The case for training earthmovers in the age of technology.
In a world as rapid changing as the construction business, it’s not surprising that the firms who survive and prosper are the ones who keep themselves current with new ideas and training. The expectations have changed. Contractors are expected to work harder, faster, and better … and within budgets where errors, rework, and unplanned costs can eat up an already slim margin. To address these demands, construction contractors have turned to technology to help improve productivity, efficiency, and quality of the end result.
Earthmoving and paving contractors have learned that technology can be a tremendous tool in their success. Paper site plans and jobsites populated with wooden stakes are fast being replaced by 3D models and GPS machine control that can automatically govern heavy equipment to match the exacting details in a digital site plan.
“Just purchasing the technology is only half the battle,” says Mark Contino, global vice president of product marketing, Topcon Positioning Systems, Livermore, California. “If customers don’t have the level of training needed to fully understand and properly use this powerful technology, they will never realize its full potential.”
CONTRACTOR TRAINING
The major developers of earthmoving technologies have been providing contractor training for years. Initially, it was start-up and on-site training to assist machine operators, who were accustomed to operating equipment using their years of experience and “gut” feel.
“These operators learned through training and demonstration to appreciate and allow the advanced technology guiding the machine to help them complete their tasks faster, better, and easier,” says Contino.
With refined and newer technologies being developed, the innovative suppliers of site planning, site positioning systems, and GPS machine control technology are offering advanced training opportunities through large training events, boot-camp-style training courses, online tutorials (webinars), and specialized training programs at spacious, fully equipped training facilities.
No matter what the tool is, there are increases in the efficiency and productivity that will be achieved with that tool after training on how to use it properly and, more importantly, to its fullest potential. When contractors invest in new technology, the first step is to properly train employees, so that they can know how to use and receive the most out of it.
ADVANCES IN TECHNOLOGY
As technology advances, so does the demand to make the learning and use of the technology as simple as possible. In many machine control systems and data management solutions, users can become fairly proficient with minimal training. Technology developed for more complex tasks using systems intended for multiple functions require more training in order to become proficient.
Providers have been refining their technology with each successive version, making them more and more user-friendly and enhancing the product’s capabilities with every technological change. Easy-to-use machine control has evolved from giving single machine operators the ability to learn how to operate a technology-driven machine into data acquisition and field-office communication connectivity. This changes how contractors manage their businesses and decide what depth of training is required.
Training helps the contractor and machine operator to take full advantage of technology. For example, Topcon’s 3D-MC GPS+ machine control products are specifically designed to be simple to use, and for machine operators to become productive with basic functions with just a few hours of training. There are many features on the product that the operator may not know exist. He may not get the work done as efficiently as possible or realize the full potential of the technology without additional training.
KEY TO SUCCESS
“The key to contractor success is not just that one operator learns how to cut grade using 3D-MC machine control, but that the contractor’s approach to business can improve dramatically if management embraces technology at every phase of the job,” says John Dice, senior trainer, Topcon University, with Topcon Positioning Systems. “To achieve full benefits of Topcon systems, training must be viewed as a prioritized company-wide initiative.”
Dice says: “Instead of the foreman and grade setter laying out paper plans on the hood of a pickup, the job designs reside in electronic format that will be viewed on a computer screen in the job trailer, or a tablet in the pickup, or the survey rover’s controller, or the machine control box, located in the operator cab.
How did the job design files get there? How does the contractor match the electronic job plans to GNSS position measurement? The Topcon system can minimize the amount of surveyor staking required on the jobsite, but without the stakes how can the grade setter verify that the grade was cut properly? What if they need to place a few reference stakes, but don’t have the surveyor’s hubs as reference?”
The point is that machine control is designed to be a benefit to the contractor, to save time, to increase productivity, and simply, make more money. Since using it changes traditional methods of construction, every employee in every step of a job needs to understand how these new technologies work and how dramatically they can enhance every phase of every job. Employees have different tasks to make using the technology a success. Therefore, training becomes the catalyst forcing the different parts the contractor’s organization to coordinate their efforts. ■
Read the conclusion of The Art of Keeping Current
About The Author:
Based in Chicago, Jack Lucic is a freelance writer covering construction, management, and insurance topics. He can be reached at jacklucic@yahoo.com.
_________________________________________________________________________
Modern Contractor Solutions, April 2013
Did you enjoy this article?
Subscribe to the FREE Digital Edition of Modern Contractor Solutions magazine.
The Art of Keeping Current
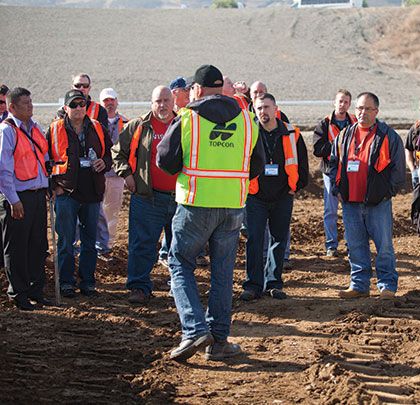