One thing is consistent when it comes to tire maintenance. Tire inflation has been, and always will be, a top concern for fleets.
“It’s been talked about for as long as I’ve been around commercial tires, and that’s close to 40 years,” says Jason Miller, Cooper Tire’s national fleet channel sales manager. “But keeping consistent inflation levels seems to be a moving target. When I’ve done yard checks with large fleets, I’ve seen the good and the bad. And, likewise with drivers. They have a huge impact since they’re supposed to check tires daily—with a gauge, not a thumper.
“The best fleets have tire inflation well under control, with drivers that are onboard with the need for accurate pressure checks—maximizing tire life and keeping tire costs under control. Since quality tires that are properly maintained affect longevity, driver satisfaction, and fuel economy, inflation maintenance is a tremendous opportunity to reduce costs.”
What can be done to ensure a top-tier tire inflation program? Miller offered these tips.
Use calibrated gauges. “Every shop has gauges,” says Miller. “But the question is, are they accurate? Gauges get dropped, and even if they don’t look like it, they’re sensitive pieces of equipment. I’ve tested shop gauges against a master gauge in the past and have found psi readings can be off by 2 to 15 psi. If you’re not testing each gauge, and recalibrating them monthly against a master, there is a good chance you’re inflating tires to the wrong level. Some fleets simply have drivers swap out their gauges for a calibrated gauge once a month. You simply can’t have a good tire program if you can’t trust your gauges.”
Start with the chart. Cooper Tire, like most major manufacturers, provides load-inflation tables based upon Tire and Rim Association guidelines. “With a typical 6×4 legal load, there will be 34,000 pounds being carried by 8 drive tires, or 4,250 pounds per tire. Using the table, you’ll see that the drive tires can support that load at as little as 75 psi fully loaded. Yet, many fleets run a standard inflation pressure at 100 psi because, they tell us, ‘that’s what we’ve always done. It’s easy for our drivers to remember, and it gives us more margin for error if a tire leaks.’”
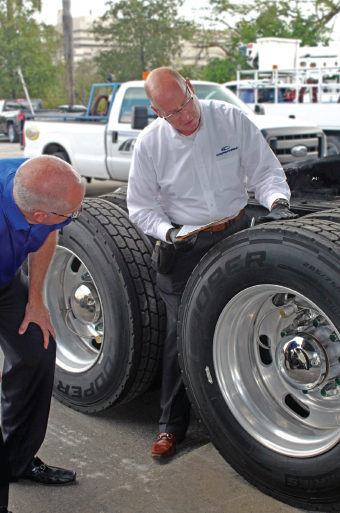
So, what’s the optimal pressure?
“Every tire has a personality,” says Miller. “Likewise, every fleet has a personality. The most cost-effective tire programs come from matching the right tire to the right application at the right inflation pressure. It takes a little time and some discipline but the effort will pay off.”
According to Miller, “We need to think differently about air pressure. The reality is, the tire doesn’t actually support the load, the air does. The tire simply contains the air. Through inflation pressure, you’re primarily trying to manage two things: the shape of the tire footprint and the amount of sidewall deflection. Overinflation can pose several problems. The biggest is premature removal and ride disturbance due to irregular wear since you’re not getting the optimal footprint patch to the road. With the weight concentrated on a relatively small contact patch in the crown of the tire, the shoulders will scrub their way into and then out of the contact patch causing rapid and uneven edge wear. You’re also likely to see significant heel-toe wear and increased ‘road rash’ or chipping of tread rubber in the center ribs. The resulting ride disturbance and general ugliness often result in early removal despite having as much as 30 to 40 percent useable tread remaining. These problems are especially prevalent in mixed service applications running open shoulder drive tires. Next, with such a small contact patch, you’re compromising traction, and that really comes into play, not only in winter but in muddy off-highway operation. You may also see an increase in the occurrence of impact breaks since the tire sidewalls have less flex. Finally, you’re impacting fuel economy.”
Audit your inflation levels. According to Miller, yard checks are a pain, but they’re a necessary evil. “If you’re serious about getting your tire costs in check, you really need to benchmark where you’re at with tire inflation, and identify problem areas,” he says. “Only then can you take steps to improve your program.
Tire related concerns beyond air pressure. “Another area to watch is with retreads,” continues Miller. “It’s back to circumference. In some cases, fleets will get identical retreads back from their retreader, but the casings may be different. Each brand and model may have a slightly different diameter so, while two tires will look identical when you get them back from the retreader, one may be significantly taller than the other. This is why we recommend using a circumference band, good measuring tape, or have a height gauge mounted in the shop to check circumference. Otherwise you may be putting together duals that should be identical, but are really mismatched in height and that will cause one tire to wear prematurely.”
CLOSING THOUGHT
According to Miller, if these tips are followed and you’re running the correct tires for your application, you stand a solid chance of pulling the drive tires at 2/32nds, and the steers at 4/32nds. “And your casings should be in great shape for retreading,” he says. “The way to extend your budget on tires is to get the most miles, coupled with the most retreads. Proper tire selection is one key to doing that, but it’s the maintenance practices—especially proper tire inflation—that keeps your tractors and trailers operating as efficiently and safe as possible.”
For More Information
For more about Cooper Tire’s commercial truck tire lineup, visit www.coopertrucktires.com.
Modern Contractor Solutions, March 2020
Did you enjoy this article?
Subscribe to the FREE Digital Edition of Modern Contractor Solutions magazine.
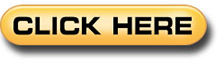