The construction industry is a pivotal and powerful part of the American economy. The noise at a jobsite is the sound of commerce, progress, and the flow of money through many hands. But that vibrancy comes with risk, both to construction workers and the companies who employ them. Every day of the year about 6.5 million people report for work at approximately 252,000 construction sites nationwide.1 These workers handle complicated machinery which can be difficult to manage on large jobsites where numerous projects are being executed simultaneously. Understanding this reality, both construction companies and contractors need to make every effort to ensure that they and their employees are doing all they can to control the hazards inherent in such an environment—and to control other factors that pose risks to the company’s bottom line.
MOVING FORWARD WITH TELEMATICS
A solution to these challenges can be found in the selection of the right telematics system. Construction business owners and managers are empowered through telematics to improve jobsite control, operator safety, and increase efficiencies over a broad operational range. The availability of real-time location data can help them utilize equipment and manpower more efficiently, leading to the identification of counterproductive trends before they can have an effect on project deadlines or result in equipment failure.
What was once a labor-intensive process of physically walking the grounds of a jobsite to see that equipment was being utilized effectively and was located in its proper place, has now evolved into an opportunity for owners and managers to oversee the site remotely, more productively, and in real time. The legacy type of manual oversight is no longer the only management option as jobsites continue to grow larger and technology evolves.
An example of the new technology available is geofencing, a feature of most telematics systems that enables credentialed managers to set invisible boundaries for designated machinery, and provides alerts when those machines move outside of that perimeter, regardless of what time of day it is and whether or not there are physical eyes on the jobsite. Management can also be alerted to unauthorized equipment use. For example, you can set a parameter: from 5:00 p.m. on Friday through 6:00 a.m. on Monday, if no equipment should be in use, you can set an alert to notify you if a machine is being used.
Perhaps the foremost benefit of the technology driving these solutions is the ability to manage and minimize circumstances which negatively affect operational efficiency. The ability to proactively mitigate risk, rather than cope with loss once problems have occurred, is a key advantage of adopting technology to manage your fleet.
PROTECTING THE BOTTOM LINE
The reporting that telematics provides on machine fuel consumption, and the automation of maintenance schedules, can increase your company’s bottom line and are often referred to as the first return on investment points. Another example of the value that telematics brings to the construction industry is maximizing fleet inventory and equipment rental investment; by providing a better understanding of equipment utilization patterns across jobsites, managers can accurately plan fleet acquisitions and machine operator manpower.
RISKS POSED BY UNAUTHORIZED MACHINE USE
As a result of having the ability to better control where and when machinery is being used, construction business owners and managers are also able to better police workers who are putting in unauthorized overtime by operating machinery outside of approved work hours and areas. This practice is of concern for two reasons: First, unplanned overtime can throw off the overall budget for an entire project; and second, the lack of supervision on a jobsite outside of working hours can easily lead to an increased potential for accidents and a reduction in worker safety.
Unauthorized use also poses an insurance risk for construction companies, as well as a threat to the company’s all-important reputation, which could suffer from a poor safety record or history of fiscal irresponsibility. Maintenance expenses are further exacerbated if the equipment in use is being habitually damaged because it is over-utilized or handled by operators who aren’t properly trained or supervised.
Telematics provides a host of new capabilities for construction business owners and contractors to help eliminate financial risk and prevent losses before they occur. From increased jobsite monitoring to real-time data about how and where machinery is being used, business leaders are ultimately able to streamline equipment utilization costs and minimize risk to the company and its workers. Without the critical insight into jobsite and business logistics that telematics provides, business owners and managers too often made operational decisions in the dark. With the illumination that telematics bring to numerous areas of machine operations, business owners and managers can remotely see and control more than ever before. ■
1 OSHA, “Work Safety Series: Construction,” www.osha.gov/Publications/OSHA3252/3252.html
About the Author: Courtney DeMilio is the national vice president of LoJack Construction at LoJack Corporation.
_________________________________________________________________________
Modern Contractor Solutions – May 2016
Did you enjoy this article?
Subscribe to the FREE Digital Edition of Modern Contractor Solutions magazine.
The Gears of Innovation
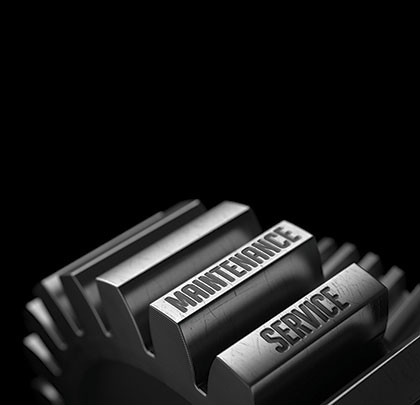