By Dr. David Gress, PE, and Malcolm K. Lim, PE
With the advances in the technology world today, it is inevitable that technology is being introduced into the construction industry. Today, we see the development of elaborate testing equipment ranging from testing machines to sensors. SMART technology is one of these new advancements available to the Concrete Construction Industry. SMART has allowed concrete professionals to make informed decisions resulting in economic benefits and accelerated time schedules. One of the critical features in concrete construction is the curing of the concrete mix after placement. With proper curing, the specified concrete strength can be easily obtained. Knowing the estimated concrete strength allows the engineers and contractor to make better decisions, e.g. when to remove forms for the next phase of construction; concrete maturity, as described by ASTM STANDARD C1074, is certainly one method of obtaining the necessary and viable information to make timely professional decisions.
Traditional concrete curing practices are one of the most critical procedures in construction today. Proper curing is essential as it allows the cement particles to effectively hydrate, resulting in increased concrete strength and durability. It is current practice to make concrete cylinders during concrete placement. These cylinders are left on site to allow the concrete to set. Cylinders are then transported to the laboratory after a short period of time in the field, usually the next day or two. The cylinders are then stripped and immersed in a water bath to continue to cure. In order to obtain the compressive strength of the concrete, the cylinders are removed from the bath, allowed to surface dry, capped, and then tested in a compression machine to determine the compressive strength of the concrete. This procedure is performed as a function of time to determine the strength time relationship.
The current practice does not take into account field curing conditions or the ambient temperature on-site, as a large majority of the curing process occurs in a moisture perfect and temperature-controlled laboratory environment. Additionally, this practice is also very labor-intensive, as the practice is repeated throughout the project and is extremely subject to operator error.
With the onset of SMART technology today, the traditional method of determining the compressive strength in the field can be obtained more accurately and better reflect the concrete strength gain. SMART technology can provide up to date information on strength gain and real-time relative humidity in the concrete.
CONCRETE MATURITY
Concrete maturity is an accepted method whereby the strength information can be obtained without having to wait for the test lab to provide information. The maturity method is fully described in the ASTM STANDARD C1074 and is one of the most useful tools in the industry that allows engineers and contractors to have up to date strength information.
The concrete maturity process, defined by ASTM, starts in the concrete laboratory where measurements of strength as a function of time and the internal temperature of the concrete strength gain over time are correlated with temperature rise within the concrete caused by hydration. The maturity method correlates the rise in concrete strength with temperature and determines a time factor. The end result is the Maturity Index, which identifies the relationship between temperature, time, and strength gain, unique for a given concrete mix. The Maturity index is represented by an equation that can easily be used to control the curing of field concrete. The Maturity Index takes into account the ambient field conditions as the concrete temperature can be taken into account with the equation.
ASTM STANDARD C1074 provides two different methods to obtain the maturity index, the Arrhenius Method and the Nause Saul Method. Both methods can be used to obtain the maturity index. The Maturity Index is mix unique to every different concrete mix. American Concrete Institute offers a certification program related to ASTM STANDARD C1074, in which the technician must demonstrate an understanding of the testing method.
The maturity index, from either method, needs to be derived prior to placement of the mix on site. This is usually done at a test laboratory. Once the maturity index is derived by the testing laboratory, the equation can then be applied to the time/temperature index of the mix.
BENEFITS OF USING CONCRETE MATURITY
The current practice of making concrete cylinders in the field, having a certified laboratory crush the cylinders, and reporting the compressive strength of the concrete, has been done for years. With the onset of SMART sensors, all this information is now available in real-time. The benefits of SMART technology includes:
- Embedded SMART sensors that obtain information from the concrete in the field. The information from the SMART sensor is, therefore, more representative of the ambient conditions of the concrete in the field.
- The SMART Sensors record data at a 30-minute interval, providing a very representative and accurate real-time strength information of the concrete, compared to a data point from a cylinder break.
