For the fleet manager of a large collection of varied equipment, each with different tire needs, managing a replacement schedule for tires can be a challenge. With a well-informed and well-defined tire maintenance and replacement strategy in place, however, a fleet manager will undoubtedly be able to save time and money while decreasing downtime and increasing productivity. Here are five tips for reducing costs through an effective tire management plan:
1. IDENTIFY THE ROOT CAUSES OF TIRE PROBLEMS
Start by conducting a tire scrap pile analysis and look for common signs of premature failure. Your local tire dealer can help with this. Common problems include uneven wear, damage to sidewalls, separations in the tire, and damage to the beads or lining. Separations in the tire and uneven wear toward the shoulder often point to issues with overloading, underinflating, or running the tire beyond its recommended ton-mile-per-hour (TMPH) rating. On the other hand, over-inflation may be the culprit behind impact damage and uneven wear toward the center of the tire. Frequent tearing or chipping of the treads may indicate that the fleet manager should select a different tread compound on their tires. Establishing this baseline of performance will help the tire professional make recommendations on better maintenance and operations practices, as well as better informed tire selection moving forward.
2. SELECT THE RIGHT TIRE FOR THE JOB
Tire manufacturers offer a range of application-specific compounds and tread designs; selecting the right tire for the job is critical to maintaining a low cost-per-hour. Cut-resistant compounds are a good choice for harsh settings with sharp, uneven terrain; wear-resistant compounds work well for machines that frequently stop and start on hard surfaces; and heat-resistant compounds are recommended for long hauls at higher speeds. Tread depth is also a key factor in tire life and a fleet manager may consider a deeper L-4 or L-5 tread if an E-3/L-3 isn’t cutting it. Not only can tire choice help reduce costs, but the choice can drastically improve productivity. It’s important to look at how tire choice impacts bottom line—not just replacement costs. New technologies such as Low Sidewall (LSW) can improve breakout force and machine stability—both of which equate to increased production and improvements to the bottom line.
3. ADHERE TO A WELL-DEFINED MAINTENANCE REGIMEN
Maintaining the proper inflation pressures is the best way to prolong tire life. It’s best to check inflation each time the machine is being refueled, at minimum. It’s also important that the fleet manager inflate to the recommended levels for each individual machine—not simply the psi noted on the sidewall of the tire, which indicates the maximum allowable pressure. Rotation schedules should be determined by individual machine. For a three-axle haul truck, about 55 to 65 percent of gross vehicle weight is carried by the front tires when empty, so it’s important to rotate the fronts to the rear at about one-third of the tires’ expected life span. When loaded, however, approximately one-third of the weight is distributed to each axle, so it’s also important to look at how operational and site conditions affect tire wear in order to make a rotation recommendation. On a loader, you have to keep in mind that the front tires usually bear 65 percent of the load with a bucket attached. So, it’s really important to rotate front to rear in order to give the front tires a rest for the remaining 50 percent of their projected life.
4. UTILIZE MONITORING TECHNOLOGY
Many OEMs offer monitoring technologies in their equipment, which can provide data to help fleet managers calculate important tire metrics, such as TMPH. However, fleet managers looking to reduce costs and extend tire life should consider also integrating tire-specific monitoring systems on their equipment which can provide metrics such as road gradient, weight distribution, road camber, turn radius, inflation pressures, internal running temperatures, and GPS. All of these metrics will help the fleet manager better pinpoint operational issues or site conditions that pose risks to tires.
5. TRAIN YOUR OPERATORS
After the operational assessment, the tire dealer may conclude that the fleet’s TMPH exceeds the limitations of the tire. When this happens, the tire dealer will often recommend traveling at lower speeds, running fewer cycles, or carrying smaller loads. Such a suggestion is often hard to swallow for fleet managers, however. In the end, the tire dealer can consult with the fleet manager to decide which provides a greater cost savings—increased tire life or increased production. Whatever is decided, make sure the operators are practicing what is preached. ■
About The Author: Johni Francis is a global product manager with Titan Tire Corporation. For more information, visit www.titan-intl.com.
_________________________________________________________________________
Modern Contractor Solutions, July 2015
Did you enjoy this article?
Subscribe to the FREE Digital Edition of Modern Contractor Solutions magazine.
Top 5 Tips For Reducing Costs Through an Effective Tire Management Plan
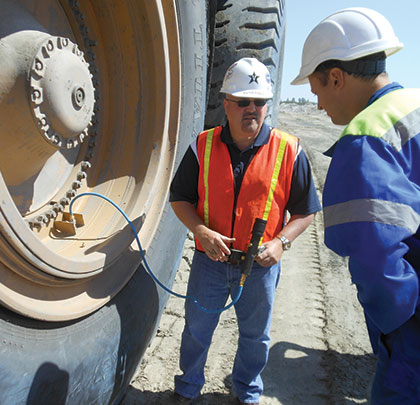