PART 2: Lessons learned using insulating concrete form construction
In the previous issue, a contractor began their first Insulating Concrete Forms (ICF) construction project, and learned some important details about working with the ICF system.
WEIGHTY CONCERNS
Samer Chaya, vice president of Royalton Homes, found out that if there are going to be problems on an ICF project, they’ll happen during concrete pouring. Most of them can be avoided by proper preparation.
While building the foundation (using the thinner conventional blocks), they had to cut away one side of a block to allow room for a column. With no cross-webs, the opposite slab of EPS wasn’t braced by anything, and during pouring, it bulged out under the weight of concrete. They braced it quickly before it could blow out and leak.
Chaya found that the thicker R-30 block that they used above grade are much sturdier and less susceptible to blow-outs. He also found them easier to assemble straight and plumb than the conventional-thickness block. There is more mating surface on the tops and bottoms of the wider block, so it’s easier to align them.
As a rule of thumb, modified ICF blocks usually needed additional bracing. Openings, such as windows, needed extra horizontal and vertical bracing to handle the weight of wet concrete, and in-plane plywood braces to support blocks that were cut to make vertical edges. After concrete hardens, it’s self-supporting.
The entire block wall gets supported with temporary tall braces placed on the interior side. The wall is built plumb, but, Chaya was surprised to learn, just prior to pouring concrete, it gets leaned slightly inwards towards the braces, perhaps a ½-inch. This deliberate leaning, which can be controlled by adjusting the jack-screw on the brace, is done to prevent accidental leaning. If the wall started to lean while being loaded with wet concrete, it might lean the wrong way, away from the brace, and get out of control.
While the concrete is still wet, the jack-screws are adjusted to plumb the wall. The best way to align it, Chaya notes, is to have a horizontal stringline across the top of the wall. While adjusting the jack-screws, sight downwards across the line to see when the top wall-edge meets the string. “You can’t use a bubble level because there can still be waves in the wall. The string works much better.”
BRACING SUPPORT
Royalton encountered another challenge because of inexperience, having to do with the height of the braces. “We built the ICF block 12 feet high, because our floor is at the 12-foot level.” It turned out the only braces available in their region were 10 feet high.
“We were too inexperienced to know we needed the full height braces. We had 2 feet of foam at the top that was not supported. We came up with a solution, but it didn’t work.” They made a horizontal brace out of two 2×4’s nailed into a running T, and placed it along the top of the ICF wall. “When we poured, the form separated from the 2x4s, and we had to run around pulling the wall back in. It was almost impossible.”
The wet concrete must be vibrated for complete distribution around the rebar and into the corners. If vibration is too intense, though, the mass of the moving concrete can rupture some ICF’s. Chaya’s crew acquired the recommended vibrator, but found that they couldn’t run it as long as they had been told. The trick he discovered was to vibrate in short bursts, 5 seconds or less. “Turn it on, turn it off, move it a little, turn it on and off again.”
ICF construction took only 2 months in all, with a break of about 2 weeks in the middle while they built the mezzanine floor. Winter slowed completion of the building, but by spring, they had stucco’d the exterior (directly onto the ICF’s) and were finishing the interior (screwing drywall directly into the web-ends).
THE BENEFITS
As a contractor, Chaya liked that ICF construction meant no framing to build, no sheathing, no insulation to install in the wall, no poly vapor barrier. (The cast-in-place concrete walls are very airtight.)
He is impressed by the noise reduction achieved by the system, too. “Our building is right next to a four-lane highway. When we were doing construction, we couldn’t even hear each other speak because of traffic noise. Now, inside the building, I hear nothing. We upgraded windows to sound-proof windows, and it’s quiet.”
“Now that we are experienced, the second ICF job will be easier. We’ve actually started planning it. You need a few more people on the job, but it is faster once you learn the system. If you’re doing stick framing, you have to hire a carpenter. [With ICF] you can put it together easily yourself. We did it in-house with our guys and saved money.”
As an owner, he adds, “I like that it’s a solid concrete wall; that building will last forever.” ■
About The Author:
Steven H. Miller is an award-winning writer and photographer, and a marketing consultant specializing in issues of the construction industry. He can be reached at steve@metaphorce.com.
_________________________________________________________________________
Modern Contractor Solutions, May 2013
Did you enjoy this article?
Subscribe to the FREE Digital Edition of Modern Contractor Solutions magazine.
Take it from me…
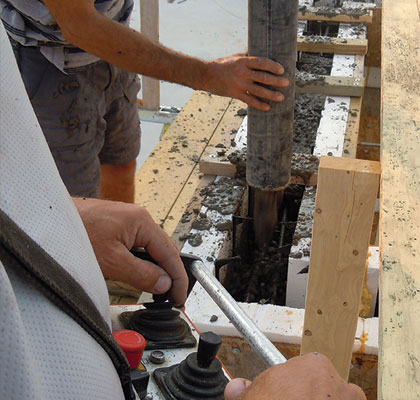