Benefits of idle reduction technology
Fuel and maintenance costs related to idling is a major concern for work truck fleets. Nationally, trucks burn four billion gallons of fuel each year from idling. A recent study on idling calculates that a fleet of 100 trucks idling for 2 hours a day can cost up to $165,000 a year in wasted fuel. Selecting idle reduction technology that doesn’t compromise driver comfort is critical for fleets to save money, reduce their carbon footprint, and keep their drivers safe. Although many fleets use tracking software to optimize routes and limit unnecessary side trips, idling is still an issue. Staged attenuator trucks for example often rely on idling to keep safety lights powered.
ISSUES WITH IDLING
Statistics show that 57 percent of government and municipal work trucks, such as snow plows and refuse trucks, idle between 1 and 4 hours daily. According to Argonne National Laboratory-Center for Transportation Research, garbage trucks alone waste close to 27.5 million gallons of fuel per year through idling.
Fuel consumption isn’t the only factor impacting the bottom line. Idling increases engine wear, maintenance costs, and downtime. Idling for one hour every day for one year is equivalent to 64,000 miles of engine wear. That results in excess annual maintenance costs of as much as $9,472 per truck.
One factor affecting maintenance costs is repair and replacement of diesel particulate filters (DPF). Tier 4-compliant engines are not designed to idle for extended periods of time. Idling causes buildup of particulates in the filters, which requires frequent cleaning. Particulates not burned off through the regeneration process can lead to poor fuel economy, reduced power output, and costly engine damage. Replacement is expensive. Each DPF system can cost up to $15,000.
The environmental impact of idling cannot be overlooked. According to 2016 data from the EPA, the transportation sector accounted for the largest portion (28%) of total greenhouse gas emissions in the United States, followed by electricity and industry. Among the transportation sector, light- and medium-duty work trucks were the largest and second largest source of emissions.
With the focus on government directives and corporate and consumer demands to reduce emissions, all companies should focus efforts on eliminating wasteful idling. Fortunately, a simple change can make a big difference and costs can be reduced at the same time.
THE SOLUTION
Inspiring idling reduction technologies are available for work truck fleets interested in saving money, reducing emissions, and complying with changing regulations without compromising driver comfort.
THE TECHNOLOGY
Designed specifically for work trucks, Idle Free® Flex Systems are “key off” idle reduction technologies trusted by DOTs and municipal fleet managers throughout North America. Maintenance and fleet managers appreciate the cost savings of reduced maintenance and fuel. Drivers appreciate the 6 to 8 hours of interior cab and engine heat the system provides. They can also run safety, interior and exterior lights, and communication equipment when the vehicle is off.
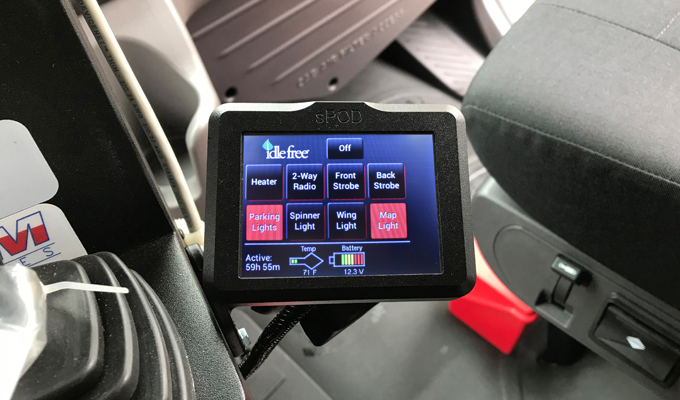
THE BENEFITS
A CARB-compliant technology, Idle Free Flex Systems comply with most city, municipal, and state idling laws. All system functions are accessed via a small touch screen user interface located near the driver. Circuits controlled by the system are protected with a low-voltage disconnect to prevent no starts and protect batteries from over-discharge. A timer on the touch screen displays cumulative runtime for the system making return-on-investment calculations easy for fleet managers.
An automatic Start-Stop Systems can be added to Flex Systems or used as a stand-alone solution to monitor truck battery state of charge and automatically start the truck at a predefined voltage. The system allows unaccompanied attenuator trucks to limit idling while powering lights and signage unaccompanied.
In addition to fuel savings, major savings on DPF maintenance and replacement, and decreased wear on the engine, Idle Free Flex Systems lower noise, minimize downtime, and extend the life of the engine and truck. Flex Systems also help fleets meet regulatory and environmental goals. The cabin engine heating technology is SmartWay Verified. Reducing idle times by just one hour per week per truck can prevent the production of more than 500 pounds of carbon dioxide (CO2) per year.
CLOSING THOUGHT
Work trucks are designed to get jobs done. Where heating, cooling, liftgate operations, etc. have traditionally been operated through idling, times have changed. The “key off” idle reduction technology provides up to 8 hours of interior cabin heat, engine warming for cold starts, power for communication devices and interior, exterior, and safety lights. Using a Flex System allows fuel savings by the reduction in truck idling, reduced repair and replacement of the diesel particulate filter, increased engine life and decreased maintenance, and helps reduce a truck’s carbon footprint with lower CO2 emissions. A win-win for the driver, your equipment and investment, and the environment.
About the author
Greg Bremhorst is the director of sales–heavy duty and power systems for Phillips & Temro Industries (PTI) with 20 years of experience in the industry.
Modern Contractor Solutions, November 2019
Did you enjoy this article?
Subscribe to the FREE Digital Edition of Modern Contractor Solutions magazine.
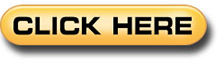