Suspended access solutions benefit World Trade Center Towers
At 1,776 feet tall, the One World Trade Center stands for resilience and enduring spirit. It’s the tallest building in the Western Hemisphere, co-developed by The Port Authority of New York and New Jersey and The Durst Organization. The 104-story skyscraper features 3 million square feet of office space on 71 office floors, a grand public lobby, and an observation deck with spectacular views. It’s the lead building in the WTC complex in lower Manhattan that occupies the location of the original 6 World Trade Center building. The new tower was designed as a glass structure to reflect the sky.
The contractor, Benton Industries, was responsible for glass curtain wall and glazing installation, glass repairs, and louver work on One World Trade Center and Tower Four. More than 3,000 large, delicate glass panels needed to be safely and efficiently lifted to extreme heights—floor 100 and above. The project took more than 4 months and reliable equipment was needed for accurate placement and worker safety.
PRECISE POSITIONING
Spider, a division of SafeWorks, LLC, provided suspended scaffolding and material hoisting solutions for the glass curtain wall and glazing installation on two towers of the World Trade Center: One World Trade Center and Tower Four.
Spider supplied Portland-based glazing contractor Benson Industries with twelve complete swing stages to access the towers’ facades. Standard 20-foot and 30-foot modular platforms, powered by Spider’s SC1000 traction hoists, as well as Modulo® platforms, enabled access to hard-to-reach areas. A custom modular outrigger beam monorail system was specially engineered to support the platforms.
In addition, four Beta Max Leo XXL VFD material hoists were used to lift more than 3,000 massive glass panels into position. With hoists on each side of the building, installers carefully brought the large, delicate panels up at a rate of 40 to 80 feet per minute and precisely positioned each panel for install.
Spider’s New York Operation Center, led by operations manager Joe Simone and district sales representative Marc Frato, provided on-site, hands-on training to ensure safe operation of the equipment.
“The reliability and flexibility of Spider’s equipment were essential for us to complete the upper portion of the project,” adds Danny O’Brien, field superintendent with Benson Industries. “Their New York team provided great service, on-time deliveries, and helpful technical support to ensure that we were working safely at height, staying on schedule, and maximizing productivity.”
The reliability and flexibility of Spider’s equipment were essential for us to complete the upper portion of the project.Their New York team provided great service, on-time deliveries, and helpful technical support to ensure that we were working safely at height, staying on schedule, and maximizing productivity.
Danny O’Brien | Field Superintendant, Benson Industries
[clear]
TAKING DESIGN TO THE NEXT LEVEL
According to the description of the project taken from Benson’s website:
The tower’s structure was designed around a strong, redundant steel frame, consisting of beams and columns. Paired with a concrete-core shear wall, the redundant steel frame lends substantial rigidity and redundancy to the overall building structure while providing column-free interior spans for maximum flexibility. The architecture consists of eight isosceles triangles forming an elongated square antiprism. At the 20th floor, inward sloping exterior walls spring from the corners of the square podium. The sloping sides increase to ultimately converge at the top of the tower in another square turned 45 degrees from the podium.
The project’s unique architectural features commanded inventive solutions. A tower crane was required to lift some of the initial curtainwall corner units. These units were assembled into mega-frames due to the complicated joinery of the converging stainless steel panels and trapezoidal glass units adjacent to them. Every other lite of glass around the 20th floor was left out of the curtainwall frames to provide access for installation of the podium. These were all field-glazed and employed the use of swing staging. The trapezoid-shaped glass lites at each corner panel extend 10 inches beyond the mullions to “float” in front of the stainless steel corners and soften the building edge. Three mechanical plenums are faced with fully louvered walls.
The anchorage was designed for blast resistance using a system of high strength anchors and reinforced glass components. A wide variety of wind loads were accommodated, requiring five different thicknesses of glass ranging from 13/8 inch to 127/32 inch. A reglazing system was designed with 4-sided structural silicone to ensure that each piece of glass could be replaced. Window washing components were included on every vertical mullion to allow the swing stage to be redirected when converging slopes intersect. Trapezoidal units incorporated a custom mecho-shade track guide into the back of the mullions, tapering at a precise 3.72 degree bias. Bright annealed, Top Pearl finished stainless steel panels cover each corner. They are continually reinforce and individually removable.
The One World Trade Center project required extensive quality control, flawless communication, and forward-thinking problem solving. Showcasing brilliant innovation for a modern take on skyscraper design, the One World Trade Center reflects more than just the sky.
■ ■ ■
[divider]
For More InformationSpider, a division of SafeWorks, is a manufacturer and distributor of access and safety solutions in North America, from baskets, traction hoist and platform rental, to safety and training, to specialty-engineered products. For more information, call 877.774.3370, or visit www.spiderstaging.com. For more projects by Benson Industries, visit www.bensonglobal.com.
Modern Contractor Solutions, June 2014
Did you enjoy this article?
Subscribe to the FREE Digital Edition of Modern Contractor Solutions Magazine!
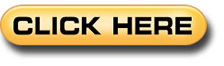