By Greg Austin
The total amount of time needed to complete the waterproofing system installation should be considered carefully when exploring the various product options. Commercial builders, designers, and architects should look closely at the time required for each step, from preparing the materials and substrate to applying the product and curing when evaluating the application. Each waterproofing system option is vastly different, especially when you compare cold-applied versus hot-applied waterproofing systems.
CONSTRUCTION TIME FACTOR
Construction projects are always on tight schedules, as they involve numerous tasks and jobs performed by a variety of vendors or trades, each within specific timeframes and deadlines. It’s necessary to keep the numerous jobs moving along and meeting those deadlines. Delays incur added costs for equipment rentals and for labor, which can be costly as they sit idle waiting to come onsite to start or proceed with a job.
Sequencing is critical as certain jobs on a construction site need to be completed before others can be started and may take some time before enabling a return to service. In the case of waterproofing, the system needs to be fully dried or cured before anyone can enter the area to walk or perform work.
The time needed to complete a waterproofing job is especially vital in an emergency renovation or repair scenario. For example, if a multi-million (or billion) dollar commercial building in a city’s downtown has water from the roof or horizontal deck penetrating the penthouse below, there is a very short window of time (typically only 4 hours) to resolve the issue in order to keep the tenant happy and avoid significant internal damage.
WATERPROOFING TIME FACTOR
Waterproofing is a process that includes several steps: preparing the surface or substrate that is being waterproofed, preparing the materials, priming, detailing, applying the waterproofing product, applying a reinforcement or protection system, and ultimately drying or curing the system. When comparing cold-applied versus hot-applied liquid waterproofing systems, there are vast differences in the number of steps, what’s required for each step and, ultimately—the time needed to perform each step.
Note: Application Guidelines, including the minimum concrete cure time and required preparation, are provided by the waterproofing product manufacturer and should be reviewed specifically for each project.
PREPARATION
Hot-applied waterproofing requires a crew to clean and prepare the substrate, then prime and detail. Detailing is a separate step, demanding a separate setup as an additional material (a polyester fabric) needs to be obtained and applied for the detailing process. In new construction, the concrete must cure for a minimum of 28 days prior to beginning the preparation. It can take days to complete all the preparation required depending on the size and complexity of the project.
With cold-applied liquid waterproofing, there are some systems that can go on 14-day-old concrete. The crew cleans and prepares the substrate in the same way; however, the detailing is greatly simplified. Generally, these steps take 1 to 2 days depending on the project size and complexity, about a third of the time required for hot-applied systems.
Time-saving benefits of cold-applied versus hot-applied liquid waterproofing during preparation: Cold-applied, such as GCP’s SILCOR® liquid waterproofing system, has 2-3 times faster preparation time than hot-applied. Waterproofing can begin 7 days earlier than with traditional hot applied methods. This equates to a 2-week schedule savings over using a hot-applied process.
APPLICATION
Building the membrane with a hot-applied liquid waterproofing system requires five to six layers, including primer, rubberized asphalt and reinforcement, and the protection layers made of separate materials. In addition, there is the time needed—about 3 hours each day—to heat up the rubberized asphalt in a kettle and bring it to 375-400°F. The average hot-applied installation is 2,100 square feet per day in an open area, including primer, first ply, reinforcement, second ply, and protection board. The detail work is separate.
The cold-applied liquid waterproofing membrane requires only two to three layers including primer, which only takes 1.5 to 3 hours to apply. No reinforcement layer is required as the membrane is self-leveling. A comparable cold-applied installation covers 7,000 square feet per day, or more, including primer, membrane and details, and it requires a crew of only three installers. The cold-applied liquid waterproofing application is clearly much simpler, saving time and labor compared to a hot-applied system. Also, the primer can serve as temporary waterproofing in the interim before the membrane is applied. There is virtually no preparation time needed for the membrane material as the crew only needs to mix the product components, per the manufacturer’s instructions, and they are ready to go.
Time-saving benefits of cold-applied versus hot-applied liquid waterproofing during application: With fewer steps involved, cold-applied is 3.5-4 times faster to install than hot-applied (installation time comparison is based on industry information).
CURING/RETURN TO SERVICE
The time that it takes for the hot-applied installation to cure or harden and for the surface to be ready for return to service can be up to 24 hours. Cold-applied installation can withstand foot traffic in as little as 2 hours and enables faster construction sequencing.
Time-saving benefits of cold-applied versus hot-applied liquid waterproofing during curing: Cold-applied can be 12 times faster than hot-applied to cure and enable a return to service.
THE SPEED FACTOR
Cold-applied liquid waterproofing is available in a spray-applied and a hand-applied version. With the spray-applied version, the liquid is simply mixed and applied. It’s a faster application than the hand-applied version, as it allows the crew to immediately apply a single membrane. With the hand-applied version, the liquid is poured onto the concrete surface and spread quickly and easily with a squeegee.
CLOSING THOUGHT
Time is money when it comes to meeting project schedules on construction sites. The time savings offered by cold-applied liquid waterproofing over hot-applied translates to cost savings in terms of labor, materials, and equipment rentals. Among the liquid waterproofing options, cold-applied not only saves time and money, it also provides a more durable product and a safer solution.
About the author:
Greg Austin is the global product director, specialty building materials, for GCP Applied Technologies. He has a background in consulting and almost a decade of experience in waterproofing system development and construction materials.
Modern Contractor Solutions, July 2021
Did you enjoy this article?
Subscribe to the FREE Digital Edition of Modern Contractor Solutions magazine.
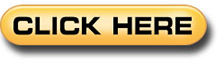