Tunnels form vital traffic and railroad arteries across the United States, providing the backbone for people and goods to traverse challenging terrain. There are 541 highway tunnels in the nation, accounting for more than 381 lane-miles of Interstate, State, and local routes. The majority of these tunnels are between 60 to 110 years old, and combined they carry in excess of 15.4 million vehicles on the average day.
As these important tunnels age, asset owners must find creative, efficient solutions for repair and maintenance. Unlike the horizontal surface of a bridge, a tunnel typically has a 360 degree surface of concrete that must be regularly monitored and restored if the structure is to last. The only alternative—tear down and rebuild—would be extremely expensive and environmentally damaging, if not impossible in many cases.
In Portland, Oregon, the Portland Board of Transportation (PBOT) is putting the finishing touches on a project to restore the concrete ceiling and vertical walls of the Northwest Cornell Road Tunnel. With the repaired surface covering a total area of approximately 28,800 square feet, this project illustrates how innovative equipment can be combined with adaptive project execution to maintain the world’s tunnel assets.
TUNNEL DETERIORATION
The NW Cornell Road Tunnel consists of two tunnels that were constructed between 1939 and 1941 to support residential development in Northwest Portland. Tunnel 1 is 500 feet long and Tunnel 2 is 250 feet long, with both tunnels containing two lanes. Approximately 10,000 vehicles per day use the Cornell Tunnel.
During a routine inspection by the PBOT, a large crack near the crown of Tunnel 1 was observed. In 2019, an in-depth field assessment and subsequent geotechnical engineering report recommended concrete strengthening and relining for both Tunnels to prevent structural failure and minimize the future permeability of harmful contaminants. The existing concrete was estimated to have an average strength of 5,500 psi but varied widely depending on the area.
The project was awarded to general contractor MJ Hughes Construction. With offices in Washington and California, MJ Hughes is an experienced heavy civil contractor that has a strong track record of success in structures, earthwork, and utilities. It is known for embracing complex projects and strict schedules, and is always ready to adapt to evolving project demands. Pat McSorley, who has been a superintendent with MJ Hughes for more than 5 years, was the project superintendent responsible for overseeing all aspects of the Cornell Tunnel rehabilitation.
MJ Hughes subcontracted the task of removing deteriorated concrete to CCS Industrial Services. Based in Longview, Washington, CCS is an experienced contractor that provides a number of solutions including hydro excavation, environmental remediation hydrodemolition, industrial cleaning, street sweeping, and waste disposal. Since 2015, CCS has been using Conjet ACR robots to perform hydrodemolition work.
The concrete removal phase was awarded to CCS based on its impressive track record and fast projected timeline. CCS was confident that, using the Conjet Robot 557 MPA, it could outperform other contractors that would attempt to complete the concrete demolition with jackhammers and breakers.
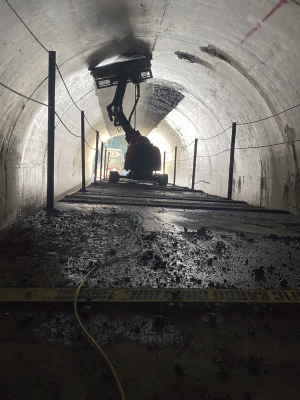
CONJET HYDRODEMOLITION
Hydrodemolition is a process that uses high-pressure water to remove concrete or other surface materials. The technology has many advantages: It is more efficient and productive than using jackhammers or other concrete breaker tools—one Conjet robot can remove the same amount of concrete as 25 or more jackhammers. Hydrodemolition is also safer than competing technologies—operators are not exposed to silica dust or vibrations that are present with jackhammers and roto millers, and they can stand a safe distance away from the robot as it operates. Finally, hydrodemolition is the most sustainable method for structural preservation—because hydrodemolition does not create microcracks in the remaining concrete, pull-off tests show that a hydrodemolition-prepared surface forms a 2.5x stronger bond with the new concrete overlay compared to the same surface that has been prepared with a jackhammer. This extends the structure’s useful life and reduces concrete consumption. In addition, hydrodemolition preserves and cleans the rebar reinforcement whereas jackhammering and roto milling damage the rebar and require significant replacement.
Further improving sustainability on the Cornell Tunnel project, CCS and MJ Hughes recycled the concrete slurry wastewater produced by hydrodemolition operations and reused it for additional blasting. This reduced total water usage and disposal costs.
CCS’s fleet of hydrodemolition robots was supplied by Conjet AB. Conjet manufactures hydrodemolition robots in Handen, Sweden, with a domestic subsidiary in Charlotte, North Carolina, which provides local sales and support to the North American market. The founders of Conjet were inventors of the hydrodemolition process in the mid-1980’s, and in the 35 years since the company has been focused on developing the technology to maximize ease of use, productivity, and safety. Conjet’s 35+ years of innovation, collectively referred to as Automated Concrete Removal (ACRTM) technology, are incorporated into every robot manufactured.
