In the construction industry, hydraulic processes are essential to efficiently prepare the site in myriad ways. Excavators use a hydraulic bucket to dig, demolish, lift, or dredge. Versatile backhoes with a front-loading bucket can be used to excavate trenches and lift or unload materials. Bulldozers move and remove soil with a hydraulically raised or lowered heavy metal front blade. A wide variety of other equipment from loaders, graders, pavers, scrapers, and compactors to dump trucks, tower cranes, and pile driving equipment also relies on hydraulic equipment. Essentially, Hydraulic Power Units (HPUs) provide the “muscle” behind all this operating machinery.
However, frequent exposure to moisture splashed from the construction site and roadways as well as weather, washdowns, humidity, and other corrosion-causing factors can wreak havoc on the hydraulic component parts.
For decades, there has been little variation in the basic component configuration of HPUs, which convert electrical power to hydraulic energy. Highly complex hydraulic systems consist of many components including manifolds, directional valves, and the system’s motor and pump, which are mounted to the top of the oil reservoir. Additional components such as filters, pressure gauges, and heat exchangers may also be needed to meet application requirements.
IMPROVE RELIABILTIY
While the design is technically sufficient, OEMs have long sought ways to improve the overall reliability of hydraulic systems that must operate in inhospitable, moisture-prone environments.
One challenge is that high-value components like the motor and pump are also the most likely to require repair or replacement in many cases. Yet current HPU design involves mounting the motor and pump to the reservoir, which exposes the components to the environment and potential corrosion damage.
Even if the HPU is in a toolbox with the vehicle battery, it is regularly exposed to moisture from various sources. Accelerated corrosion only leads to premature service, repair, and replacement.
REDUCING DOWNTIME
Since critical equipment and machinery cannot function without a sound hydraulic system, downtime and lost revenue can result as well. When this occurs, OEMs receive service calls and complaints from customers that are having problems with the unit.
In the industry, maintaining the construction schedule is crucial to help the entire project stay on track and on budget. Any heavy equipment downtime due to the unplanned breakdown of hydraulics can be extremely costly if it delays the project or leads to unused manpower and late penalties.
In addition, while not a concern in all applications, smaller, more compact HPUs are generally preferred where space is limited.
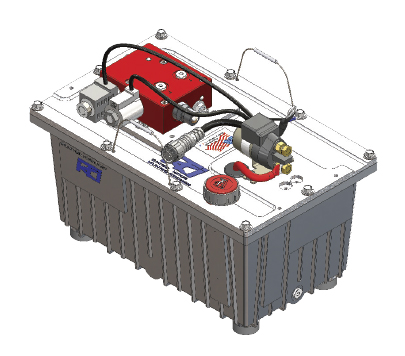
INNOVATIVE REDESIGN
To significantly increase HPU reliability and provide greater design flexibility, a leading hydraulic parts manufacturer, KTI Hydraulics Inc., redesigned these vital components to create the industry’s first “Submerged DC HPU.” Founded in 1998, the Santa Ana, California-based company provides Hydraulic Power Units and components for use in commercial and industrial hydraulic equipment.
In the patented design, the motor and gear pump are protectively submerged in the reservoir fluid, rather than the typical configuration of mounting the motor/gear pump and manifold to the top of the reservoir.
Protecting the motor and gear pump in this manner has many benefits. When the motor and gear pump are submerged, the high-value parts require substantially less maintenance and replacement. The new units are particularly ideal for equipment and machinery operated in harsh, corrosive environments. The oil also functions as coolant, resulting in a longer duty cycle.
KTI Hydraulics Inc. offers the Submerged HPU with a 1.8 KW 12V and 24V DC motor with superior ingress protection (IP) ratings (a measure of an enclosure’s resistance to dust or liquid intrusion). The HPU includes a pressure-loaded gear pump, potted solenoid, and a reservoir with 5 quarts of usable volume. Several optional add-ons are available as well.
The new, innovative HPU configuration also enables a more compact design (15 1/2” x 9 1/2” x 8”), which is ideal for OEMs looking to minimize the space required for hydraulic components.
To provide more flexibility in design for OEMs, the Submerged HPU is offered with a variety of common hydraulic circuits. Custom circuits can be designed upon request. This configurable approach allows for one base unit to utilize multiple circuits.
The Submerged HPU allows the OEM to change the manifold to work with a multitude of different standard or custom circuits. This contrasts with current HPU designs that lock the OEM into either a single-acting or double-acting configuration.
For hydraulic equipment distributors, the capability eliminates the need to stock four different types of HPUs, conserving inventory space and capital. With the submerged HPU, the distributor can purchase a single SKU item to hold in inventory and then the needed manifolds.
CLOSING THOUGHT
Given the critical importance of Hydraulic Power Units in the construction industry, Submerged HPUs are bound to appeal to equipment OEMs experiencing excessive service calls. By ensuring the motor and gear pump are protected within the oil reservoir from wet, corrosive environments, the result will be fewer repairs, greater equipment reliability, and more on-time project completion.
For More Information:
For more, visit ktihydraulicsinc.com.
Modern Contractor Solutions, September 2023
Did you enjoy this article?
Subscribe to the FREE Digital Edition of Modern Contractor Solutions magazine.
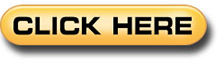