The old adage, “one size fits all,” normally does not apply to important trench safety equipment like trench shields and shoring. However, for two contractors, a more applicable adage would be, “one shoring system fits all sizes.”
Recently, North Florida-based Watson Construction LLC and South Carolina-based Terry R Lee Contracting completed projects in Gainesville, Florida, and Hardeeville, South Carolina, respectively. Both underground utility installation projects were very different from each other—a gas tank and a lift station—yet the projects did have one thing in common; they all used an Efficiency Production manufactured Slide Rail Shoring System rented and delivered from Efficiency Shoring & Supply in Jacksonville, Florida.
WATSON CONSTRUCTION
In December 2012, at the University of Florida’s Institute on Aging in Gainesville, Watson Construction installed a 36-foot-long, 10-foot-tall fiberglass collection tank. The project was slated as a LEED Platinum rated facility and the rainwater collection and reuse system was an integral part of achieving the Platinum rating.
The tank was installed at a moderate depth of 15 feet; however, depth wasn’t the primary challenge for Watson. The big challenge was contending with the surrounding structures, as the excavation site was crammed into the main building’s courtyard and had only limited access on three sides of the long pit.
“After careful consideration of the constraints of installing the tank, such as the tank’s length and the depth of the pit, plus the limited space, we chose the Slide Rail System by Efficiency Production,” says Steve Miller, Watson’s assistant operations manager. “It was almost a no brainer considering our past experiences with using the Efficiency system,” Watson adds.
Slide Rail is considered “positive shoring.” It is installed by sliding the panels into integrated rails on the posts, and then pushing the panels and posts incrementally down to grade as the pit is dug; a process commonly referred to as a “dig and push” shoring system.
With the help of Efficiency Shoring’s on-site installation team, Watson installed a 10-foot-wide, 41-foot-long, 16-feet-deep, two-bay, 4-Sided Multi-Bay™ configured Slide Rail System. Multi-Bay™ utilizes Efficiency’s exclusive Parallel Beams that roll up and down the slotted rail on the inside face of the linear posts and have spreader collars—like trench shield sidewalls—which pin standard trench box spreaders.
For the Watson project, tie-back waler i-beams were added at the top of the system, attach into integrated waler brackets that connect into a slotted rail on the outside face of the linear posts. Paired with a sacrificial member (such as a spreader pipe or timber beam) braced cross-trench against the bottom of the linear posts; the entire parallel beam spreader assembly can be completely removed, which provided Watson a full 40 feet of open space to install the 36-foot-long tank.
“The Slide Rail System proved efficient, effective, and easy to use,” says Watson’s project foreman, James Tilley. “I had never used a Slide Rail System before, but with help from the guys at Efficiency Shoring, it was as easy as any conventional trench box I’ve ever used, if not easier in this particular application,” Tilley says.
TERRY R LEE CONTRACTING
About 150 miles north of Jacksonville in the little town of Hardeeville, South Carolina, Terry R Lee Contracting was utilizing an Efficiency Slide Rail System on the Old Charleston CDBG Sewer Upgrade project for the Beaufort Jasper Water & Sewer Authority. However, Lee’s Slide Rail System was configured into a simple16 x 16 x 20-foot, 4-Sided Pit configuration, which shored the excavation for Lee to install a precast 6-foot-diameter, 20-foot-tall round lift station.
Though location and other project factors may change, excavation shoring challenges tend to run in patterns, such as dealing with surrounding structures and other environmental issues. “We were digging in a residential area so we had very little space; really only access on two sides of the pit,” explains project manager Bobby Lee. “We knew Slide Rail would be the best choice for the conditions; we’ve used (another manufacture’s) system before. However, we were convinced to try an Efficiency Production Slide Rail System now that they have a close dealership,” Lee says, referring to Efficiency Shoring & Supply’s Jacksonville Branch.
To help install the system, Efficiency Production sent its Special Operations Shoring Division’s senior slide rail installer, Tim Hurst, to assist Lee with the installation. “The Lee guys were great to work with; super hard working,” says Hurst. “They were able to get the entire system installed in a little over 5 hours, which is great time for a system that size.” ■
For More Information:
James McRay is the director of marketing and media for Efficiency Production, Inc. He can be reached at 800.552.8800; jmcray@efficiencyproduction.com. For more information, call Efficiency Shoring & Supply, 888.777.8307, or visit www.efficiencyshoring.com.
_________________________________________________________________________
Modern Contractor Solutions, January 2014
Did you enjoy this article?
Subscribe to the FREE Digital Edition of Modern Contractor Solutions magazine.
Shoring System Fits All Sizes
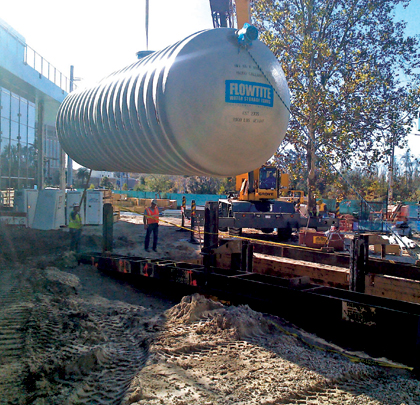