Being in the construction management business since 1938, the Linbeck Group has had a unique opportunity to be part of the transformative, game-changing process that technological innovations have brought to the industry. These specialized technologies have advanced leaps and bounds in the more than 30 years since Linbeck built the original Cook Children’s Medical Center in Fort Worth, Texas.
By fully embracing spatial coordination through Building Information Modeling (BIM) and a supporting suite of applied technologies, Linbeck has turbocharged its latest project for Cook Children’s, a $220 million expansion to the south side of the medical district campus to support one of the busiest pediatric hospitals in the nation.
THE PROJECT
At the core of the south expansion project is a high-performance, 19,000-square-foot utility plant comprised of chilled water and heated water systems, normal and emergency power, and switchgear to support a new south tower heart center, medical lab, sterile processing department, and surgery center, while also providing redundant service for the balance of campus.
Making the project more complex, a 6-story parking garage and two busy streets stood between the 6-story south tower and the utility plant that supplies it. In order to connect the campus and utility plant, Linbeck had to excavate an open-cut utility tunnel beneath the streets and parking garage structure to make the utility connections.
Serving as construction manager at risk, and leader of an Integrated Project Delivery (IPD) team, Linbeck leveraged the power of spatial coordination through BIM, a process that required carefully orchestrated collaboration of all stakeholders to build the south utility plant on time and under budget.
Featured Image: The BIM model clearly shows the complexity of the systems needing to be installed for the Cook Children’s south utility plant.
Above: When the BIM model matches the finished product, it’s easy to see the advantages of specialized technologies to take a project from concept to completion.
COORDINATED EFFORTS
Well before mobilization on site, an eight-member core team was formed to discuss coordinating the model and facilitate communications. Comprised of representatives from the design team, various trade contractors, and the owner, they established operation protocols and weekly meetings to work through spatial coordination and discuss and resolve conflicts in advance of fieldwork.
As a main repository of information, BIM 360 Field, a QA/QC mobile platform, facilitates quality assurance and quality control by using checklists and issues tracking in the field along with QR codes to track equipment delivery, installation, and commissioning status.
BIM also allows the project team to move quickly on field RFI’s in a matter of hours versus weeks, thereby avoiding long approval processes. Daily, a designated model coordinator works to resolve variances and clashes discovered by the job team, and bring those solutions forward for approval to a “BIM Cluster”—small groups of project team members with particular expertise in specific disciplines. “We could send in an RFI with a proposed change and it would be reviewed in the model for almost immediate approval,” says Linbeck’s project manager Todd Zdunkewicz.
By utilizing the spatially coordinated model, trade contractors were able to import the model directly into their fabrication equipment, allowing them to create precast concrete panels and lids and prefabricate electrical and mechanical systems for the 12-foot-by-12-foot utility conduit, reducing time and material waste significantly. Chilled water lines planned for the same location as fire protection were corrected before either work began, a conflict that would otherwise have not been found until well into construction with significant time and cost impacts.
CONNECTED COLLABORATION
To facilitate faster communication, modelers for all parties worked side-by-side in a co-located office and, while in the field, a single Knaak data vault with a 40-inch monitor allowed the job foreman to coordinate installation crews. Group collaboration meetings would routinely occur in the field around the data vault. Once common agreement and understanding was achieved, the crews carried the revised plans to their respective workstations on iPads, which were purchased for the project to fully connect all the firms working from one 3D model.
For quality assurance, BIM 360 Field works in tandem with 3D laser scanning. The point cloud, created from several laser scans, is used to compare ongoing construction to the spatially coordinated model for all systems being installed. Any variances found in the comparison are either adjusted in the field when the variance causes an issue with other installed components or the model is adjusted and used for as-built purposes.
To enable project collaboration from anywhere and on any device, the cloud-based file sharing platform Box was utilized as a secure hub for all drawings, submittals, and other project documentation. This data was also linked to BIM 360 Field to enhance the QA/QC effort.
Linbeck Group has made technology its number one priority in an ongoing effort to continuously improve and enhance its ability to add value for clients. Moreover, forming strong ties with the owner over the past three decades, the construction firm has built a high level of trust with Cook Children’s, which has facilitated the implementation of new planning strategies and technologies to allow a core team to work collaboratively and efficiently for improved outcomes.
Through effective utilization of a suite of applied technologies, the south utility plant project, designed with redundancy and MEP systems to serve future expansions, resulted in more than $6 million in savings from the original budget estimate with zero lost-time injuries. Spatial coordination, laser scanning, use of a mobile QA/QC platform, and collaborative sharing through Box actually encouraged a much higher level of collaboration and lead to the destruction of the traditional knowledge silos typically found in the design and construction industry. ■
About The Author: David Stueckler is the chief executive officer with Linbeck Group, based out of Houston, Texas. For more information, visit www.linbeck.com.
_________________________________________________________________________
Modern Contractor Solutions, October 2015
Did you enjoy this article?
Subscribe to the FREE Digital Edition of Modern Contractor Solutions magazine.
The Power of Spatial Coordination
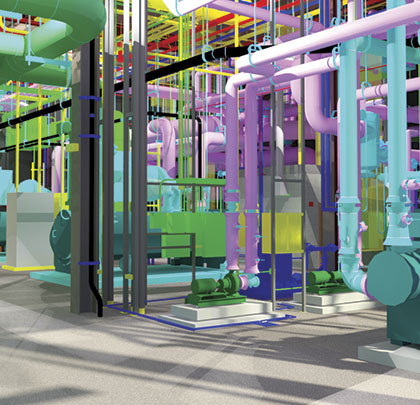