Problems and why they matter
By Stefan Eshleman
Batteries can be monitored for many different things. None of these different things are as important as the foundational measurement of: State of Charge (SoC). Knowing how much charge is remaining in a machine battery pack and what can be done with it is an enabling piece of information that can drastically improve machine/operator efficiencies and increase operator satisfaction with Mobile Elevated Work Platforms (MEWPs).
FLA BATTERIES
The Flooded Lead Acid (FLA) battery was developed more than 100 years ago and coupled with on-board chargers has given the access industry mobility for decades. The batteries and chargers of today are drastically more robust and reliable than those of the past and are designed specifically to work together for optimum reliability and efficiency. Charger suppliers commonly work directly with battery manufacturers to ensure their charging algorithms optimize battery performance and life.
FLA batteries are well suited for the access industry for several reasons. They don’t require expensive and complicated battery management systems; they work over a vast temperature range and are durable and forgiving of misuse/abuse. However, there are still problems encountered with battery performance that can occur. Many of these issues highlighted in this article can be minimized by understanding correct care and maintenance of the batteries and the common issues encountered in the field.
COMMON SERVICE CALLS
Many times, service calls are the result of a lack of charge. Often an operator will plug a machine in overnight and the next day the battery dies shortly into the morning. This commonly happens from charging with long extension cords or small generators, neither of which can supply enough power to enable charging.
When this happens, a customer may call the rental company to dispatch a service tech. The service tech may swap out the charger and have the operator leave it plugged in for the rest of the workday, only to find out the next day that the machine still isn’t charged. Then, eventually it is determined that not enough power is being supplied to activate the machine’s on-board charger.
The major disadvantage of this situation is that the batteries are swapped out simply because they are dead only to find out later the root of the issue was a misuse in charging. As a result, the operator loses time, there is cost associated to the machine owner through service tech time, and a day of lost rental. These situations can be avoided by ensuring power inputs are correct and giving machine owners information on proper charging practices.
PREVENTIVE MAINTENANCE
Today, batteries are viewed as an expensive wear item. Batteries, like other machine components, will eventually need to be replaced. When they need to be replaced is largely determined by how they generate electricity. The internal chemicals will deteriorate or plates short to one another which cannot be prevented, but it can be prolonged.
One of the simplest ways to help prolong battery life is to simply keep batteries over an 80 percent SoC. This drastically reduces sulfation of the lead plates therefore keeping batteries performing at a higher level for a longer period. Many machines fall subject to being opportunity charged. Opportunity charged means that the machines are completely discharged, and then are only recharged enough to move the machine. This is detrimental to battery life.
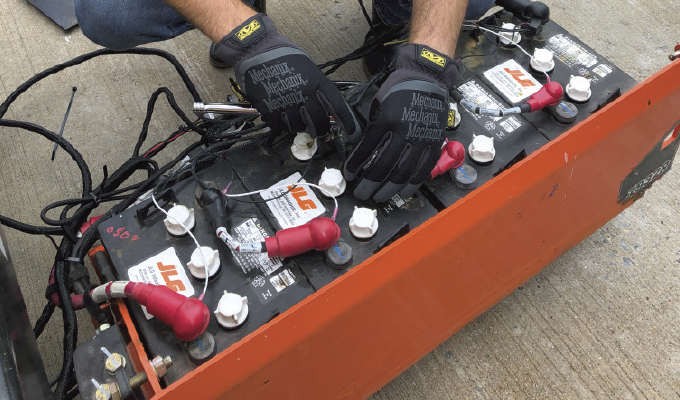
Another known issue of FLA battery is freezing. If a FLA battery is deeply discharged and the temperature gets low enough, the battery will freeze into an ice cube, leading to damage. During battery discharge the sulfuric acid turns into water making it possible to freeze. A battery with a 0 percent charge can therefore freeze at 32 degrees F.
There are several ways to prevent this from happening. The simple answer: When it’s cold, make sure batteries stay charged. Allow machine owners/operators to completely avoid this scenario. This can happen if every battery system is always plugged in while not in use.
Another maintenance task that will help prolong FLA battery life is ensuring that the water level stays above the lead plates. In today’s quick turn world to get machines back out on jobsites, this is commonly overlooked. Low battery fluid level won’t prevent the machine from working and typically the evaporation process is so slow that it just doesn’t merit a cause for concern. When the water level is not above the lead plates, the battery is subject to irreparable damage.
BATTERY POWER ISSUES
It’s not unheard of for machine batteries to run out of charge during the workday. Data shows that close to 65 percent of the time machines are getting charged is between 8:00 a.m. and 11:00 a.m. This is in the middle of the workday for most users causing a huge efficiency problem. This could be prevented by checking a battery SoC or charger status as an end of day report and plugging them in overnight.
The scenario above may not always be the operator’s fault. Today the industry standard for our machines is to rely on a simple voltage table lookup to give SoC indication. This is simple and gives an idea of SoC, but it isn’t accurate throughout the discharge cycle. Operators will experience the battery SoC indicators, most of the time shown in 25 percent increments, switching between charge levels. Then reverting to a higher SoC during times when the machine is not being used and dropping during machine use. Leaving operators to wonder what the “real” SoC of the machine is.
CLOSING THOUGHT
Rental fleet owners should look forward to future advancements in battery management coupled with telematics systems to dramatically increase customer satisfaction while lowering their operating costs.
JLG is taking a comprehensive look at the battery/charger system and will be offering incremental improvements as they become possible, and drastically changing what is and is not possible within the FLA battery world; planning to bridge the gap between what is today and what will be in the future.
About the author
Stefan Eshleman is a senior project engineer at JLG Industries, Inc. He evaluates designs for performance, safety, and reliability. For more, visit www.jlg.com.
Modern Contractor Solutions, October 2019
Did you enjoy this article?
Subscribe to the FREE Digital Edition of Modern Contractor Solutions magazine.
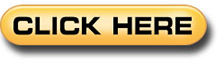