Civil contractors are optimistic about the industry for 2023 and 2024, per the most recent Civil Quarterly from Dodge Construction Network. The report states that “there are no significant differences by contractor size for their 12–24 month outlooks. This demonstrates that the boom in work is impacting all types of civil contractors, and this is expected to do so for some time.”
HCSS, a construction management software provider, interviewed several of its customers about their outlook for the future in the industry. A summary of these discussions follows:
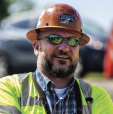
INTERVIEW: PHILLIPPE FALKNER
ENGAGE EMPLOYEES MORE
Phillippe Falkner is the safety director and business services specialist with Ed Bell Construction in Dallas, Texas. Ed Bell has been a heavy contractor in business since 1963. Phillippe discusses what the industry needs to engage employees more.
People’s goals, desires, and reasons to be at work have changed so much over the past 24 months, and it’s still changing dramatically and fast. The supply chain and technology have also changed. Every time executives get their heads wrapped around this change, employees have moved on. C-level executives and company owners need to engage more with their employees to understand why workers stay at the business.
Employees must be engaged as equals—from the entire management team to operators and laborers. Employees should be asked, “Why are you here? Why do you stay here doing what you do?” Many in the industry think, “Well, they are here because they need a job.” That is not true, as every one of our employees could be making a comparable wage at a big box retailer. We need to figure out why this person is a contractor and why they are here. Why are they doing this as opposed to doing something else? Why are they building roads?
For some people, it’s a family business. Others have a great curiosity about the engineering behind it. Still, some people have a passion for doing something that feels important to the community. For Phillippe, “the cool part is that I get to build something that wasn’t there before. I help get people places.” If your business can understand why people work there, owners and executives can keep the employees working there. It’s all about how you communicate with each other.
The military traditionally does a good job communicating with their troops. We can all learn this lesson—you must keep your people informed. The construction industry has issues keeping employees informed, not on what to do and when to do it, but why. Understanding why employees are working at your business can help to motivate them to get even more engaged.
More importantly, these people have different reasons for getting up every day and coming to work. Six months from now, a third of them will have a different reason because they have life changes. Since life changes faster than many of us want to deal with, we must expend resources, time, and effort to engage with our people on a communicative level about why they are here. Employees are the most critical asset in the construction industry, and executives need to spend every day engaging with them.
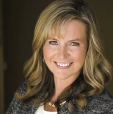
INTERVIEW: MARY TEICHERT
ENVIRONMENTAL PRACTICES
Mary Teichert is the president of Teichert, Inc., a 135-year-old contractor regionally based out of California and Western Nevada. It was started by her great-great-grandfather, Adolf Teichert, a foreman for the man who invented expansion joints. Mary discusses the impact that environmental practices have on the industry.
Teichert has an interesting contracting business because they own and operate materials plants—about 25 rock plants in California and Western Nevada. Because these are stationary facilities, Mary’s company has built a depth of expertise in environmental management. These skills and awareness bleed over into the construction industry as they are stewards of the land they are working on.
So as a steward of the land, Mary often questions what the company needs to do. They need to understand technical requirements, like emission regulations, testing stormwater runoff, and increasing government regulations. As a regional contractor, many people that work at the company live nearby, so the more the company can take care of the resources they care about, such as the air they breathe and the water they drink. This is important for future generations.
It’s a balancing act—managing and measuring the most critical things or understanding if something is worth the tradeoff in costs. We spend millions of dollars yearly on our capital program, and replacing and buying equipment is a non-trivial project.
Our industry also cares about things like small and disadvantaged businesses. We can only say that we should be investing in more technology to keep the air cleaner if we have paid attention to what that means for someone with limited capital that may not have used up the life of their previous equipment. There is a balance that needs to be done between all the different goals that exist. Plus, we need to stay in the conversation about what stewardship means, how we will do it with the tools and technology we currently have, and how we can meet the requirements of the built environment that we are developing.
Some people feel like cars and bad things because of too many emissions, so we should build fewer roads. While there is something to that, we have yet to have other alternatives to getting around. So, trying to figure out balancing reality with our goals is part of the ongoing challenge of the business. Other industries must deal with a little grayer reality where you can change things on the fly, revise your software, or change your spreadsheet assumptions. But construction is not like that. You get out there and dig a hole in the dirt—it is what it is. Having to deal with real tradeoffs with environmental management is a big deal. We will keep thinking about stewardship of the environment, caring for people, and thinking about how we can make investments so that our work creates a great place for future generations.
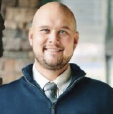
INTERVIEW: TIM ZEGLIN
AUTOMATED EQUIPMENT
Tim Zeglin is the vice president of Frontier Environmental, a general contractor based in Jones Mills, Pennsylvania, that focuses on developing the landscape in Appalachia and is currently running crews in Ohio, West Virginia, and Pennsylvania. Tim discusses how automated equipment will change the industry.
Automated equipment will change the industry from running a conventional best-managed practice in the field to an autonomous fleet that can run according to environmental characteristics. Automated equipment doesn’t need to go home, cut the grass, or leave the jobsite for any reason. The measure we will use with automated equipment is project duration, as we already have safer, lower-cost fleets in practice.
As a horizontal contractor in Appalachia, we are subject to more running water than any other spot in the US. When it rains, our projects are impacted. An autonomous fleet can help when soil conditions are sub-optimal. Autonomous equipment can continue planting, restoring right-of-ways, moving dirt, and excavating bulk materials. Often our jobs run 20 to 22 hours if soil conditions dictate you can remain on the project site. From an autonomous fleet perspective, the equipment is optimized to run in that set of parameters.
You can look at the easiest parts of a project and let the autonomous equipment perform that work. Then employees can focus on the most delicate environmental practices, such as stream crossing. When crossing a stream, you need to focus on the flood plain and the impact on aquatic life that may require a bridge to be built there.
With an autonomous fleet, we’ll see massive changes because the fleet will run on the easiest parts of projects allowing employees to focus on the most challenging part of the project. This also means employees will no longer be able to run the machine beyond its capabilities. Autonomous machines know the parameters it needs to run under. This will help lower operating costs because we won’t see the added expense related to excessive machine usage and out-of-parameter limits.
An autonomous fleet that will run off a digital plan set will be more complete than what our project owners provide us today. We’ll have a set of drawings that can be read or understood by a machine, which can give us a lower overall cost and complete the work faster. Together, the autonomous fleet and digital plans will create an opportunity to complete projects faster, as our current windows of opportunity are minimal. We can see all those things blossom with an autonomous fleet.
CLOSING THOUGHT
Despite supply chain issues and labor shortages, the construction industry has a rosy outlook as many contractors turn to technology to manage their business better and grow their revenues.
About the Author:
David Redd is the content manager with HCSS, the trusted leader in construction software for estimating, field entry, project management, safety, digital plans, fleet management, and telematics. For more, visit www.hcss.com.
Modern Contractor Solutions, January 2023
Did you enjoy this article?
Subscribe to the FREE Digital Edition of Modern Contractor Solutions magazine.
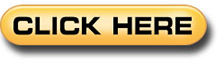