MULTIPURPOSE ARM
For the Cornell Tunnel, an important feature of the Conjet 557 robot was its Multipurpose Arm, or MPA. The MPA allowed CCS, with the push of a button, to quickly relocate the 557’s cutting head to remove concrete from different angles and reaches on the overhead crown and vertical sidewalls.
Regarding the Conjet 557, the CCS onsite supervisor reports, “The flexibility of the 557 MPA was crucial for this project. We needed the ability to quickly adapt our cuts to different depths, angles, and reaches in order to meet the engineering requirements. The 557 MPA allowed us to accomplish this work with relative ease and, importantly, quickly. We also received valuable technical advice from Conjet’s customer success manager, Tim Best, on how to leverage the flexibility of the ConjetONE control system to set the 557’s cutting parameters to fit the curved tunnel radius. As a result, we were able to perform this complex job without purchasing and installing any additional attachments on our 557.”
McSorley comments, “The Conjet 557 MPA performed great for us. I was impressed with CCS’s ability to easily adjust the robot’s parameters to the compensate for the radius of the tunnel. And due to the unexpected complexity of the concrete removal that was needed, the 557’s versatility was crucial to our success on this project.”
CONSTRUCTION BEGINS
The sitework began in September 2021. Tunnel 1’s project specifications called for a 14 ft wide x 2 in deep strip to be removed at its crown for the entire length of 500 feet. The removed concrete would be replaced with Shotcrete to seal and preserve the Tunnel’s rebar reinforcement beneath the surface.
Tunnel 2 had experienced more severe deterioration than Tunnel 1 over the years. As a result, the project engineers initially planned to use hydrodemolition to cut 12 inch wide x 12 inch deep ribs every 7 feet for increased structural stability. In addition, the plan called for the top 2 inches of the entire overhead area and vertical walls, totaling 14,000 square feet to be removed and replaced with new concrete. Finally, in Tunnel 2 a new mat of #3 rebar would be added to the entire removed surface area, covered with mesh, and filled with Shotcrete. The #3 rebar mat would create a new reinforcement system to replace the original rebar which was damaged by the concrete deterioration and resulting permeability.
CCS quickly mobilized its equipment and began removing the concrete. Tunnel 1 demolition operations went quickly and according to plan. However, as CCS began removing concrete on Tunnel 2, some unexpected challenges arose.
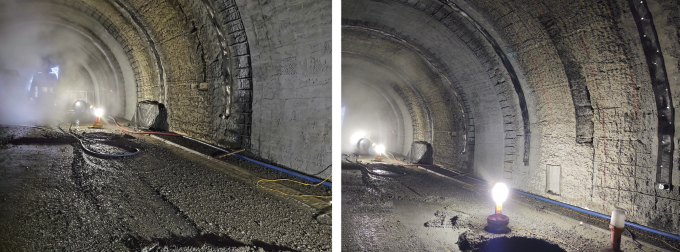
PROJECT WITH CHALLENGES
When CCS began operating the Conjet 557 in Tunnel 2, it was discovered that not only was the concrete extremely deteriorated, the thickness was also very inconsistent, ranging anywhere from 8 to 24 inches depending on the location. As a result, the original plan to cut 12 inches deep and place new concrete to form structural ribs had to be abandoned.
Rather than installing ribs, the PBOT engineering team decided to pivot to a new structural strengthening approach that involved cutting thicker, 6 in deep x 10 ft long panel sections. Each panel section would have a reinforcing mat of high-strength #6 rebar. To maintain structural integrity during this process, each panel section would need to be cut to the proper depth, replaced with rebar and concrete, and cured before work could begin on the next section.
CCS got to work executing the new project specifications for concrete removal. Using the ConjetONE control system, CCS was able to easily adjust the parameters of the 557 MPA to cut at different speeds across the cutting head, ensuring a 6 inch deep removal, even across the curved crown of the Tunnel. The MJ Hughes team then came back in and installed new rebar and mesh, filling in the new reinforcement system with Shotcrete.
The revised construction plan was executed successfully, and the concrete repairs were completed in April 2022. McSorley states, “In view of the unexpected challenges, we are extremely pleased with the outcome of the Cornell Tunnel restoration project. CCS exceeded our expectations with respect to the concrete removal work. The hydrodemolition process provides an incredibly efficient, high-quality removal that is perfect for applying a new concrete overlay which will extend the useful lives of these tunnels for many years to come. Hydrodemolition was the only way to go for this work. It was far superior to any other methods we could have used for the concrete removal.”
CLOSING THOUGHT
The Cornell Tunnel restoration project is a great example of how skilled contractors and engineers can deploy cutting-edge hydrodemolition equipment to preserve vital concrete infrastructure, regardless of the unexpected challenges that may arise in the process.
For More Information:
For more about Conjet hydrodemolition, visit www.conjet.com.
Modern Contractor Solutions, July 2022
Did you enjoy this article?
Subscribe to the FREE Digital Edition of Modern Contractor Solutions magazine.
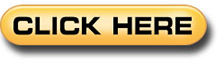