By Victoria K. Sicaras
When building structures in hurricane-prone states, it’s important to factor Mother Nature in design decisions. A popular building design in Florida—and other coastal and high-wind communities—includes a resilient cast-in-place concrete structural frame accompanied by concrete masonry infill at the perimeter that offers protection from high-velocity winds and flying debris. The structure is typically covered with an attractive architectural stucco finish.
Delivering the final product requires a high level of coordination among concrete, masonry, and stucco trades to ensure the design’s structural elements and finishes fit seamlessly together. That’s easier said than done, as each trade’s allowable construction tolerances vary. If the three differing trade tolerances are not addressed and adjusted for compatibility by the design team, they often lead to confusion and discrepancies at the jobsite, which can result in change orders and cost overruns.
To help close the gaps between the structural shell (concrete and concrete masonry unit) tolerances and the stucco industry’s expectations, Ceco Concrete Construction is working with the Florida Lath & Plaster Bureau (FLAPB) and the American Society of Concrete Contractors (ASCC) to provide industry-backed guidance and recommendations. Concrete and stucco contractors can share these documents with clients, designers, and other project partners to resolve tolerance issues before construction begins.
THE TOLERANCE CHALLENGE
Construction tolerances are simply defined as allowable deviations from specification or design values. Each trade’s maximum tolerance limits are dictated by building codes and standards; deciding which tolerance ranges are compatible and reasonable for the project is a design responsibility. Yet, because these allowable design deviations are not reflected in designers’ BIM models, alignment issues do not always arise until the skin phase of construction.
Generally, at this point, the finish contractors are left to determine whether they can fix the tolerance issues or notify the general contractor of deficiencies that must be corrected before they can begin their work.
Ceco’s Florida Team has been able to overcome tolerance issues between concrete and masonry scopes by self-performing masonry work in addition to the structural concrete. The concrete and masonry divisions work together to create higher-quality connections where the two structural components meet. This synergy allows Ceco to provide clients options that include schedule impacts when it comes to substituting cast-in-place concrete for CMUs or vice versa. However, the varied tolerances can still be a problem when stucco contractors arrive on the job.
Work on the project’s concrete frame begins first, followed by masonry and infill after the structural pour is complete. Stucco work is last. As the last installer to arrive onsite, the stucco contractor may come across tolerances from preceding work that require them to apply thicker stucco. The stucco contractor must determine if this work goes beyond the scope of their contract or prevents them from working within their own allowable tolerances.
LEADING THE CHARGE
“Project owners don’t always understand why tolerances are what they are. It’s up to us as an industry to not only explain the gaps, but also propose viable solutions for them before any issues arise,” says Brandon Kovarick, Ceco senior project manager.
In March 2021, Kovarick reached out to the Florida Lath & Plaster Bureau (FLAPB) to discuss Ceco’s tolerance concerns. He learned that FLAPB had already published one Technical Bulletin addressing the issue (TB-ST-#03-12), which was endorsed by the Florida Concrete & Products Association, Masonry Association of Florida, and Florida Wall & Ceiling Contractors Association. At the time, FLAPB was still in the draft phase for its update (TB-ST-#03-04.21). These bulletins provide guidance for both stucco contractors and designers.
Brandon’s timing was fortunate. He seized the opportunity to offer Ceco’s assistance with the bulletin update. Working with Ceco’s Director of Quality Control Frank Salzano, FLAPB improved the bulletin by more accurately representing the concrete tolerance expectations outlined in ACI 117 Standard Specification for Tolerances for Concrete Construction.
At the same time, says Brandon, “We learned a lot about stucco, and I’m sure working with Ceco helped FLAPB members increase their depth of knowledge. Imagine if all trades worked together in the same fashion!”
SHAPING RECOMMENDATIONS
Tolerance variations between trades is not restricted to Florida. This is an industrywide problem. To tackle the issue on a larger scale, Ceco approached the ASCC Technical Committee about creating a position statement that addresses the three trade tolerances.
ASCC position statements help concrete contractors clarify contradictory or obsolete specifications. They can be referenced to determine whether the specification or scope of work is realistic and what the contractor can and cannot feasibly do. They also are excellent resources to share with project partners during preconstruction so the project team can discuss applicable issues before they become problems.
FLAPB board member and stucco expert Michael Starks (CGC, CDT, CCPR, LEED, BD&C) of In-Spex LLC also agreed to join efforts to draft this important position statement. The result will help owners and designers industrywide successfully specify their vision and goals.
“Because tolerance issues snowball downhill, it’s just as important to know how your work will affect the trade after you as it is to know how the trade before you will affect your performance,” says Starks. “All trades need to clearly communicate what we can and cannot do before we start.”
CLOSING THOUGHT
Nobody likes the stresses of eleventh-hour change orders. When trades work together to address tolerance gaps, we can provide enhanced, solutions-based planning for our clients.
“Ceco is proud to be part of the movement to help clarify tolerance variances between trades and ensure project budgets reflect the steps needed to close tolerance gaps,” says Phil Diekemper, senior vice president at Ceco. “We are working to help advance the construction industry through education and a higher level of collaboration with other trades so we can improve constructability for our clients’ concrete building projects.”
About the Author:
Victoria K. Sicaras is an account manager with Advancing Organizational Excellence (AOE), a full-service business consulting firm specializing in the concrete and construction fields. Ceco Concrete Construction is the nation’s leading design-assist structural concrete contractor helping clients build high-performing, cost-efficient structures through front-line innovation and technology. For more, visit www.cecoconcrete.com.
Modern Contractor Solutions, November 2021
Did you enjoy this article?
Subscribe to the FREE Digital Edition of Modern Contractor Solutions magazine.
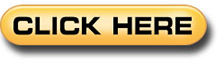