower rpm, and an improved packaging design that helps the engine run cooler and produce less noise, the new welder/generator produces up to 68-percent less sound compared to previous models.
“The noise reduction is good anywhere, even for my sake,” says Hummel, “because I’m tired of hearing (welder/generators) run wide open all day long. When it’s on low idle, you can talk around it and you can hear yourself. It’s definitely a quieter machine than any other machine, the fuel savings is good, and having the separate generator and welding power is a big deal.” ■
About The Author:
Christopher Wierschke is a product manager with Miller Electric Mfg. Co. For more information, visit www.millerwelds.com.
_________________________________________________________________________
Modern Contractor Solutions, April 2013
Did you enjoy this article?
Subscribe to the FREE Digital Edition of Modern Contractor Solutions magazine.
Two Stories Up
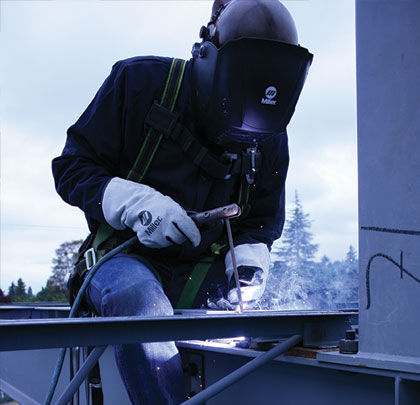