When it comes to asphalt, measuring pavement density is key to building longer-lasting roads. Paving contractors must ensure that the pavement is compacted enough to ensure long-term asphalt health. In addition, identifying the percentage of air voids in the overall placed pavement mix is the accepted measure of evaluating this key factor to the integrity of the roads. The current industry standard for measuring compaction and air voids are point-by-point techniques such as coring or using a nuclear density gauge, but up-and-coming Ground Penetrating Radar (GPR) technology could provide a better alternative.
The trouble with point-by-point techniques
Point-by-point technology is limited in terms of density testing. With these techniques, inspectors measure random sample locations of the pavement and extrapolate this data to the entire road. However, this technique does not cover a large area and could potentially miss problem areas. As Kyle Hoegh of the Minnesota Department of Transportation explains, “You could be at a location that is well within passing density, then move just a few feet away on the pavement and observe a failing density, which does not make spot-check methods well-suited for getting a reliable assessment.” Coring is currently the golden standard for assessing pavement health, but it has further issues. This destructive method tests for air voids at the cost of pavement integrity. Sometimes additional resources and road closures are needed to fill in these cored areas. Besides being destructive, this method also is lacking because it cannot provide real-time data, but rather requires a lengthy and costly process of sending out the cores to be analyzed. Nuclear gauge testing, another point-by-point method, requires certificates for safety and operation, which can be cumbersome.
The benefits of Ground Penetrating Radar
While coring is destructive, Ground Penetrating Radar is a non-destructive method for analyzing pavement. Kyle Hoegh explains, “The technique of using a dielectric constant to relate to asphalt density has been around since at least the 1990s… but up until recently, the technology wasn’t precise enough to be able to use it for deployment on actual asphalt pavement projects.”
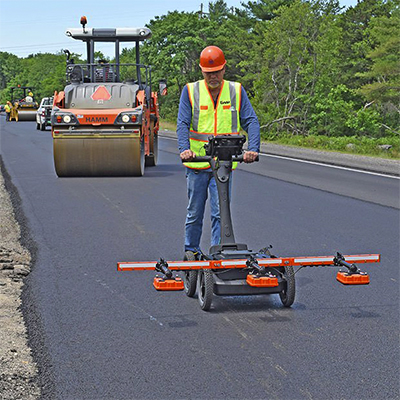
using GPR and getting real-time data on pavement density.
Minnesota Department of Transportation’s studies uphold the value of GPR in paving
In 2020, MnDOT joined a group of states and the Federal Highway Administration in creating a pooled fund to experiment with GPR technology to improve asphalt pavement density. MnDOT became the leader of this national pooled fund, focused specifically on deploying continuous asphalt pavement compaction technology. Through this project, MnDOT collaborates with researchers and on-the-ground workers such as foremen and contractors in a unique and iterative process. Currently, MnDOT is familiarizing contractors with the technology so they understand the information it provides and how it can assist with construction practices. Contractors also provide valuable feedback in evaluating the protocols that are in development, with the ultimate goal of rolling out GPR as a quality assurance tool in Minnesota or recommending it for quality assurance nationally. MnDOT provides density assessments throughout the project as a trial in creating protocols for future work. Kyle Hoegh explains, “There are many contractors already doing everything they can to try to get consistently good density and are looking for any sort of information that can help them continue to improve. They’ve been very receptive to trial data collection on their projects, and we’ve even had multiple contractors using the information from the GPR technology to improve their compaction operations.” The process thus far demonstrates the effectiveness of GPR in paving.
For example, a MnDOT team recently tested the technology on a highway echelon paving project. Two asphalt pavers were simultaneously paving both lanes of a two-lane highway, which allows for good compaction at the longitudinal joint, or the area between those two lanes since the compaction occurs while both lanes were hot. However, the MnDOT team was able to use a density profiling system to identify that less than a foot away from the joint there was a problem. They noted periodic lower densities along one side of the joint, for as long as 100 to 200 feet stretches. The MnDOT team was then able to collaborate with the contractor in real time to brainstorm. The team identified what was causing the lower densities and made the necessary changes to ensure adequate pavement density.
GPR in the Future of Paving
These MnDOT projects have demonstrated the potential of GPR technology. The advent of the use of intelligent construction technologies in day-to-day work is occurring at MnDOT and other partners. The continued expansion of these technologies could benefit other states and even countries as more and more information about the paving process becomes available. Work to date shows that longer-lasting road integrity through improved density is on the horizon if this technology is adequately implemented.
A case study provided by the Minnesota Department of Transportation.