When a parking lot concrete overlay job is commissioned, there are standard procedures regarding the different design elements of the job. One such element is the curb, which historically has been approached in one of three ways:
- Remove and replace poor curbs
- Remove pavement adjacent to the curb and tuck the overlay in
- Overlay against existing curb and lose curb height
Generally, method (a) is used when the curbing is in disrepair and needs to be reconstructed. Options (b) and (c) are done when the curbing is in fair to good shape, but still come at other ancillary costs to the design and construction teams. With option (b), there is additional cost associated with the 4-8 feet of pavement removal, which allows for the grade transition to maintain full existing curb height. Additionally, drainage must be surveyed to assure the grade change in the tucked sections does not pool, or move water adversely to the surrounding environment. Option (c) overlays the concrete lot directly against the existing vertical curb, thereby losing 3-4 inches of curb height, and the resulting shorter curb height becomes another drainage consideration engineers must study to ensure the remaining height is sufficient to manage the water flow and gutter spread. The other smaller, but evident, issue with (b) and (c) is that you end up with a bright new concrete lot, but do not have the visual consistency of the existing curbing system, which typically has a contrasting hue as compared to the bright white pavement surrounding them.
Well, if you’ve ever taken a multiple-choice test, you’ve noticed that there are usually four options to choose from, right? We agree, and despite the three existing options being somewhat evenly implemented over the 50-plus concrete overlaid parking lots completed in the past 15 years, there have been quite a few of those lots that were begging for a little innovation. Using sound knowledge of materials and deep understanding of concrete engineering properties, an option (d) was destined to be born.
A FOURTH OPTION
In the fourth quarter of 2022, the Concrete Council attended a preconstruction walkthrough as a contractor was about to begin work on building the third and final lot of a large project. During this walkthrough, an interesting question was posed by the Concrete Council with the rest of the team, “Could we overlay the existing curb, as opposed to the plan removal and replacement of it?”
This idea had its roots back when the entire project was being designed a year prior. At that time, the local ACPA chapter took the idea to the national stage where other Chapter State Executives weighed in on this concept’s history. Unfortunately, there was not much documented history to properly assess the pros and cons of such an approach to the curb. In the end, the design team decided to play it safe and stick with what they knew. Because they were not too sure of the ultimate outcome of such a bold new strategy, they opted to go with a traditional removal and replacement. They did not want to create such a large “unknown” for the owner of the lot, especially when considering this was the first time the lots would be overlaid in concrete. However, the idea lingered in the minds of some of the ACPA members.
When this idea resurfaced before construction on the third lot two years later, it began to seem more plausible. As the field conversations began to pick up momentum, and the idea was shared with the agency leadership and contractor, it was clear that there may be an opportunity to give this novel idea a try. Although there were still some unknowns regarding the theory and benefits, and there were still some concerns expressed by the design team regarding the lack of quantifiable data on the approach, the agency decided to give it a try.
THE EXECUTION
The Concrete Council staff worked side by side with the contractor and owner to pour the curb cap monolithically with the 4-inch overlay. During this time, they could communicate in real time with the staff to ensure best practices and placement applications were being followed so that this novel approach would have the very highest chance of succeeding.
Ultimately, the design decision was made to cap the curb with a minimum of 2 inches of fiber reinforced PCCP on the vertical face along with 4 inches on the top face in order to raise the curb height in conjunction with the overlay. There were four guidelines/practices that would need to be followed for the highest possibility of success:
- The curb would need to be power washed thoroughly to remove the various oils, dirt and grime present
- The forms needed to be in exact alignment with the existing curb, ensuring the 2-inch minimum clear
- A full depth sawcut was required 8 inches from the face of the curb, to help relieve stresses from pulling on the cap
- Any existing joints must be precisely matched to the overlay
THE RESULTS
By the end of the project, more than 400 feet of existing vertical curb was overlayed, and out of this, a new name for this application was born, a “Crown Curb.” Per the owner’s testimony, this method saved nearly $10,000 from the initial bid prices for removal and replacement of the existing vertical curbs.
CLOSING THOUGHT
Since installation, the Crown Curb has been continually monitored. Post construction observation has shown zero cracking or bonding issues, and all parties involved consider this to be an overwhelming success.
About the Author:
Jesse Jonas, P.E. is a civil engineer serving the Concrete Council of St. Louis, whose primary goal is to increase the incremental use of concrete construction in the area by serving as a resource to owners and agencies considering concrete construction. Membership is made up of firms in the St. Louis area involved in concrete production and construction. The Council provides technical input, site visits, in-house presentations, and cost comparisons, at no cost, for consideration of concrete construction. For more, visit www.concretecouncil.com.
Modern Contractor Solutions, September 2023
Did you enjoy this article?
Subscribe to the FREE Digital Edition of Modern Contractor Solutions magazine.
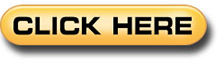