I’ve been around construction for more than 25 years. I’m particularly familiar with moving big RORO (roll-on/roll-off) equipment, I even drove for a while, and have a practical understanding of what it’s like to be in the field and faced with trying to load equipment onto a trailer that’s not well suited to the task.
I bring that prior experience to my job at Alta Equipment Company, which operates one of the largest integrated equipment dealership platforms in the U.S. I’m deeply involved in spec’ing our equipment and because of my background, I specialize in trailers.
BEYOND THE BLUEPRINT
Over the years, I’ve gone around and around with some trailer OEMs and have often been less than satisfied with their willingness to build the specific type of boxes I need. They are often very resistant to modifying existing trailer designs or make significant customization.
About nine years ago, I came across a trailer manufacturer with a vastly different attitude about customization. Not only were they willing to entertain design modifications but were enthusiastic about creating uniquely configured trailers purpose-designed to solve problems. Pratt Industries is an OEM trailer manufacturer located in southwest Michigan. The company has been building trailers since 1974. In this article, I’m going to review three projects that I think highlight the kinds of success stories that are possible when knowledgeable professionals collaborate to troubleshoot, brainstorm, and creatively resolve real-world equipment hauling issues.
60-TON DROP AXLE TRAILER
I had a customer with a fleet of 45-metric-ton excavators with short sticks and big buckets. No matter what we tried, we couldn’t fit them into the knuckle trough and get their stick height down. Not only was this causing the customer to pay more in permit costs for the excess height, but they were also having to remove the bucket and haul it separately, so they were hauling two loads with each deployment.

I took this problem to Clarence Schubach, senior engineer at Pratt, which resulted in an innovative trailer design. Clarence came up with the creative idea of using a unique drop axle, also called a yacht axle, because it’s often used for hauling large boats. The axle drops down about 9 inches in its center.
In addition, Clarence repositioned the axles and made other space-saving structural modifications, from recessing the deck to reengineering the crossmembers. The resulting trailer configuration allowed us to fold that entire boom down into the rear bridge, above the wheels.
The novel trailer design enabled the fleet to reduce its stick height from approximately 15 feet to about 13 feet and 6 inches. Not only did they save on the reduced height permitting, but they no longer had to remove the bucket for transport. Now they could haul their big excavators in just one trip.
SPECIALIZED 60-TON RAISED CENTER TRAILER
Most trailer manufacturers build a raised-center trailer that’s about 48 inches from outside to outside of the center beams. So, anything that has a narrower profile carriage or has a smaller space between its tracks, such as a compact dozer, can have a problem clearing the beams. This results in a lot of raised center trailers hauling small equipment with one set of tracks up on one of the center beams and the other set down on the deck.
I brought this problem to Pratt, and they again had a great solution. They capped their center beams at 40 inches outside to outside, because all the baby dozers like a CAT D3 or a Komatsu D31 have 42-inch spaces between their tracks. This design allowed small equipment to straddle the beams and keep their tracks on the flat deck during transport.
This brings us to the knuckle-trough issue. The area between the two center beams is where the knuckle comes down when an excavator is folded into its transport position. Most manufacturers will close that opening to 20 inches or less. Unfortunately, for big equipment, you need at least 27.5 inches. Pratt specially engineered beams that would flair out in the rear, at about the last four feet of the deck, so you could fit the big knuckles down in between the beams.
The resulting specialized 60-ton raised center is an amazingly versatile trailer that can accommodate almost anything. It allows users to haul everything from a baby dozer to a big excavator, like a CAT 349F.
HYDRAULIC DETACHABLE NECK TRAILER
The standard profile of most detachable neck trailers is somewhat pronounced, so you can’t get equipment close to the neck, because it won’t clear it. Once equipment is loaded, there is also a problem with hydraulic lifting power.
I’ve seen situations where operators had to reposition excavators in multiple different ways to make them fit. I’ve also seen situations where nothing does the trick.
In response, Pratt developed a low-profile, seven-position, all-terrain ratchet neck. The neck enables equipment to be positioned far forward without interference. Pratt also engineered the trailer with four powerful hydraulic cylinders at a slight incline to maximize their physical lifting force.
The result is a highly functional trailer that is easy to load and won’t let you down once it’s laden with even the biggest equipment.
FINAL THOUGHTS
Essentially, I have found that the people at Pratt love a challenge, but I see these qualities less and less in today’s world. Finding the right trailer manufacturer that’s willing to listen, collaborate, and solve customer problems, is worth it when it comes to moving yellow iron.
About the Author:
Ben Berard brings over 25 years of seasoned expertise in the heavy equipment industry to his role as Inventory Manager at ALTA Equipment Company. With a background that spans hands-on experience in the yards of major heavy equipment dealerships to managing trucking and trailer operations, Berard’s comprehensive knowledge of the sector is exceptional.
Modern Contractor Solutions, March 2024
Did you enjoy this article?
Subscribe to the FREE Digital Edition of Modern Contractor Solutions magazine.
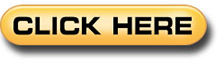