In northern Illinois, U.S. 30 crosses the Rock River just north of the community of Como and less than 5 miles west of the twin cities Rock Falls and Sterling. In 2016, the route’s 1,200-foot-long bridge was rehabilitated, receiving a new finger joint and a latex-modified concrete overlay. Transverse grooving was installed on the overlay’s surface.
“At that time, IDOT didn’t have a departmental policy for diamond grinding overlays on bridge decks,” says Matt Hardt, acting construction engineer, Illinois Department of Transportation District 2. “In 2017, the department enacted a new policy on grinding bridge deck overlays—so if the bridge had been rehabilitated one year later than it was, it would have been diamond ground.”
The policy released in 2017 determined when to perform diamond grinding based upon average daily traffic, length of bridge deck, and posted speed limits.
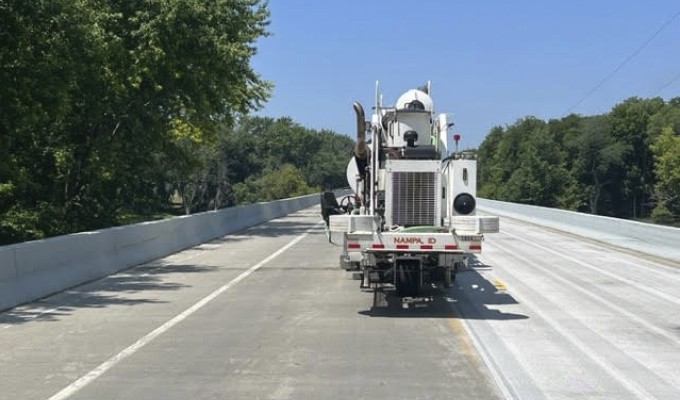
Because it can be difficult to achieve a smooth finish on latex-modified concrete overlays, the final riding surface for the 2016 project was less than ideal. Hardt, who lives near the bridge and had first-hand experience with its rough ride, advocated for diamond grinding the overlay.
“In District 2, we had not historically done a lot of bridge deck grinding after the fact. To go back and grind an existing overlay on a bridge deck was new to the district,” says Hardt.
In July 2023, a grinding project was let, and Quality Saw and Seal successfully performed diamond grinding and longitudinal grooving on the deck.
“This example project goes to show that diamond grinding and grooving can be used on other existing bridge decks that have similar smoothness issues. The process offers IDOT, and other agencies, a cost-effective solution,” says Scott Eilken, Quality Saw and Seal.
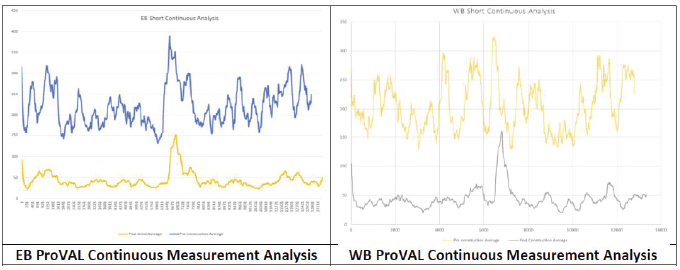
GRINDING IMPROVES SMOOTHNESS
Fixed interval reporting (using a standard input of 528 feet or one-tenth mile) showed that grinding reduced the eastbound roughness from 185 in/mi to 44 in/mi, a 76-percent improvement. The westbound roughness was reduced from 223 in/mi to 46 in/mi, a 79-percent improvement. Continuous short interval reporting (using an input of 25) supported the findings of the fixed interval analysis and indicated that there was a significant reduction in areas of localized roughness. Specifically, eastbound and westbound roughness improvements ranged between 5 and 89 percent and from 15 to 90 percent, respectively. Post grind short interval roughness cumulative distribution plots, again with inputs of 25 feet, showed nearly all sections achieved a 50-percent or greater roughness reduction.
In addition to improving smoothness, the deck is much quieter than before. One factor contributing to noise on the original overlay was its transverse grooving, which causes more road noise than longitudinal grooving. Another factor was the roughness itself; rough pavements are noisier pavements. After diamond grinding and longitudinal grooving, there was a noticeable improvement in tire/pavement noise. Longitudinal grooving has also been shown to reduce wet weather crashes, improving safety.
“Quality Saw and Seal was very pleased that we were able to use the well-established process of diamond grinding and longitudinal grooving—a method that has been proven, by the International Grooving and Grinding Association and others, to improve smoothness. On U.S. 30, we were able to reverse conditions on a very rough existing bridge deck surface that had definite smoothness issues, achieving an improvement of 76 to 79 percent. The motoring public will recognize and be very pleased with such a difference,” says Eilken.
“IDOT strives to provide the public with a quality transportation system that is safe and comfortable,” says John Senger, IDOT bureau chief of research. “Improving the ride quality on bridge encounters goes a long way in helping the agency achieve this goal.”
For More Information:
The International Grooving and Grinding Association (IGGA) is a non-profit trade association committed to the development of the diamond grinding and grooving process for surfaces constructed with portland cement concrete and asphalt. In 1995, the IGGA joined in affiliation with the American Concrete Pavement Association (ACPA) to form what is now referred to as the Concrete Pavement Preservation Partnership (IGGA/ACPA CP3). For more, visit www.igga.net.
Modern Contractor Solutions, May 2024
Did you enjoy this article?
Subscribe to the FREE Digital Edition of Modern Contractor Solutions magazine.
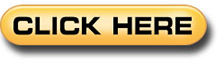