Colorado Milling resurfacing Denver Metro with attention to fueling efficiency
When Chris Vorhies started Colorado Milling, LLC in 2016, he had a vision of executing asphalt milling jobs along the entirety of the front range of the Rocky Mountains. With more than 50 years of experience between himself and his team, Vorhies strove to become a growing force in the redevelopment of roads, highways, parking lots, and asphalt surfaces along the I-25 corridor.
That vision coincided with requisite infrastructure improvements being made in Colorado’s largest city, which is also Colorado Milling’s headquarters: Denver.
The population of Denver, Colorado, has grown by nearly 20 percent since 2010, with Census projections estimating growth to continue at a high rate compared to its peer cities across the United States. That population growth has led to increased traffic, increased wear on roads, and an increased need for investment in the Mile High City’s infrastructure.
That’s where Colorado Milling comes in.
Currently, the company is in the throes of an effort to mill roughly 300,000 square yards of asphalt across the Denver metro area. It’s a massive project for Vorhie’s outfit that often requires two of the company’s five cold milling machines, a pair of skid steer loaders equipped with brush attachments, and wheel loaders for moving asphalt debris. In total, the project requires between 12 and 20 employees that are running full weeks.
“We have at least one mill dedicated to this project that runs 5 days a week until the project is done,” Vorhies says. “It’s a monster project for us. We are moving through the city, milling the streets and parking lots and then a paving crew, which is a separate entity from us, comes in behind us and paves the streets back. It’s the biggest project we’ve ever had.”
BIG PROJECT. MASSIVE FUEL NEEDS.
The city of Denver has a litany of hand-picked asphalt milling projects that Colorado Milling tackles from day to day. Sometimes its multi-day or multi-week road projects, other times it’s a shorter-term parking lot resurfacing job. In each case, the company mills 3 inches from the asphalt’s surface, allowing it to be resurfaced in a sustainable manner that’s most cost-effective for the city and taxpayers.
On a given day, one of Colorado Milling’s mills alone burn between 100 and 200 gallons of diesel every day. Combine that with the fuel being burned by the company’s skid steers, loaders, dump trucks hauling debris off-site, and various other pieces of equipment, and that translates to a need for fueling efficiency.
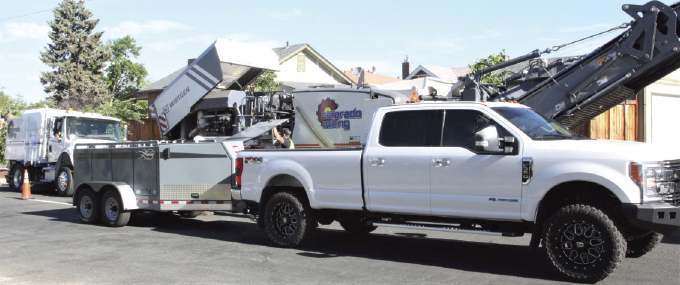
It didn’t take long for Vorhies to identify that he had an opportunity to streamline his operation 18 months ago when he calculated how much fuel he would be burning and how much time it would take to be making fuel runs with a 90-gallon tank in the back of a pickup.
“It would take one guy several hours a day per crew to just run back and forth to the fuel station to fill up the equipment after 8 to 10 hours of operating each day,” Vorhies says. “It was a lot of wasted time and a lot of overtime hours.”
FUELING SOLUTION
It was at that point that Vorhies added to his fleet. He invested in a 920-gallon Thunder Creek Equipment Multi-Tank Trailer to solve his fueling challenges.
The Thunder Creek MTT is designed to transport up to 920 gallons of diesel over-the-road without the need for a HAZMAT authorization and in many cases a commercial driver’s license, saving Vorhies and Colorado Milling the cost of paying a professional driver, which are in short supply, and the additional insurance of a HAZMAT vehicle.
Additionally, Colorado Milling’s MTT is equipped with a 2-in-1, 100-gallon Diesel Exhaust Fluid (DEF) system that both pumps DEF in and out in a closed system, eliminating risk of contamination, which can lead to the degradation of a Tier 4 engine’s Selective Catalytic Reduction (SCR) system. Since the company’s asphalt mills all require DEF, the Thunder Creek MTT has massively reduced the time, hassle, and risk of contamination associated with refilling with 5-gallon plastic totes of DEF like they were previously.
“We can now top the DEF tanks off once a week and it works great,” Vorhies says. “We’re not running around with 5-gallon jugs in the back of our service trucks. That was a pain.
“The Thunder Creek trailer has streamlined everything. Now one vehicle can take care of all the equipment as far as fuel and DEF.”
EQUIPPED FOR GROWTH
While the Denver infrastructure contract is a big step in the company’s growth, Vorhies has an eye towards the future. The company is growing sustainably year-over-year, and much of that is due to the fortuitous regional growth, the public’s willingness to invest in infrastructure improvements, and Colorado Milling’s knack for efficiency.
“With every project we’re always looking at ways to be faster, more efficient, and more effective,” Vorhies says. “And making smart moves and investments is a big part of that, too.”
The Thunder Creek MTT was one of those smart investments, Vorhies says. While it’s not a direct revenue generator, it has given his operation hours of efficiency each day and cut down extensively on overtime pay. The trailer, he expects, will have paid for itself by the end of summer 2019.
Additionally, once the company expands to multiple locations across the metro area, Vorhies expects to add at least one more Thunder Creek MTT.
“When the longest part of the fueling process is filling up the trailer itself, I would say the process is working great,” Vorhies says. “The Thunder Creek has worked beautifully for us.”
For more information
For more information about Thunder Creek’s no HAZMAT bulk diesel and DEF handling solutions, call 866.535.7667, or visit www.thundercreek.com.
Modern Contractor Solutions, July 2019
Did you enjoy this article?
Subscribe to the FREE Digital Edition of Modern Contractor Solutions magazine.
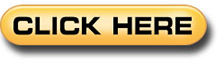