The construction industry is constantly evolving with new equipment innovations and technologies to help your machines and operations run optimally. There is a tool for every job, but as long as humans have been building, few things rarely change: 1) having the right tool for the job, and 2) operation and maintenance matters.
Most major OEM’s note that undercarriage represents an average of 50 percent of your machine’s owning and operating costs. Routine maintenance and inspection of the undercarriage are critically important to optimizing the life of these components. Further extending the undercarriage life can be done with the use of quality rubber or polyurethane track pads. Identifying the culprits of undercarriage wear is first and foremost the best way to understand how track pads lend a hand in protecting your equipment’s undercarriage.
What causes undercarriage wear and premature failure?
Friction, abrasion, and uneven wear/loading are an undercarriage’s worse nightmare. Any one or combination of these can result in undercarriage wear, damage, and failure if not properly handled through regular preventive maintenance programs, combined with correct equipment operation as recommended by the manufacturer.
Several factors lead to an increase in undercarriage wear: track tension, operation of components past their wear limits, premature parts failures, and operation on hard surfaces. The consequences of increased track wear and lack of preventive maintenance and/or inspection can be severe. An increase in maintenance costs is the most critical aspect affecting a contractor’s bottom line, but downtime can be far more costly. Increased wear leads to more frequent replacements, removing the machine from service, and additional labor costs.
What can you do to reduce undercarriage wear?
Through proper preventive and operational maintenance, best practices, and following the manufacturer’s recommendations, you can improve equipment efficiency, reduce wear, and extend the life of the undercarriage. Simple steps like tracking machine hours, monitoring part replacement cycles, daily inspection, and cleaning are just a few ways to improve undercarriage wear. In addition, rubber and polyurethane track pads can help reduce wear on your undercarriage.
What are Track Pads?
Track pads are designed to protect surfaces from damage caused by steel tracks. Typically made from rubber or polyurethane, they can be attached to either the steel grouser shoe or bolt directly to the chain and are often used in place of plywood, sand, or mats. Track pads allow the machine to be operated as intended on any surface without the need for additional personnel or movement of a substitute material.
Rubber track pads are intended for operation on smooth, flat surfaces. Generally, rubber track pads provide better traction but are susceptible to damage by hard debris. Newer to the industry, polyurethane track pads have a higher cut/tear/abrasion resistance and offer 3-4 times longer wear-life. Intended for a wider range of applications than rubber and are only slightly more expensive, making them a far superior option.
Ron Johnson, owner of Riverbend Equipment, did a test comparing rubber track pads against polyurethane track pads on two machines working on the same job. Johnson states, “We’ve always used rubber track pads for all of our mid-large size excavators, but we wanted to optimize our maintenance routine. We tried the polyurethane CUSHOTRAC® ReDDi™ pad side by side with the OEM rubber, the results were staggering. The polyurethane pads had minimal wear after 1800+ hours and the rubber pads were peeling off the steel core.”
In Riverbend’s typical operations, switching to a polyurethane track pad reduced their maintenance costs significantly and eliminated unexpected downtime in the field. “I’ve changed my entire fleet over to the polyurethane ReDDi track pads—they’re guaranteed to last and that’s one less thing I have to worry about,” says Johnson.
How do track pads help reduce undercarriage wear?
The primary purpose of rubber or poly track pads is to provide a less aggressive and softer contact with harder concrete or asphalt surfaces. This “cushion” effect of track pads naturally absorbs the impact of the machine’s operation and vibration, reducing undercarriage friction and minimizing track slippage. Another bonus is significant noise reduction—like comparing nails on a chalkboard to an eraser. Operator comfort improves and noise complaints drop with the use of rubber or poly track pads.
TRACK PAD MOUNTING STYLES
Clamp/Clip-On: Pads that clamp or clip over the existing steel grouser shoes. No modification to the equipment is required and installation is the fastest of any style of track pad—typically in 2-4 hours for a full set. Intended for temporary use and should be removed when not needed.
Bolt-to-Shoe: Pads that bolt directly through steel grouser shoes. In some cases, steel grousers require drilling for bolt placement. Commonly found in road milling machines.
Bolt-to-Link/Chain: Pads that are fitted with steel inserts/cores and bolted directly to the chain links, eliminates the need for steel grouser shoes. No modification to equipment is required. Optimal choice for excavators, but can be used on other steel tracked machines. CUSHOTRAC ReDDi track pads are Bolt to Link/Chain style pads.
Mold-On: Pads that are molded to a steel grouser shoe and bolt directly to the chain.
CLOSING THOUGHT
As you approach your next tear down/maintenance season, or have a project that requires surface protection, invest in the operation and maintenance of the machine—be sure you are not stepping over a dollar to save a dime.
For more information:
For more about track pads by Superior Tire & Rubber Corp., visit www.superiortire.com.
Modern Contractor Solutions, June 2020
Did you enjoy this article?
Subscribe to the FREE Digital Edition of Modern Contractor Solutions magazine.
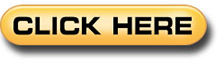