By Shashank Bhatia
As global regulations continue to evolve, MEWP (Mobile Elevated Work Platform) makers will be forced to adopt, deploy, and develop new technologies. One such technology is the incorporation of a load sensing system (LSS), one of many new systems soon to be required under the new upcoming American National Standards Institute (ANSI) standards to be published. This Load Sensing System provision mandates that an MEWP include a means of monitoring platform weight.
For scissor lifts, a pressure-based load sensing system is used as a regulatory safety system designed to monitor the load of persons, materials, and tools in the platform, ensuring vehicle capacity ratings are not exceeded. Apart from the basic requirement stated above, this system also has other functional, calibration, and diagnostic requirements to ensure operator safety.
FUNCTIONALITY
A pressure-based load sensing system typically comprises of redundant pressure transducers on a scissor lift to monitor force acting on the main lift cylinder. The system also includes redundant elevation sensors to monitor platform height. The use of a redundant sensors is driven by the new standards as a means of monitoring the health of the load sensing system.
Solutions vary between manufacturer such as the number of lift cylinders present in the arm stack, the location of transducers, the number of sensing elements per cylinder, and the mathematical algorithm used to calculate the platform weight.
To determine a platform load, sensor data is measured (both elevation and cylinder pressure) against data recorded in the calibration process, specifically a map of no load and full load conditions with respect to elevation. The current data from the sensors is then calculated to determine its relative position within that map, resulting in a mathematical load determination. The Aerial Work Platform then determines if the load is greater than the maximum allowable operating capacity of the vehicle when operating indoors or outdoors.
In the event of an overload, the MEWP notifies the operator by sounding an alarm sequence and indicator lamp in the platform and ground controls. The MEWP will then disable all drive functionality, all steer functionality, and prevent further elevation until the overload state is clear or the load sensing system sensors are repaired and recalibrated. In the event of an emergency, a manual descent system or the ground control station may also be used to rescue an elevated and incapacitated operator.
CALIBRATION
Scissor lifts with a load sensing system require periodic recalibration due to wear or component failure. Some manufacturers specify a service interval of twelve months. This is either a retest of the system with maximum rated load as well as overload with the existing calibration or a condition-based calibration verification. During a routine service interval, when a sensor fails, or when a machine fails to pass an annual inspection, a technician must perform an LSS calibration so the system can learn the MEWP’s new mechanical characteristics.
During a calibration most scissor lifts will require the operator to load the platform with weights to maximum platform capacity. The control system then uses both pressure and height to generate a dynamic pressure calibration curve which can be used to determine if an overload condition exists.
A zero load or empty deck calibration instead of a maximum weight calibration typically requires only a diagnostic tool, without the need for platform weights. One of the main benefits associated with a weightless or empty deck calibration, is the ability to repair units in the field without any load in the platform, only suffering a slight impact to performance. A field calibration with zero load would compare measurements with the last calibration and provide a full use of the machine system if within tolerance the calibrated parameters.
DIAGNOSTICS
In the case of an overload situation occurring, sensor and status information can often be presented in real-time for operators and technicians. To remove the overload condition and resume normal operation, the operator must remove weight from the platform until the overload condition no longer exists or a technician may have to repair the machine. Both the platform and ground visual indicators will display when overload is active in addition to when the platform is no longer over capacity.
Some load sensing systems can present challenges that could affect diagnosing when the platform is being overloaded. For example, when machines are running in the cold, hydraulic oil tends to become viscous. As the oil in the rod side of the cylinder gets more viscous, it makes it more difficult for the piston to push the oil out of the barrel end to elevate the scissor.
The increased rod pressure then pushes back on the piston, increasing the pressure on the head side of the cylinder therefore increasing the platform load measurement. As this happens, the pressure in the barrel end of the cylinder increases because it thinks the machine is trying to elevate a large amount of weight, when in fact the sensor is reading the effects of viscous oil. This can commonly lead to a false reading with load sensing systems that only measure barrel-side pressure.
NEXT GENERATION LOAD SENSING SYSTEM
JLG uses a pressure transducer on the rod side of lift cylinders in addition to the head side of the cylinder. This approach compensates for hydraulic fluid viscosity in low temperatures. In addition, JLG has developed a means of verifying the integrity of the LSS calibration called Load Verification. This is done by running a single lift cycle up and down from the ground station with an empty deck, verifying whether the machine characteristics have changed significantly from their last calibration. The advantage of this is that service technicians can process a fleet of vehicles very quickly, isolating the out of tolerance vehicles from the healthy vehicles. The technician can choose to partially or fully recalibrate the vehicles once the necessary equipment is available such as an overhead crane and the correct collection of test weights.
SUMMARY
New ANSI requirements coming into effect in 2019 will challenge MEWP manufactures to provide a Load Sensing System that limits an operator’s ability to put him or herself in an unsafe condition while operating an MEWP. Load sensing systems will take all the lessons from prior systems and improve the calibration, functional, and diagnostic performance of the machine.
About the Author
Shashank Bhatia is the senior director of engineering and is responsible for JLG’s scissors, verticals, and low-level access product development. He has worked in the construction equipment industry for 17 years gaining experience in service, marketing, product lifecycle management, as well as engineering.
Modern Contractor Solutions, May 2019
Did you enjoy this article?
Subscribe to the FREE Digital Edition of Modern Contractor Solutions magazine.
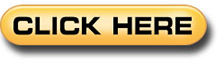