Machine to machine, process to process, result to result. In almost every business or industry, meaningful comparisons and evaluations can make the difference between profit and loss. But all too often in industries that use heavy equipment, asset managers are not able to hold apples up to apples when evaluating fleet performance.
The Association of Equipment Management Professionals (AEMP) is working to improve the situation through a Metrics Initiative that, in the past 22 months, has gained traction among association members.
The goals are to establish consistent and practical fleet performance standards to help asset managers more accurately and consistently monitor fleet performance and profitability. If industry standards can be established, everyone will have a baseline of information on which to compare their fleet with industry benchmarks. If successful, variances, such as soil conditions, terrain, the cost of fuel in specific regions, or any one of dozens of other performance variables, will be considered.
In the process, the new standards will help software developers, manufacturers, distributors, dealers, and others more effectively meet the needs of companies that use heavy equipment.
MOVING A MOUNTAIN
A performance metric is a raw measurement of a business process. Through metrics covering a wide range of assets, costs, and processes, companies are able obtain the data they need to monitor and evaluate performance and, ultimately, make better decisions.
Industries that put heavy equipment to work every day measure hundreds of things, from cost per hour for a piece of machinery to cost per ton, from percentages of mechanics’ billable hours to production per gallon, from run vs. idle time to lifecycle costs.
The problem is that one company seldom measures the same things in the same way as another. And often, when they do measure the same things, they either don’t measure them to the same extent or use a common formula. What means one thing to one company means something entirely different to another.
Take cost per hour as a basic, oversimplified example. Let’s say an asset manager wants to measure the performance of a specific, standard piece of equipment. How many hours should that asset manager factor into the metric? Should it be the hours in a regular 8-hour-per-day workweek, 2,080 hours per year? Should it be based on 24/7 utilization? Or should it be somewhere in between?
Tons per hour is another example. It’s one thing if you’re taking that measurement in Florida, but if you’re in Colorado, where soils are rockier, the results are going to look a whole lot different. Excavation there will take longer and will require more effort. The work is also going to inflict more punishment on the machines, which in turn will impact other metrics like maintenance and lifecycles.
The point is, it’s very difficult for companies that use heavy equipment to benchmark because the data that is being used in developing utilization protocols is completely different between companies, regions of the country, and so on. There are no mutually accepted or consistently applied standards that can help fleet managers see where they are, how they compare, and where they might improve. It gets more complicated still when you factor in thousands of companies in dozens of regions with tens of thousands of ground conditions and nearly infinite equipment combinations.
Clearly, there is a need to develop metrics and industry-accepted standards that can be applied across the board. With them in place, an asset manager will be able see how a company’s fleet benchmarks against the industry as a whole with similar equipment numbers that are in the same region and so on.
We all need to start speaking the same language.
WHO GETS THE MESSAGE
Several groups, not just end users, stand to benefit from everyone agreeing on foundational standards. They are all in the AEMP Equipment Triangle, which represents interrelated partnership between manufacturers and other suppliers, distribution, and fleets.
For example, the productivity test that Manufacturer A currently conducts does not look anything like Manufacturer B’s productivity test, yet end users may want to analyze those products and decide which equipment best suits their needs for a specific job. With industry standards in place, they will be able to make more meaningful comparisons.
In addition, with metrics and standards in place, manufacturers will know exactly what to do to respond to the needs and desires of end users. Take an uptime metric for example. With one in place, the industry will clearly show manufacturers how uptime is measured so they can report how their machines perform based on the metric. The manufacturers can change their designs to better align with those expectations and, by extension, become stronger competitors.
Companies that develop software that heavy-equipment industries use will get a leg up, as well. They’ll know exactly what’s needed in those industries, so it will be easier for them to develop workable programs, with meaningful reports and tools, for tracking and evaluating performance. They’ll also understand what level of flexibility is needed within their products so end users can build in company-specific variances.
Distributors and dealers will gain a better understanding of what industry hot-button issues are so they can more effectively market and support products that reflect those preferences.
From one point of the Equipment Triangle to another, metrics and standards will provide much clearer insight to what industry goals are and what asset managers expect when purchasing, using, and ultimately, disposing of equipment. ■
Look for the conclusion of this article in the next issue.
About The Author:
Stan Orr has been the president and chief strategy officer at the Association for Equipment Management Professionals (AEMP), an international organization based in Glenwood Springs, Colorado, for 14 years. AEMP provides education information and networking opportunities for companies that use heavy equipment and the professionals who manage it. For more information, visit www.AEMP.org.
_________________________________________________________________________
Modern Contractor Solutions, September 2013
Did you enjoy this article?
Subscribe to the FREE Digital Edition of Modern Contractor Solutions magazine.
Speaking the Same Language: Part 1
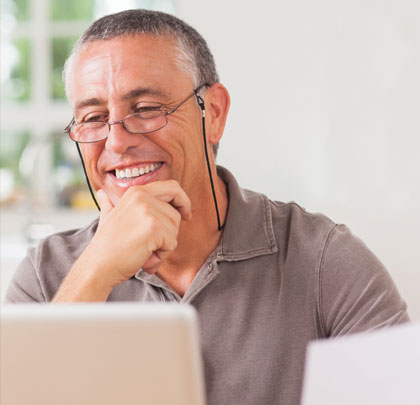