Since the beginning, builders have faced a dual goal of improving performance, while also improving the bottom line. More recently, though, the desirability of “green” building has come to the forefront. For builders who wish to reach all of these objectives, metal offers numerous reasons for consideration. From recyclability to durability, and less obvious qualities, such as the benefits that come from metal coatings, steel demonstrates that minimizing environmental impacts go hand in hand with maximizing the bottom line.
RECYCLABILITY
Steel is the most recycled building material in the world, and because recycling metal products uses 75 percent less energy than processing them from new materials, it offers an attractive solution for builders who have sustainability in mind. The green building movement can be credited with increasing awareness of steel’s recyclability and reusability, which has helped conserve natural resources and reduce environmental damage for decades. In fact, panels from a metal building can often be completely reused, as is, on a similar building. This saves an entire piece of steel from being remade, while simultaneously keeping waste out of landfills.
LASTS A LIFETIME
Building owners need to think long term when deciding on construction materials. Metal buildings are extremely durable; in fact, most are constructed with a 60-plus-year life in mind. Because they last longer, they do not have to be maintained or replaced as often, reducing waste, labor costs, and adverse environmental effects. Additionally, they are resistant to fire, wind, and pest damage, saving money on repairs throughout the life of the building. Replacing building components should be considered in a similar way. For example, if a traditional roof has a 20-year life, and the owner plans to have the building for 60 years, two re-roofs should be factored into the lifecycle cost and environmental impact. A metal roof, however, would likely not need to be replaced at all.
IT GOES FURTHER
Forty tons of steel and 40 tons of concrete are equal on a scale, but typically, steel goes much further in terms of building square footage. Steel mills have very precise control over product thickness, allowing the manufacturer to provide the least weight panel or member needed to meet the project engineering requirements. This has the direct benefit of minimizing the environmental impact, which is directly proportional to mass, as well as indirect benefits, such as reduced travel impacts.
PRE-FABRICATION
Another benefit to building with metal is the fact that many of the building components can be pre-fabricated in a factory setting, a step that brings additional eco-friendly benefits. Processes that produce emissions like cutting, welding and painting are more easily managed in a factory than in the field. For example, by applying coatings in a controlled space, manufacturers can very closely monitor application parameters and keep all chemicals and emissions confined within the factory walls to allow for proper capture and disposal of VOCs. This process allows for excellent quality control and results in a very durable, long-lasting paint system that would not only be hard to duplicate on the jobsite, but also would create undesirable emissions to the environment if applied outdoors.
Another advantage to these metal coatings is the ability to change the properties of the paint to maximize the energy performance of the building. For structures in a hot climate, a cool roof, in a light, reflective color could save a large amount on cooling costs throughout the year. Conversely, a dark roof color would save heating costs in a colder climate. It’s not just black and white, either: There are hundreds of shades available for roof coatings, and where possible, an engineer should be part of the selection process to make sure builders choose the most efficient option.
AT THE END OF THE DAY
Although steel is likely to be the more sustainable option for most buildings, it won’t always be the best choice for every scenario. What’s most important is that builders choose materials that fit their project, first and foremost. The function of the building should always drive the material used. To achieve the best outcome, builders should first develop a list of potential materials that fit the needs of the building, then consider different design scenarios with those materials, and finally choose the one with the least amount of environmental impact.
The most accurate way to measure the sustainability of any material, including that of prefabricated steel, is to use a Life Cycle Assessment (LCA) during the design phase. This assessment evaluates the environmental impacts of a product’s raw material procurement, manufacture, delivery, deployment, use, deconstruction, recyclability, and disposal. LCA allows professionals to look at a building’s impact as a whole and make an educated decision on what works best for the building at hand. ■
About The Author:
Bob Zabcik is NCI Building Systems’ director of research and development. He is a LEED-accredited professional and a registered professional engineer with more than 20 years of experience. He serves on several professional committees, such as the MBMA Energy Committee and Sustainability Committee, as well as several task groups of those committees. He is also on the board of the Cool Metal Roofing Coalition and serves as the director of their technical committee. To learn more about NCI Building Systems, visit www.ncilp.com, or to contact Bob: bobz@ncigroup.com.
_________________________________________________________________________
Modern Contractor Solutions, December 2013
Did you enjoy this article?
Subscribe to the FREE Digital Edition of Modern Contractor Solutions magazine.
Steel Yourself
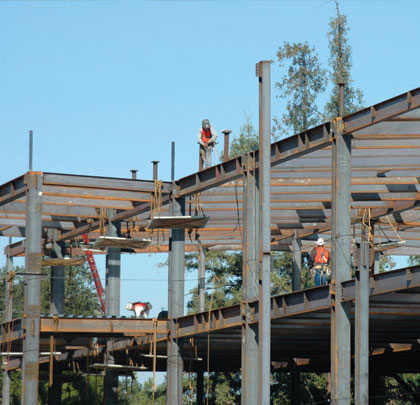