You would have had to have just emerged from a recently unsealed time capsule, or perhaps just completed a 10-year retreat in Tibet, not to be aware of the interest, time, and financial resources being brought to bear on the next generation of environmentally responsible green cements and green concrete construction materials. In fact, if you were to do a Google search on the term “green cement,” you would return approximately 67,400,000 results—or about one result for every ton of cement that was produced in the U.S. last year.
While the volume of information may be daunting, the fact is that there is a convergence of critical market forces that are continuing to drive the evolution to green, carbon neutral, concrete construction materials. Principal among them are new regulatory initiatives, advancements in cement technologies, and an increasingly environmentally focused consumer. Efforts to effect the transition to produce lower carbon, higher durability, and increasingly more sustainable concrete range from emerging voluntary compliance programs to real revisions in industry standards and practices. The challenge to contractors and architects alike is in discerning when these advancements leave the lab and research environments and become commercially available, cost competitive, and practical.
CeraTech Inc. is the leader in successfully delivering alternative carbon neutral, green cement products. Research and development efforts beginning in 2001 have resulted in the introduction of more sustainable cements offering higher performance and greater durability than conventional portland products. Hundreds of projects across a broad range of commercial and industrial applications have been completed. The product has been accepted for use by more than 35 State Departments of Transportation (DOTs). Leading ready-mix producers like Argos and Consumers Concrete have incorporated CeraTech’s cement systems in their product offerings.
CEMENT TECHNOLOGY
The principal point of differentiation between CERATECHTM cement and portland cement is in the physical structure of the concrete produced with these cements. CeraTech Inc. has pioneered the development of a new hydraulic cement system technology that is based on combining activated fly ash with chemical binders or activators. This combination yields an extremely dense, interlocking crystalline network of calcium alumino silicate hydrates, similar in structure to fused glass. The result is a concrete that is much less permeable than traditional portland cement. The density of CeraTech’s concrete eliminates the continuous capillary system that is susceptible to permitting the entry of foreign liquids and gases in to the concrete matrix. These foreign substances drive reactions within a portland cement concrete matrix that will break down the structural integrity of the concrete.
LIFECYCLE ADVANTAGES
The key to achieving a carbon neutral cement lies in our ability to use virtually 100-percent recycled materials. Utilizing 95-percent recycled fly ash and 5-percent renewable liquid activators, CERATECHTM cement develops a concrete matrix that is less permeable than portland cement, resulting in a product lifecycle 2 to 3 times greater than ordinary portland cement concretes. Since CERATECHTM cement is produced through a blending and binding process and not a combustion process, no energy is expended and no CO2 is generated. Therefore, for every ton of portland cement displaced by CERATECHTM cement, one less ton of CO2 is released into the atmosphere from the energy intensive production of portland cement. Imagine, eliminating that type of CO2 burden from being released into the atmosphere by making the change to an environmentally friendly and responsible cement system. CeraTech’s ability to beneficially recycle tremendous volumes of fly ash enables utilities to reduce, and in some cases even eliminate, impondment and landfilling.
CeraTech’s line of cements include: ekkomaxxTM (general applications), KEMROKTM (corrosion resistant), and FIREROKTM (heat resistant) brands. Each cement system exceeds ASTM C-1157, ASTM C-1600, and other important industry standards.
The physical properties of CeraTech’s activated fly ash cement systems naturally provide superior attributes for demanding concrete applications. Because of the low water to cement (W/C) ratio—typically .18 to .23, there isn’t any “free moisture” left in the mix, making it advantageous when toppings and/or floor coatings are to be applied. CERATECHTM cement can be coated in as little as 3 days, compared to 28 days with a portland cement concrete. In addition, all of the brands have a discontinuous capillary system making the concrete a very dense, impermeable material. This physical characteristic also prevents chemical attacks from penetrating the surface through capillaries. KEMROKTM’s design keeps highly corrosive materials from attacking the concrete and surround paste, protecting it from mass loss as with a portland cement mix. FIREROKTM’s properties provide much greater thermal performance. FIREROKTM cement concrete can withstand up to 1,850 degrees F intermittent temperatures and is used by the military for vertical take-off aircraft pads.
BUSINESS AS USUAL
It is important to note that the product mixes, and places, like portland cement concrete. There is no change imposed on the way you work. Since CERATECHTM cement utilizes liquid activators, there is more mix design flexibility in the range of set times and strengths based on specific project requirements.
In closing, I’d pose the following question, “If you could use an already established, next-generation cement that outperformed portland cement, offered tremendous carbon reduction and environmental advantages, had a longer product lifecycle, and was competitively priced—why wouldn’t you?” ■
About The Author:
Mark Wasilko is the executive vice president for CeraTech. For more information about CeraTech Inc. and its family of sustainable cement products, call 800.581.8397, or visit www.ceratechinc.com.
_________________________________________________________________________
Modern Contractor Solutions, June 2013
Did you enjoy this article?
Subscribe to the FREE Digital Edition of Modern Contractor Solutions magazine.
The Reality of Green Cements
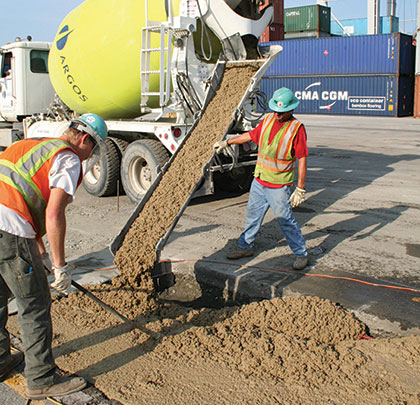