When Hurricane Michael tore the roofs off several buildings at the lumber mill in the Florida Panhandle, a hail of screws was released at the scene which littered the ground for weeks after. As employees scrambled to get the mill back into operation, those screws soon found their way into dozens of tires, notes Randy Bullock of Harris Tire in Ocala, Florida.
“There were 40 or 45 flats the first week they were back in operation,” says Bullock. There was one forklift that escaped the damage, he notes—a large Hyundai outfitted with a set of Galaxy Yardmaster SDS solid tires that were being tested at the mill.
“With the Galaxy solids, they just pulled the screws out and kept on going,” he says.
TOUGHEST OF THE TOUGHEST
The “SDS” in the tire’s name stands for “Severe Duty Solid.” When Ed Flatten, North American sales manager for solid tires for Alliance Tire Americas, Inc. —manufacturer of the Galaxy brand—asked him to put some Galaxy SDSs through their paces, Bullock chose two lumber mills.
Bullock likes to find environments that he calls “the toughest of the toughest” for testing new tires. Testing tires in a decent environment doesn’t tell you what you need to know, he points out.
“We want to try them, in essence, where we’re going to try to make them fail,” he explains.
Two shifts per day, 5 to 6 days per week at the mills, keep the tires grinding constantly on concrete and asphalt. Hazards like broken wood and bits of welding rod can puncture tires and sideline equipment for hours. The long hours also provided Bullock a chance to get feedback on the solid tires’ ride.
“Neither of the operators of the forklifts knew the first month that these were solid tires—we didn’t tell them,” he says. “A lot of people think the solid tire’s going to be a really rough ride. But there’s a three-stage compound in the Galaxy tire so they have a little coosh. The operators never even mentioned the change in the ride.”
Alliance Tire’s Flatten explains that three-stage construction includes a core of cellular compound rubber under the durable tread rubber layer that offers a cushioning effect.
Bullock adds that pneumatic tires on the huge lumber mill forklifts are typically inflated to 130 psi to handle the extremely heavy loads, so “there’s not a lot of give.”
COUNTING THE HOURS
Downtime is extremely expensive in heavy equipment. A machine that costs $100 to $150 an hour to own and operate racks up a lot of losses as it waits for a mechanic to fix a flat tire, Bullock notes, not to mention the wages of the mechanic assigned to do the repair and the cost of the operator sitting idle on the clock.
But the other hours Bullock counts carefully are how long the tires last. After months in the field, the Yardmaster SDSs are showing no sign of wearing out. At a price about equal to the premium pneumatic radials that the mill typically uses on its forklifts, he expects the Galaxy solids to be much more economical to own and operate.
Flatten notes that two forklifts at the mill are projected to need replacement of their pneumatic radials at less than 2,500 hours; Bullock notes that top-tier radials max out at 4,000 to 5,000 under the best of circumstances. Meanwhile, the Yardmaster SDSs are on track to last about 6,000 hours.
“They’re tracking really well,” says Bullock, “so the cost per hour is going to be a lot less.”
It’s not hard to see why the solid tires last so long. Bullock points to the 114/32nds of useable rubber on the solids, which is three times as much as on a typical radial pneumatic tire and well over twice as much depth as on the top brand of pneumatics.
“That’s a lot—a lot—of rubber,” he notes.
IDEAL FOR CONSTRUCTION
Bullock points out that even though he’s chosen a mill in which to test the Galaxy SDSs, the lessons learned there demonstrate the value of solid technology for construction sites and other tough environments.
“In these heavy-duty industrial applications, a solid is the way to go,” he says. “They’re ideal for skid steer type applications, construction. They can be running over nails with no problem. And, the skid steer solids have the R-4 treads for traction, and even aperture holes so you’ve got a little bit of cushion.”
The long-time tire dealer notes that foam-filled pneumatics were popular for tough environments and were immune to flats from punctures, but he adds that slashes on the sidewall cause the foam to ooze out, ruining the tire. That’s a significant risk on construction sites where broken pavement, bent rebar and debris create a significant risk of sidewall damage.
“With a solid tire, it’s made for cutting,” he notes. “It’s designed for abuse.”
That’s exactly what the people whose job includes repairing tires are looking for, says Bullock.
“The guys at the mill, they really want these to work,” he points out. “It’s going to free up the mechanics and the maintenance shop. In the long run, it’s going to save the business a lot of money.
“These solids just go and go and go,” he says.
About the author:
Ryan Lopes is national product manager (Material Handling and Solid Tires) for Alliance Tire Americas, Inc. A strategic marketer with experience across the Alliance Tire Group’s global operations, he was integral to the development and testing of the company’s solids and material handling product line, continually drawing on his degrees in engineering and marketing. Ryan, who has been with ATG for more than 5 years, is based at Alliance Tire Americas’ headquarters in Wakefield, Massachusetts. For more on Alliance Tire and its Galaxy brand of construction and industrial tires, visit www.atgtire.com.
Modern Contractor Solutions, December 2018
Did you enjoy this article?
Subscribe to the FREE Digital Edition of Modern Contractor Solutions magazine.
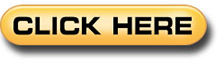