What is the best way to reduce accidents in the workplace? According to the Occupational Safety and Health Administration (OSHA), developing a strong safety culture has the single greatest impact on accident reduction of any process. For this reason all companies will want to focus on creating a safety culture.
WHAT IS A SAFETY CULTURE?
In a strong safety culture, every employee feels responsible for safety. Employees are empowered to identify and correct safety issues as they arise.
A “say it when you see it” philosophy is key to creating a safety culture. In a safety culture, for instance, an apprentice would feel comfortable walking up to a foreman and reminding them to wear their safety glasses. This behavior is not only encouraged, it’s rewarded in a strong safety culture.
How can a company instill a safety culture? They can adopt the four “E’s” of a SMART Safety Culture, which are:
- Establish safety as a core value
- Empower everyone
- Elevate safety advocates and eliminate opposition
- Exhibit a commitment to safety in all actions
The following are practical steps you can take in order to establish a SMART safety culture at your company.
Establish safety as a core value. Top management “buy-in” is essential. Top management needs to adopt safety as a core value to maintain equal footing with other core business interests, such as production, quality, and profitability. They can show their buy-in by repeatedly sending the right message, at all levels of the company, at every meeting.
When management reviews safety performance, employees take it seriously.
Develop a written program and a system of accountability so everyone understands their roles and plays by the same rules. Written programs should be realistic and usable, so make the written program brief and use direct language without any fluff. The whole safety program only needs to be about 100 pages. Keep the IIPP, MSDS, and all the rules and regulations in one document.
Align the organization by having management and supervisors take a leadership position in communicating the safety and health goals and objectives with the rest of the company.
Empower everyone. It’s important to create a communication infrastructure. The success of your safety and health program is directly correlated with the frequency it is discussed at your company. So communicate safety on a regular basis—at weekly safety meetings, at monthly company meetings, at new hire orientations, and after incidents occur.
Supervisors need to correct, record, and report improper behavior when it occurs, seeking to gain employee buy-in to change behavior. As reinforcement, they should also involve management in the follow-up to disciplinary action.
Provide training. Provide safety and health training first to your core group of people so they get onboard with needed changes and become safety champions. Then broaden the training to the rest of the employees. Training should cover the company’s code of safe practices, policies, disciplinary action protocol, and the employee’s responsibilities. Watch out for employees paying lip service to the program instead of truly embracing it. Follow-up is recommended to ensure that employee’s understand and have truly bought in to the safety and health program.
Establish a safety business meeting monthly or quarterly with managers and other key people. This is an opportunity to get everyone on the same page and keep top-level management in the loop. At the safety business meeting, you should review all incidents, jobsite inspection results, and disciplinary action. You should also discuss future training and policy development.
Elevate safety advocates and eliminate opposition. Define roles and responsibilities at all levels of the organization and develop a standard reporting procedure. Safety and health must be viewed as everyone’s responsibility. Develop recognition and incentive policies rewarding employees for doing the right things and encouraging participation. And for those people that don’t support the safety culture, you should put them on notice.
Exhibit a commitment to safety in all actions. Continually measure performance, communicate results, and celebrate successes in order to sustain efforts and keep everyone motivated. Jobsite audits should be unannounced and performed frequently, weekly or monthly. The employees being audited need to know what to expect, so develop a standardized checklist.
Develop an ongoing measurement and feedback system that encourages positive change instead of focusing solely on the bottom line. What gets measured … gets done. Some important things to track include accident rates, loss reserves, experience modification rate, and employees completing essential paperwork.
CONCLUSION
As insurance costs rise (and they will rise) you can separate yourself from your competition by reducing the number of employee injuries. Companies can save between $10 to $20 for every dollar spent on safety. The surest way to maximize this investment is by developing a SMART safety culture so that safety efforts remain in the organization long into the future.
■ ■ ■
[divider]
About the Author Vince Hundley, MS, CSP, STS is the president and CEO of SMART Safety Group, a full-service safety company providing safety products, safety services, and OSHA training to thousands of employees in the construction industry. Vince also serves as the safety director of the AGC of San Diego, where he oversees all safety training staff, curriculum development, and regulatory affairs. Vince has 20 years of comprehensive safety experience and management experience working for a diverse group of employers. For more information, visit www.smartsafetygroup.com.
Modern Contractor Solutions, June 2014
Did you enjoy this article?
Subscribe to the FREE Digital Edition of Modern Contractor Solutions Magazine!
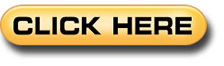