- The SMART Sensors continuously captures and updates data, allowing decisions to be made based upon projections or trends of the data
- The quick and easy installation methods reduce labor cost associated with concrete strength evaluation
- SMART Sensors are also available to record the relative humidity of the concrete as an asset to assist in the placement of floor coverings.
TYPES OF SYSTEMS OUT ON THE MARKET
There are both wireless and wired sensors available today for the concrete industry. The wireless sensor has the benefit of gathering data within the proximity of the sensor, after which the data can be rapidly uploaded and distributed to the project team. The difference between the wired and wireless sensors are:
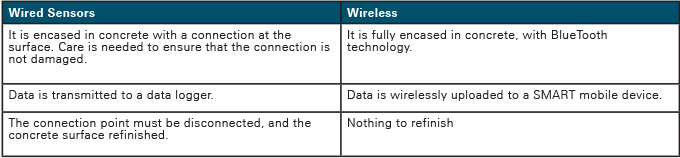
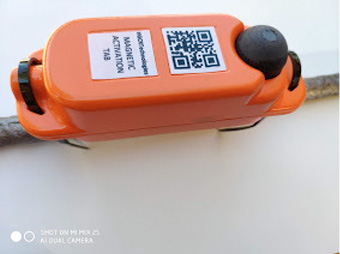
Having utilized both the wired and wireless sensors, the authors recommend the wireless method. The largest advantage of wireless technology is savings in labor costs and having the information available when needed. Once the maturity index is formulated for a given mix, it can be applied to all of the concrete mix placements without any need for traditional and expensive concrete laboratory testing. Additionally, the sensor(s) are app-based to easily allow multiple users to collect and distribute essential data. The sensor collects data every thirty minutes and enables the user to estimate the concrete compressive strength based on either of the maturity methods described in ASTM STANDARD C1074.
Additional benefits to using an instrument, such as the VAKKA, is the added ability to record the concrete parameters and monitor these parameters at different locations within the structure. The VAKKA also has a 10 ft lead, which can be positioned at different points within the structure.
Flooring contractors can be assured the moisture level is consistent with their particular flooring application needs. Internal temperature, as in massive placements, can easily be monitored to ensure the temperature does not exceed the design threshold.
AUTHORS’ EXPERIENCE
The authors installed the wireless sensors into test beams that were cast with very specific strength criteria. The team chose to use the wireless sensors to monitor the gain in strength of the concrete. This allowed for closer monitoring of the strength and allowed the slabs to be utilized over a projected duration or when the concrete compressive strength fell within the specified criteria. The maturity index was initially developed with concrete test cylinders. The test beams were 10 feet long, by 2 feet wide by 15 inches thick. The reinforcing bars were embedded into the test beams. The placement of the sensor was simple. A sensor was incorporated into one test beam for every concrete pour on the top reinforcing bar. The test beams were placed and stored after stripping in a temperature-controlled warehouse where large variation in temperatures was not expected. Achieving the narrow strength range specification was easy to achieved using the sensor.
The past practice was to cast ten test beams at a time. Additionally, a total of thirty concrete cylinders were also made during the concrete placement. The testing protocol called for testing two to four cylinders according to ASTM STANDARD C39[i] each time the test beam was incorporated into the test program. Given that these practices took time and effort, and the added cost of concrete cylinders, the recommendation was to develop the maturity index and use the wireless sensors to help achieve a concrete compressive strength within the narrow required strength range.
The high sampling rate of the sensor allows for monitoring the conditions in the slab. The wireless sensor and associated app provided the required information on a daily basis. The app was a great benefit to the research team as it allowed for closer monitoring of the concrete strength and allowed the team to anticipate when the test beam could be utilized. From the previously derived maturity index, the app also calculates and displays the compressive strength. The temperature profile displayed in the app shows the temperature of the concrete flattening out, indicating the hydration of the cement in the slab. Additional steps to slow the rise in concrete strength gain was not needed.
