By Tom Webb
A typical construction jobsite contains a plethora of small equipment and power tools, along with heavy equipment, such as cranes and bulldozers, that need to be tracked. Assets can easily get lost or walked off the site if they are not adequately followed. Trucks and other fleet equipment need to be tracked as well so that supervisors and managers know where this equipment is at all times.
Many contractors still use paper systems to track tools manually. They write down the piece of equipment in a tool log, enter the person’s name and location, and the time the equipment is checked out. When the worker finishes with the equipment, he/she checks it back into management. But papers can get lost. Plus, if you enter information into a paper log, your admin person must re-enter the information into a computer system for billing purposes. Reentry of data often leads to mistakes and errors.
AUTOMATING PROCESSES
Automating the tool tracking process provides you and your team the ability to:
- Quickly assign tools and equipment to individual workers. Your team can see which tools and equipment are in use, available, or out of service. Check tools and equipment in and out electronically, so a record exists of who uses what piece of equipment. You will never have to call around looking for a bit of equipment again.
- Monitor tool usage and determine how well the worker used the equipment or if they need additional training. By assigning equipment electronically, workers know they are accountable for the equipment. If it becomes damaged or lost, management will know who used the equipment last and follow up with the worker.
- Sends you alerts when maintenance needs to be performed, when warranties and registrations expire, when inspections are due, and if parts inventory goes below desired stock levels. Track usage and machine hours to schedule maintenance based on handling.
- Manage work orders, shop, and equipment costs with complete transparency to all stakeholders involved, including office, field, project managers, and shop.
- Maximize equipment utilization by identifying assets used heavily or pieces not used very much; those that sit idle can be deployed to areas of need.
BENEFITS OF TRACKING
Tracking equipment and tools using paper misses out on one of the key functionalities that automated systems offer: maintenance monitoring and preventive maintenance programs. By monitoring tool check-in/out, length of use, and other vital information, your team will know when the tool or equipment needs to go through its routine maintenance program. Preventive maintenance keeps tools and equipment in top working condition.
Using an iPhone or Android phone with a tool tracking mobile solution helps you keep track of equipment in the field. Many firms have over 75% of their data entered via mobile devices. Mobile apps save workers time if they can input information while doing their work at the jobsite.
MANAGING ASSETS
Getting real-time visibility of assets is critical to managing your equipment assets. Fleets use telematics devices, GPS Systems, and ELD platforms to monitor the location of the truck or equipment. Fleet management systems monitor these devices to track equipment wherever it moves. If a bulldozer is at one end of the jobsite but should be in another location, these tracking devices can alert management to the bulldozer site. Managers can then communicate with the operator to find out what he is doing and why.
Small tools need to be tracked as these tools play a big part at any jobsite. Most sites have more small tools than they have big pieces of equipment. Bar code systems track small tools while eliminating paperwork and providing access to inventory logs locating equipment and status.
Use a solution that sends alerts when maintenance needs to be performed, when warranties and registrations expire, when inspections are due, and parts inventory is below desired stock levels.
Use a system that provides detailed equipment history and automatically builds timecards to manage payroll better. Connect directly with your accounting system to avoid double entry and save time in the payroll process. Data is accessible between products, reducing manual entry and increasing productivity.
Mobile systems allow workers to enter information, such as time, parts information, service readings, and notes while out in the field. That way, workers don’t have to come back to the office to enter data; it can be entered while on the job, saving time and improving productivity. If a worker is out in the field and notices an issue with a piece of equipment, they should submit a maintenance request on the fly.
Who Uses Tool Tracking Solutions?
McGeorge Contracting of Sweet Home, Arkansas, is known for completing large industrial projects offering construction, earthmoving and excavation, site work, and mining. The company needed to improve its maintenance shop. McGeorge implemented HCSS’s Equipment360 to track tools and keep records on all the equipment. All the information on each tool, piece of equipment, maintenance schedules, repair records, and more are available to everyone in the shop. Each piece of equipment can have its maintenance schedule, and the software connects to payroll so workers can be paid for the repairs and maintenance they perform.
CLOSING THOUGHT
With so many costly assets on a jobsite, it is crucial to modernize operations with automated tools that keep track of paperwork, work assignments, maintenance, and tools. Having a 30,000-foot view of your equipment assets with easy-to-spot trends around utilization, life expectancy, and equipment costs mean you will have better control over all your equipment.
About The Author
Tom Webb is the vice president of products for construction software developer HCSS, a Texas-based company that since 1986 has specialized in developing software to help heavy, highway, and utility construction industry companies streamline their business operations. Webb has 29 years of experience in software technology and 25 years in the construction industry. For more, visit www.hcss.com.
Modern Contractor Solutions, June 2021
Did you enjoy this article?
Subscribe to the FREE Digital Edition of Modern Contractor Solutions magazine.
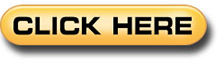