Restoring beauty to the tallest high-rise condominium
Located in Marco Island, Florida, the Veracruz of Cape Marco is the tallest high-rise condominium complex in the world-renowned Cape Marco community. Spanning 24 floors, it boasts panoramic views of the Gulf of Mexico and is surrounded by 30 acres of beautifully landscaped beachfront grounds. However, trouble in paradise was becoming apparent as the humid climate of the oasis complex was beginning to take its toll. The building’s exterior stucco façade was in a state of cracking and disrepair.
STUCCO DETERIORATION
Given the extreme heat conditions and Florida’s coastal environment, rarely does a building go beyond 25 years without requiring advanced restoration. Built in 2005, the Veracruz was on a fast-track of restoration needs as the climate’s high humidity and moisture quickly began deteriorating the concrete structure’s stucco façade. The ensuing breakdown of the bond between the stucco and backup material was resulting in severe stucco damage throughout the complex’s vast 24-floor span. This could result in costly infrastructure repair, as well as potentially dangerous loose stucco.
The Veracruz Condominium Association had planned to paint the entire complex so they asked Delta Engineering & Inspection, Inc. of Sarasota, Florida, to first evaluate the condition of cracks in the building’s exterior stucco. According to Dan Reed, Delta Engineering’s senior project manager, “The initial repaint of a building is usually the first opportunity to assess the condition of a building’s stucco façade. This allows us to design repairs before further damage occurs.”
To avoid the costly and time-consuming replacement and reinstallation of the damaged stucco, Delta enlisted leading industrial masonry repair reinforcement system manufacturer Helifix, Inc. of Streetsboro, Ohio, to implement its precision engineered StuccoPin system.
STREAMLINED STABILIZATION
The StuccoPin system leverages a special short version of Helifix’s patented, slim profile, precision engineered Dry Fix helical tie (stainless steel; grade 304 or 316). The drawn stainless steel manufacturing process that creates the helical hi-fin design more than doubles the proof stress. With its relatively small diameter, the system provides substantial tensile properties to the stucco and concrete.
Notably, the system effectively stabilizes damaged stucco without tearing off and rerendering or chemical anchoring with large pins. Quick, economical and easy to install, StuccoPin also accommodates differential movement and resists wind loads and ground vibrations all while providing a clean finish with minimal visual impact. This is vital to maintaining the luxurious ambience of the Veracruz high-rise complex’s exterior façade.
PULL-TESTING AND INSTALLATION
Before restoration began in the spring of 2012, “pull tests” were conducted on the building’s existing stucco and substrates. These tests were vital in determining the most efficient use of Helifix’s 8mm StuccoPin anchors for optimal strength.
Testing was performed on the second floor at the northeast corner of the Veracruz complex on both the stucco and the concrete alone. The tests were done completely perpendicular to the wall in the area showing the most cracking. A pilot hole was drilled through the stucco and into the backup using a rotary percussion 3-jaw-chuck drill. The StuccoPin was then driven into the stucco using the StuccoPin Power Driver Attachment (PDA 0802) fitted to a SDS rotary hammer drill (650w/700w).
Helifix also recommended that the ties be installed at a 45-degree downward angle. This was essential to increase the surface area of the helical tie embedded in the stucco, thus increasing the pull-out capacity of the pin from the stucco. The results of the testing averaged a significant pull out value.
With the positive pull test data approved and the guidance of Helifix on-site, installation procedures were initiated by Complete General Contractors (CGC) of Sarasota, Florida. CGC western sales manager, Josh, Senevey, states, “This is the largest project we’ve used Helifix’s StuccoPin system on, so the pull tests were vital to ensure the system would provide superior hold for the Veracruz high-rise complex.”
CONCLUSION
Senevey also notes that the initial installation on eight key “drop points” (designated areas of weakness) on the building’s first few floors went seamlessly. “We used approximately 800 StuccoPins and all debonded areas were pinned. The pinning extended at least 2 feet outside the affected areas for strength. Installation is as simple as drilling the pilot hole, driving the tie in, and caulking over the hole. This saves a substantial amount of time versus entirely removing the stucco and replacing it.”
With the effective use of Helifix’s concealed, non-disruptive StuccoPin system, the completion of the restoration of the Veracruz of Cape Marco finished right on target in fall of 2012. ■
About The Author:
Brian Barnes is the vice president of sales with Helifix. For more information, call 888.992.9989, or visit www.helifix.com.
_________________________________________________________________________
Modern Contractor Solutions, April 2013
Did you enjoy this article?
Subscribe to the FREE Digital Edition of Modern Contractor Solutions magazine.
Structural Resolution
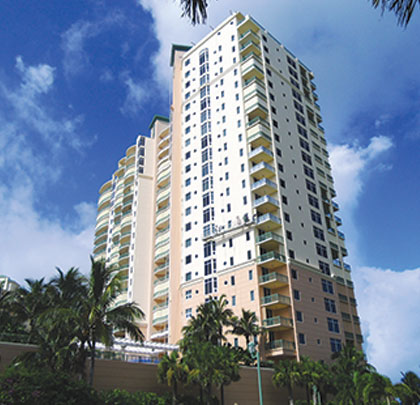