By Tommy Faulkner
Special inspections originated in response to public safety concerns over a series of catastrophic structural failures in the late 1970s and early 1980s. Following high-profile incidents, like the collapse of a pedestrian walkway at the Hyatt Regency Hotel in Kansas City, Missouri, in 1981, the U.S. House of Representatives tasked a subcommittee with examining causes of the failures. The subcommittee reported the need for improved communication on construction projects and recommended the onsite presence of the structural engineer or his designee during construction.
Since then, special inspections have been developed, now known as Chapter 17 of the International Building Code (IBC) and adopted by all 50 states. Special inspections code language addresses requirements for materials, fabrication, and installation, where special expertise is needed via inspection to assure that buildings are constructed according to the design specifications. Requirements are based on such factors as height of the structure, occupancy category, and additional requirements for “high” seismic and “high” wind conditions.
While designed to assure public safety, special inspections are sometimes viewed by late adopters as costly additions to construction projects. However, special inspections requirements have been thoughtfully developed by the ICC code development process to increase the quality of construction and simultaneously reduce overall construction costs. This occurs as a result of the trade-off between higher factors of safety during the design process and these intensive inspections by an inspection agent to evaluate the accuracy of the construction as compared to the design documents. When implemented properly by a qualified team, special inspections add value for all stakeholders in construction projects. Here are three ways special inspections add value to any project:
1. HIRE FOR KNOWLEDGE AND EXPERIENCE
While special inspectors must be thoroughly trained and qualified to serve, a knowledgeable and experienced special inspector provides value far above the mandatory requirements. When hiring special inspectors, identify those who have in-depth knowledge of both the special inspections and design chapters of the building code. With the understanding of both design factors of safety and special inspections requirements, the special inspector can develop a plan that is safe and effective without adding unnecessary burden or cost to the project.
In addition to depth of knowledge of the codes, look for breadth of experience. While inspectors are usually deployed based on their areas of expertise, one with the proper training and experience can manage an entire project. Whether a Master of Special Inspections who is qualified across all materials and service lines, or a Professional Engineer who has been trained intentionally across multiple inspection disciplines, identifying a lead inspector provides continuity in understanding of the design, efficiency in having one person who can manage any concurrent issues onsite, and improved communication across stakeholders throughout the project.
2. FOCUS ON QUALITY
Some project owners are tempted by low-cost special inspections programs, viewing the code as creating unnecessary cost and schedule burdens. However, when the focus is placed on quality, project stakeholders have the assurance that the structure will perform as intended, which more often saves time and money in the long run.
An effective quality assurance (QA) program requires the special inspector to be more than a figurehead on the project; they must be intimately involved and regularly onsite to ensure the quality of construction. By performing in-process inspections as required, the inspector can ensure construction progresses with the specified materials, within tolerances, and with proper installation techniques, benefitting the contractor and project owner by reducing the frequency of callbacks and future maintenance issues. The inspector can proactively manage and reduce the need for field changes, providing assurance to the owner and design team that the structure is constructed, and will thus perform, as designed.
QA programs require a thorough communication plan, including the documentation process and speed with which deficiencies are communicated to the contractor. By adhering to requirements for onsite presence, and communicating with the contractor quickly and effectively, the inspector can recognize deficiencies in-phase, reducing potential rework. Through this collaboration, the inspector and contractor can ensure deficiencies are corrected with limited cost and schedule impacts or safety risks.
3. COMMUNICATE PROACTIVELY
An effective special inspections program cannot be reactive: if communication does not begin until the first deficiency is noted, a significant opportunity is lost. Pre-construction conferences provide a forum for discussing the QA program and addressing potential challenges with the project’s specific materials, fabrication, or installation techniques. Drawing on their knowledge and experience, special inspectors can identify areas of concern and consult on strategies to prevent issues during construction.
In addition to the requirement for a Statement of Special Inspections (SSI) prepared by the design professional in responsible charge, the designer will provide the full road map of the testing and inspections plan. This process allows for all project participants to understand what is required by IBC and/or local codes, the quality requirements set forth by the project owner and the timeline for testing and inspections. By looking ahead, the contractor and special inspector can partner to address potential challenges in advance, rather than waiting for deficiencies. This collaboration will serve to reduce the cost of correcting deficiencies and the resulting schedule impacts.
CLOSING THOUGHT
When properly planned and implemented, special inspections add value to construction projects in areas of schedule, cost, and quality. By hiring special inspectors based on their knowledge and experience, and implementing a plan that focuses on quality and proactive communication, project owners can mitigate cost and risks during construction, and ensure structures perform as designed.
About the author:
Tommy Faulkner, CEO of JDSfaulkner, is a licensed professional engineer, general contractor, Master of Special Inspections and realtor. For more, visit www.jdsfaulkner.com.
Modern Contractor Solutions, November 2020
Did you enjoy this article?
Subscribe to the FREE Digital Edition of Modern Contractor Solutions magazine.
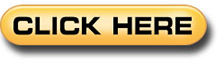