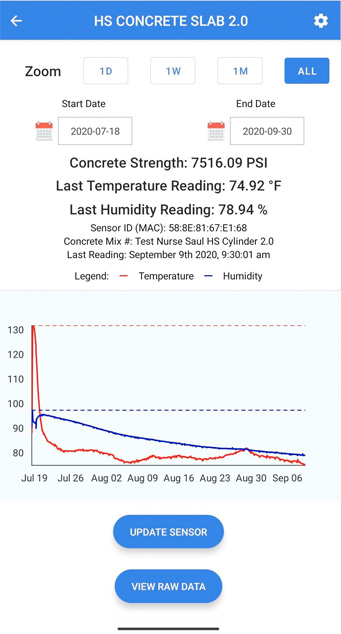
Overall, the reduction in time, effort, and expense of not testing cylinders as well as required validation with cores resulted in a significant cost savings of 70 to 80 percent of the project testing cost over the entire project. The most significant advantage was to be able to upload temperature data from the sensor on an as-needed basis and have the estimated concrete strength available.
OPINION
Incorporating technology has great benefits in that it saves a significant amount of labor cost and eliminates any potential errors that may occur along the way. Many issues have been noted with traditional cylinder testing when mistakes were made (handling cylinders before hardened, dropping cylinders, improper transporting cylinders, recording errors, inaccurate testing equipment, etc.) during cylinder testing. An erroneous data point in any report becomes a legal entry making it a legal document that can be very expensive to correct. With the SMART sensor, all data is recorded electronically and displayed graphically. The information is also reported all the project team members, making the process seamless.
Both from an educator and practitioner point of view, the inclusion of technology into the industry will not only assist in better decision making but also benefits future young professionals who are not only technology savvy, but also expect and readily accept it to use the information since they have the information at their fingertips.
[i] ASTM Standard C39, 2020, ” Standard Test Method for Obtaining and Testing Drilled Cores and Sawed Beams of Concrete Speciments” ASTM International, West Conshohocken, PA.”
CLOSING THOUGHT
The authors of this paper view SMART technology, such as the VAKKA-HT, as a huge win for the industry. The benefits of utilizing SMART technology in construction practices today will not only save but also challenges the upcoming graduates to think of ways to use the technology at hand and automate practices that can lead to new and better structures.
about the authors:
Dr. David Gress, PE, David Gress and Associated (retired Professor from University of New Hampshire), david.gress@unh.edu. Dr. Gress has a Ph.D. degree from Purdue University in Civil Engineering with an emphasis in Materials. His professional carrier has been based on concrete durability. He conducts experimental and analytical research on topics related to transportation materials, including the reuse of waste materials produced as byproducts of industry and when renewing the civil infrastructure. These research projects have included laboratory studies, full-scale field experiments, and demonstrations. Dr. David Gress is a materials engineer with special interests in the durability of concrete. Dr. Gress served as Dean of the Civil Engineering department at The University of New Hampshire for 10 years.
Malcolm K. Lim, PE, president and CEO, MLim Consulting, Inc. www.adeptgp.com, a forensic engineering company, a practice dedicated to supporting and resolving construction problems, formly Adept Group; he can be reached at mlim@adeptgp.com; he is also president of HGCR Technology LLC. Mr. Lim is a globally recognized expert and has practiced in the field of forensic engineering for more than 30 years. MLIM Consulting Inc. is a practice dedicated to supporting and resolving construction problems. MLIM provides investigative and testing services related to structural distress and materials issues through the use of the latest testing techniques and laboratory testing methods. Mr. Lim is a speaker and author. He has been invited to speak at conferences in the US, Zurich, Switzerland, London, England, Abu Dhabi, UAE, and Singapore. He has also authored a book for the NRC on investigations of Nuclear Power plants, especially with different nondestructive testing techniques. Mr. Lim is also the President of HGCR Technology LLC, a SMART technology company.
Modern Contractor Solutions, December 2020
Did you enjoy this article?
Subscribe to the FREE Digital Edition of Modern Contractor Solutions magazine.
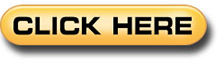