Building a successful contracting business is hard work—there’s no doubt about that. Every day you face challenges that threaten to impact project deadlines, profits, jobsite safety, and even your business reputation. Management of your tool and equipment inventory is one of those far-reaching challenges that can have repercussions affecting all of these issues.
When workers can’t find the tools they need to do their jobs, it’s more than just a minor annoyance—it means lost productivity, lost profits, and even lost customers when project deadlines are missed. Keeping track of your valuable tools and equipment at all times is key to increasing staff productivity and accountability, as well as reducing tool replacement costs. Of course, this task is further complicated when managing construction projects across multiple jobsites.
RFID TECHNOLOGY
Many contractors in construction and other heavy industries have come to rely on radio frequency identification (RFID) technology to gain overall visibility of all their valuable assets worldwide—from tools and equipment, to machinery, consumables, and vehicles. An RFID-enabled tool and equipment management system simplifies the issue and return of tools to contractors and employees using a simple and accurate transaction system and database.
Attaching RFID tags to equipment allows quick and easy scanning of tools for check-in and check-out, even from a self-service kiosk, eliminating the need to staff a tool room. This system not only keeps workers accountable for the tools in their possession, it also tracks the transfer of equipment between various jobsites and storage locations, making sure that the right tool is in the right place at all times for maximum productivity and operational efficiency.
Better management of tools and equipment means fewer tools lost to theft and hoarding, reducing equipment budgets. RFID tracking can be used with all kinds of large equipment and tools that are left outside in the weather, as well as those exposed to rough and dirty conditions on a regular basis, since RFID tags are durable and can be scanned even when covered in grease and grime.
Likewise, ruggedized mobile devices, such as the CN70E RFID mobile computer, are available for scanning equipment in the field under harsh conditions. Choosing this type of reliable, rugged handheld scanner helps lower cost of ownership, versus non-ruggedized scanners that would need to be replaced more often.
FUTURE PROOF
When selecting a tool tracking solution, look for a scalable solution that will grow with your business. The ToolHound tool and equipment management system has been deployed by industry-leading companies of all sizes to track an unlimited number of tools and equipment across multiple jobsites. For example, this solution is used by a global engineering firm to achieve complete visibility of large equipment, supplies, and hand tools at jobsites on four continents.
Beyond scalability, functionality and accessibility are key criteria for an equipment tracking system. The powerful ToolHound system enables on-demand access to your equipment database remotely from any Internet-enabled device, offering 24/7 oversight and visibility.
In addition to tracking the location of tools, a robust RFID-enabled equipment management system like ToolHound enables tracking of equipment repair or calibration schedules. Following proper compliance and maintenance schedules not only protects your equipment investment for maximum ROI, it also ensures safety on the jobsite, a vital concern for any contractor.
Another concern for many contractors is the ability to recapture tool costs through accurate and timely billing per project. The ToolHound system includes an automated billing feature that makes it easy to maintain accurate rate calculations and simplifies management of internal or external tool rentals and work order costs. Moreover, tool purchasing functions can be automated, saving time and money, as well as streamlining the identification of obsolete or excessive inventory that can be resold.
ADDED PEACE OF MIND
Investing in the right RFID-enabled equipment management solution can help your company achieve peak operational efficiency and significant cost savings by minimizing tool loss and hoarding, maximizing equipment use, increasing worker accountability, and improving productivity. As a result, you gain overall peace of mind that the right tools are in the right place to get the job done … and the challenge of protecting your valuable business reputation just got a little bit easier. ■
For More Information: For more information about maintaining productivity and profitability with RFID-enabled tool management, visit www.toolhound.com.
_________________________________________________________________________
Modern Contractor Solutions – July 2016
Did you enjoy this article?
Subscribe to the FREE Digital Edition of Modern Contractor Solutions magazine.
Tool Tracking Solution
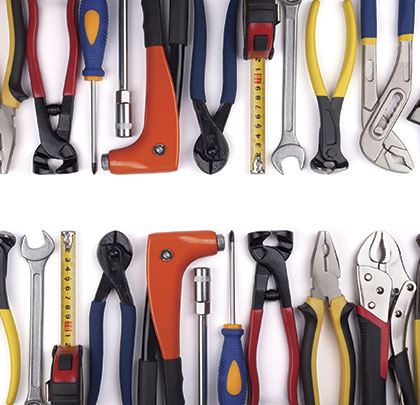